相关文档推荐
-
11.6分 | 4760阅读 | 4人下载
-
20.9分 | 3044阅读 | 3人下载
-
31.9分 | 13399阅读 | 6人下载
-
42.2分 | 13370阅读 | 3人下载
-
52.5分 | 10289阅读 | 14人下载
-
61.5分 | 7873阅读 | 8人下载
-
71.5分 | 7033阅读 | 5人下载
-
81.1分 | 6178阅读 | 4人下载
-
91.3分 | 6165阅读 | 8人下载
-
102.8分 | 5861阅读 | 1人下载
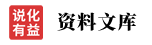
免费下载

阅读 5365

点赞 0

收藏 0

分享
微信扫一扫分享给朋友
铝合金阳极氧化与表面处理技术
铝合金阳极氧化与表面处理技术
第一章引论
1.铝及铝合金的性能特点
密度低;塑性好;易强化;导电好;耐腐蚀;易回收;可焊接;易表面处理
2.简述铝合金的腐蚀性及其腐蚀形态
1)腐蚀性:(1)酸性腐蚀:铝在不同的酸中有不同 腐蚀行为,一般在氧化性浓酸中生成钝化膜,具有很好的耐蚀性,而在稀酸中有“点腐蚀”现象。局部腐蚀;(2)碱性腐蚀:铝在碱性溶液中的腐蚀,碱能与氧化铝反应生成偏铝酸钠和水,然后再进一步与铝反应生成偏铝酸钠和氢气。全面腐蚀;(3)中性腐蚀:在中性盐溶液中,铝可以是钝态,也可能由于某些阳离子或者阳离子的作用发生腐蚀。点腐蚀。
2)腐蚀形态:点腐蚀,电偶腐蚀,缝隙腐蚀,晶间腐蚀,丝状腐蚀和层状腐蚀等
点腐蚀:最常见的腐蚀形态,程度与介质和合金有关
电偶腐蚀:接触腐蚀,异(双)金属腐蚀,在电解质溶液中,当两种金属或合金相接触(电导通)时,电位较负的金属腐蚀被加速,而电位较正的金属受到保护的腐蚀现象。
缝隙腐蚀:两个表面接触存在缝隙,该处充气溶解氧形成氧浓差原电池,使缝隙内产生腐蚀。
晶间腐蚀:与热处理不当有关,合金元素或金属间化合物沿晶界沉淀析出,相对于晶粒是阳极,而构成腐蚀电池。
丝状腐蚀:丝状腐蚀是一种膜下腐蚀,呈蠕虫状在膜下发展,这种膜可以是漆膜,或者其他涂层,一般不发生在阳极氧化膜的下面。丝状腐蚀与合金成分、涂层前预处理和环境因素有关,环境因素有适度、温度、氯化物;
层状腐蚀:剥层腐蚀,也叫剥蚀。
3.铝合金表面处理技术包括哪几个方面?
表面机械预处理(机械抛光或扫纹等)(2)化学预处理或化学处理(化学转化或化学镀等)(3)电化学处理(阳极氧化或电镀等)(4)物理处理(喷涂、搪瓷珐琅化及其物理表面技术改性)等。
搪瓷珐琅:将无机物的混合物熔融成不同熔点玻璃态物质。
4.铝合金阳极氧化膜的特性有哪些?
有:耐蚀性;硬度和耐磨性;装饰性;有机涂层和电镀层附着性;电绝缘性;透明性;功能性
第二章铝的表面机械预处理
1.预处理的目的:(1)提高良好的表观条件和表面精饰质量。(2)提高产品品级。(3)减少焊接的影响。(4)产生装饰效果。(5)获得干净表面。
2.磨光操作要求
(1)磨料种类和粒度的选择:根据工件材料的软硬程度、表面状况和质量要求等选用;表面越硬或越粗糙则用较硬及较粗的磨料。
(2)磨光应分多步操作,工件压向磨轮的压力要适度。
(3)新磨轮在黏结磨料前应预先刮削使之平衡后才能粘结磨料。
(4)定期更换新磨料。
(5)根据不同的需要选择合金材料。
(6)选择适当的磨轮转速,一般控制在10~14m/s。
(7)磨光效果取决于磨料、磨轮的刚性和轮子的旋转速度、工件与磨轮的接触压力等因素,以及实践经验和熟练技巧等。
3.磨光和抛光的概念
磨光:将布轮黏结磨料后的操作。目的:去除工件表面的毛刺、划痕、腐蚀斑点、砂眼、气孔等表观缺陷。;
抛光:将抛光膏抹于软布轮或毡轮后的操作
4.常见的问题和解决办法:
常见问题:“烧焦”印。
原因:(1)磨光轮、磨料和抛光剂的选择不当;(2)抛光用力不当;(3)磨触时间过长;(4)磨触过热。
措施:(1)在稀碱溶液中进行轻微的碱蚀;(2)用温和的酸浸蚀:如铬酸-硫酸溶液,或者质量分数为10%的硫酸溶液加温后使用;(3)3wt%Na2CO3和2wt%Na3PO4,溶液在40~50℃温度下处理,时间为5min,严重的可延长至10~15min
经上述处理清洗并干燥后,应立即用精抛轮或镜面抛光轮重新抛光。
预防:采用适当的磨光轮、抛光轮;采用适当的抛光剂;工件与抛轮的磨触时间要适当掌握。
第三章铝的化学预处理
1.铝材的脱脂方法有哪些?工艺原理分别是什么?
1)脱脂方法:酸性脱脂、碱性脱脂和有机溶剂脱脂。目的:清除铝表面的油脂和灰尘等污染物,使后道碱洗比较均匀,提高阳极氧化膜的质量
2)(1)酸性脱脂的作用机理:在以H2SO4、H3PO4和HNO3为基的酸性脱脂溶液中,油脂发生水解反应,生产甘油和相应的高级脂肪酸,达到脱脂的目的。(2)碱性脱脂的作用机理:碱与油脂发生皂化反应,生成可溶性的肥皂,用皂化反应消除油脂与铝材表面的结合,达到脱脂的目的。(3)有机溶剂脱脂的作用机理:利用油脂易溶于有机溶剂的特性进行,既能溶解皂化油,也能溶解非皂化油,具有很强的脱脂能力,且速度快,对铝无腐蚀性,达到脱脂的目的。
2.碱洗的目的、存在哪些缺陷?相应的对策应如何?
1)目的:去除表面的赃物,彻底去除铝表面的自然氧化膜,显露出纯净的金属基体,为后续的表面处理主工序做好准备。
2)碱洗的三大缺陷:外观粗糙、斑点、流痕。
3)(1)外观粗糙:是碱洗法生产砂面铝材时常见问题,常是由原始铝材存在组织缺陷(粗晶或金属间化合物沉淀粒子大)引起;提高原始铝材的内在组织质量才能从源头上解决问题。
原因:A:挤压用的铝棒原始晶粒尺寸大。B:铝棒加热温度偏高或挤压速度太快。C:采用的挤压机吨位偏小。 D:挤压后淬火不足。E:碱洗速度太快。
对策:选用晶粒度复合国家标准的挤压铝棒;控制好挤压制品的出口温度;加强挤压后的淬火;合理控制碱洗速度等。
(2)斑点:是铝材表面处理的致命缺陷:中断后续工序或报废回炉处理。
原因:
A:熔炼铸棒时加入回收铝的比例太高。Al2O3熔点高达2050℃,熔炼时不熔化,仅是破碎;碱洗过程中的浸蚀导致雪花状腐蚀斑点。 对策:控制阳极氧化膜的回收铝的比例,应小于10%;熔体的精炼除渣,铸造前熔体静止约25min和熔体过滤等。
B:水中氯离子含量高。当铝材的材质品质较差,而所用水的氯离子含量也较高时,碱洗或碱洗前后水洗都会显露出腐蚀斑点。 对策:改善原始铝材的材质;采用复合国家标准的自来水;改用硝酸或硝酸加硫酸除灰;在水槽镍加入1~5g/L HNO3也可有效抑制氯离子的腐蚀影响。
C:大气腐蚀。铝材在沿海大气环境中放置约3天、腐蚀性气氛熔炼炉旁、阴雨天气等其表面常有腐蚀斑痕或斑点形成。 对策:缩短原始铝材转入阳极氧化的周期时间;带阳极氧化的原始铝材放置在环境干燥、空气良好的位置;对长时间放置或阴雨天,可对原始铝材进行适当的遮盖处理等。
D:挤压“热斑”。铝材与出料台的导热良好的石墨辊相接触,因局部冷速不同,导致铝材内有析出相(Mg2Si相,温度范围400~250℃)形成,呈现间隔状斑点。 对策:控制挤压出料台的运行速度(应大于铝的挤出速度);采用导热效果差的其他耐热材料替代石墨辊;借枪风冷淬火力度;快速将挤压出口铝材降至250℃以下。
(3)流痕:碱洗工艺条件和操作不当造成碱洗流痕缺陷(碱洗速度太快和转移速度太慢)。 对策:A:加快转移。B:降低碱洗槽液温度。C:降低槽液中的NaOH浓度。D:铝材装料过密,应适当减少。
3.除灰的目的是什么?铝合金表面除灰有哪几种方法?
目的:去除表面挂灰,防止后道阳极氧化槽液的污染,提高氧化膜质量。
方法:硝酸除灰,硫酸除灰,
4.氟化物砂面处理的缺陷和对策是什么?
氟化物砂面处理是利用氟离子使铝材表面产生高度均匀、高密度点腐蚀的一种酸性浸蚀工艺。
缺陷与对策:
(1)上表面有斑痕:槽内沉淀物较多、氟离子浓度较低时,反应强度较弱,沉淀物在吕爱表面上沉积或停留过久,阻碍氟离子的正常腐蚀。
对策:清除槽内过多的沉淀物、降低铝材密度、添加适量的氟化氢铵和添加剂,提高氟离子浓度,增加反应强度。
(2)表面不易起砂:槽液受前道酸脱脂的污染而使PH降低,氟离子和添加剂浓度不足。 对策:用氨水或氟化铵调节PH值、补加氟化氢铵和添加剂等。
(3)表面沙粒太粗:槽内氟离子浓度太高或添加剂不足,或处理时间太长。
对策:采取相应的措施控制。
(4)表面光泽度有差异:槽工艺条件控制不当,或选用添加剂不适当,或铝材存在问题。 对策:采取相应的措施控制。
(5)局部不起砂:局部存在复合氧化膜。 对策:调整工艺流程,如磨光、抛光、重新酸洗或碱洗等。
第四章铝的化学抛光和电化学抛光
1.简述化学抛光和电化学抛光的机理的异同点。
1)化学抛光:通过控制铝材表面选择性的溶解,使表面微观凸部比凹部优先溶解,达到表面平整和光亮的目的。
2)电化学抛光,又称电解抛光。原理与化学抛光相似,依靠选择性溶解表面凸出部分而达到平整光滑,不同的是有外加电流作用,处理时间较短
3)共同点:抛光机理相同; 不同点:电化学抛光在处理过程中施加了电流,化学抛光使用的是化学氧化剂。
2.化学抛光和电化学抛光具有哪些优点?
化学抛光和电化学抛光与机械抛光相比较,具有如下优点:
(1)设备简单,工艺参数易调控,节省成本等以及表面更光亮;
(2)可处理大型零部件或大批量的小型零部件,以及复杂形状的工件;
(3)表面更洁净,无残留的机械抛光粉尘,具有良好的抗腐蚀性;
(4)化学抛光的表面镜面反射率更高,金属质感也较好,表面不会形成粉“霜”。
3.简述化学抛光和电化学抛光的缺陷和对策。
1)化学抛光缺陷及对策(以磷酸-硫酸-硝酸工艺为例)
(1)光亮度不足:铝材的成分影响、硝酸的含量影响等。
对策:采用高纯铝、控制硝酸的浓度,抛光前的铝材要干燥。
(2)白色附着物:铝溶解过多,需控制其在槽液中的含量。
对策:调整槽液中的溶铝量到正常范围。
(3)表面粗糙:硝酸含量过高,反应过于剧烈;或Cu含量过高。
对策:应严格控制硝酸含量;提高材质内部质量、减少添加剂量等。
(4)转移性腐蚀:化学抛光后转移到水洗过程中迟缓造成;
对策:应迅速转移至水中进行清洗。
(5)点腐蚀:绿箭表面气体累积形成气穴而产生;或因硝酸或Cu含量偏低造成。 对策:应合理装料,增加工件倾斜度,加强搅拌使气体逸出。清洗表面干净;控制硝酸含量等。
2)电化学抛光缺陷及对策(以磷酸-硫酸-铬酸工艺为例)
(1)电灼伤:导电借助面积不足、接触不良、工件通电电压上升过快、电流密度瞬间过大等; 对策:注意工件与电夹具接触良好、接触面积满足大电流需要,施加电压升压不宜过快等。
(2)暗斑:电流密度过低、电力线局部分布不均匀等
对策:装料量不宜过多、避免电力线分布不到的死角区等。
(3)气体条纹:气体逸出造成
对策:装料时使工件的每个面倾斜,装饰面垂直放置且朝向阴极、避免气体聚集等。
(4)冰晶状附着物:槽液中溶铝量太高或者磷酸含量高而形成磷酸铝沉淀。
对策:降低槽液中的溶铝量、或降低磷酸含量等
第五章
第六章铝阳极氧化与阳极氧化膜
1.铝阳极氧化膜分类:
(1)壁垒型:也叫屏蔽型或阻挡层氧化膜,紧靠金属表面,致密无孔、薄,厚度取决于氧化电压,不超过0.1μm,主要用于电解电容器。
(2)多孔型:由两层氧化膜组成,底层是阻挡层,与壁垒膜结构相同的致密无孔的薄氧化物层,厚度与电压有关;主体部分是多孔层结构,其厚度取决于通过的电量。
(阻挡层:指多孔型氧化膜的多孔层与金属铝分隔的,具有壁垒膜性质和生成规律的氧化层。)
2.多孔型氧化膜的厚度、结构和成分
多孔型阳极氧化膜组成:阻挡层和多孔层;阻挡层的结构和形成规律相当于壁垒型氧化膜;多孔层的生成规律、结构和成分与阻挡层完全不同。
1)阻挡层的厚度:取决于外加氧化电压,与氧化时间无关。成膜率或成膜比δb/Va ;壁垒型氧化膜的成膜率大于多孔型氧化膜的阻挡层的成膜率。
多孔层的厚度:总厚度=多孔层 + 阻挡层;总厚度与电流密度和氧化时间的乘积(即通过的电量)成正比
2)阻挡层的成分:致密无孔的非晶态氧化物。
多孔层的成分:非晶态的Al2O3,但不是纯的。
3)阻挡层的结构:双层结构。外层:含有溶液阴离子;内层:基本上由纯氧化铝组成。
多孔层结构:外层:含有γ-Al2O3和α-AlOOH;内层:非晶态Al2O3,水的渗入氧化膜逐渐转化为假勃姆体α-AlOOH。
第七章阳极氧化工艺
1.硫酸阳极氧化的工艺影响有哪些?
铝硫酸阳极氧化工艺参数的影响
(1)硫酸浓度的影响:影响氧化膜阻挡层厚度、电解液的导电性、对氧化膜的溶解作用、氧化膜的耐蚀性及后续的封孔质量等。
(浓度高对氧化膜的溶解作用大,形成的阻挡层薄,维持一定电流密度所需的电压降低;反之膜则厚,电压高。高浓度硫酸维持一定电流所需电压低,但对氧化膜的影响大。随硫酸浓度和温度上升,所需电压下降。但较高的硫酸浓度增加了酸对氧化膜的浸蚀。随硫酸浓度上升,效率降低:即获得一定厚度氧化膜的电耗大。随硫酸浓度增加,膜的耐蚀性和耐磨性降低)
(2)槽液温度的影响:1)槽液温度在一定范围内提高,获得的氧化膜种类减少,膜变软但较光亮;2)槽液温度较高,生成的氧化膜外层膜孔径和孔锥度趋于增大,造成封孔难度大,也易起封孔“粉霜”。3)较高槽液温度得到的氧化膜容易染色,但难保持颜色深浅的一致性,一般染色膜的氧化温度为20~25℃;4)降低槽液温度获得的氧化膜硬度高、耐磨性好,但在养护过程中维持同样电流密度所需电压较高,普通膜采用18~22℃。
(对于厚度大于15μm的氧化,槽液温度升高,膜质量和金属损失比显著减少,且膜的外层硬度较低。温度对氧化膜质量影响显著:温度高于15℃都是生产非晶体的软膜。温度低有助于制备致密的氧化膜。随温度升高,膜硬度下降。要获得硬度高、耐磨性好的膜层,必须采取低温阳极氧化。除3004合金外,一般合金在20℃时耐蚀性最好。随温度升高耐蚀性下降,40℃下降到最低。)
(3) 氧化电压的影响:电压决定氧化膜的孔径大小:低压——孔径小、孔数多——孔径大、孔数少。
(在一定范围内,高压有利于生成致密、均匀的氧化膜。在恒定电压下,电流密度随氧化时间延长而下降。维持一定电流所需的电压越高,则氧化过程所释放的热量就越多,不利于氧化膜性能稳定。电流一定时,温度越低电压越高。)
(4) 氧化电流的影响:氧化电流直接影响生产效率:高电流生产效率高。
(高电流需要电容量大的电容器,膜厚度波动大,易引起工件“烧伤”。
低电流下氧化时间长,使膜的耐蚀性和耐磨性下降。最佳电流为1.2~1.8A/dm2。硫酸浓度越高,槽液导电性好,同电压下的电流密度越大。铝含量增大,槽液电阻增大,导电性下降。)
(5)槽液搅拌的影响:为了使阳极氧化槽液温度和浓度均匀,特别是采用较大电流时,膜-槽液界面上产生大量热量,搅拌使界面温度降低。
(6) 氧化时间的影响:恒流下氧化,在一定时间内氧化膜厚度的增长与时间成正比。(根据:电解液浓度、槽液温度、电流密度、氧化膜厚度和性能要求等。)
2.简述硫酸、铬酸、磷酸、草酸硼酸和碱性等电解液的阳极氧化工艺特点和氧化膜性质差异。
1)硫酸工艺:生产成本低;膜的透明度高;耐蚀性和耐磨性好;电解着色和化学染色容易。2)铬酸工艺:氧化膜厚度一般,表面粗糙;膜层质软;耐磨性不然硫酸氢化膜,但弹性好。3)草酸工艺:氧化膜孔隙率低,耐蚀性、耐磨性和电绝缘性比硫酸膜好,但成本高。4)磷酸工艺:氧化膜较薄,而孔径较大。
3. 硫酸交流阳极氧化和硫酸直流阳极氧化比较
1)交流:电流效率低;氧化膜的耐蚀性差,硬度低。
2)直流:生产成本高;膜的透明度高;耐蚀性和耐磨性好;电解着色和化学染色容易。
4. 硫酸容易中铝离子和杂质的影响
主要是影响氧化膜的耐磨性、耐腐蚀性、光亮度和槽液导电性等
(1)铝离子:含量在1~10g/L 内是有利的,大于10g/L将造成影响。电流随铝离子浓度增大而减小;染色难度增大;铝含量较高时有不溶性的铝盐沉积于铝材工件表面、 槽壁和热交换器上,影响产品外观和热交换效率。
(2)阳离子Fe、MN、Cu和Ni等:
Fe:有害杂质,主要来源于硫酸和铝材。当Fe含量超过25~50μg/g时导致氧化膜出现很多问题:如光亮度下降、膜软松等。
Mn:影响与Fe相似,但没有Fe显著。
Cu和Ni:主要来源于合金化的铝材,它们影响相似,当含量超过100μg/g时,氧化膜耐蚀性降低。
(3)阴离子磷酸根、硝酸根、氯离子等:
磷酸根:化学抛光后水洗不足导致;含量很少时(ppm级)影响不大,含量多时主要危害是磷酸根被氧化膜吸附,而在水合封孔时释放出来,超过5μg/g时将会对封孔质量产生危害。
硝酸根:主要来源于前道工序后水洗不足和槽液商品硫酸。当含量超过30μg/g时对光亮度不利,过高还会使槽液溶解能力增强不利于成膜。
氯离子:主要来源于使用的水,自来水中氯离子含量较高。当Cl-和F-超过50μg/g时氧化膜产生腐蚀斑点。
第八章铝的硬质阳极氧化
1.简述硬质阳极氧化膜与普通氧化膜的制备工艺参数的异同点。
硬质阳极氧化膜的制备:与普通的阳极氧化原理、设备和工艺等无本质区别,仅是具体工艺措施方面略有区别。区别:降低氧化过程中氧化膜的溶解速度。
2.硬质阳极氧化莫与普通阳极氧化膜比较
硬质阳极氧化膜厚度大、硬度比较高、耐磨性较好、孔隙率较低、耐击穿电压较高、而表面平整性稍差。(外加电压大,浓度低,处理时间长,则膜厚,硬度高,耐磨性好,耐击穿电压高,孔隙率低,孔径大,表面平整性差。)
3.铸造铝合金的硬质阳极氧化工艺与硫酸等硬质阳极氧化工艺的异同点。
(1)槽液温度低:小于5℃,温度越低膜硬度越高。普通硫酸阳极氧化的槽液温度在20℃左右。(2)槽液浓度低:对于硫酸一般小于15%;普通阳极氧化的槽液浓度在20%左右。(3)硫酸槽液中添加有机酸:草酸、酒石酸、柠檬酸等;(4)外加电流/电压较高:2~5A/dm2,25~100V。普通阳极氧化1.0~1.5 A/dm2,18V以下;(5)逐步递增电压的操作方法:阶梯式加压;(6)采用脉冲电源或特殊波形电源:高Cu合金或高Si铸造铝合金。
第九章
第十章铝阳极氧化膜的电解着色
1.简述Sn盐与Ni盐电解着色的工艺及其优缺点
1)Sn盐电解着色工艺:主要是单Sn盐、Sn-Ni混合电解着色,主要的着色盐是SnSO4,利用Sn2+点解还原在阳极氧化莫的微孔中析出而着色。优点:Sn盐的抗杂质性能好,点解着色溶液分布能力强,工业控制简单,交流Sn盐着色本身不存在困难。缺点:Sn2+稳定性差,着色的色差和色调比较难以控制。
2)Ni盐点解着色工业:与Sn盐电解着色工业相似,析出Ni而着色。优点:Ni盐着色速度快,槽液稳定性好。缺点:对槽液的杂质比较敏感
2.交流与直流电解着色的优缺点。
1)交流着色。优点:克服了直流电解着色存在氧化膜剥落的危险。
缺点:在交流着色中阳极电压会影响阴极着色反应的速度,使得阳极电流密度下降,阴极电流密度减小,从而 着色速度减慢。
2)直流着色。优点:着色速度快,电能利用率高;缺点:直流电解着色存在氧化膜剥落的危险。
第十一章铝阳极氧化膜的染色
1.氧化膜应具有哪些条件才能进行染色处理
(1)铝在硫酸溶液中得到的阳极氧化膜无色而多孔;
(2)氧化膜应具备一定的厚度,应大于7um;
(3)氧化膜应具有一定的松孔和吸附性;
(4)氧化膜层应完整、均匀,不应有划伤、沙眼、点腐蚀等缺陷;
(5)氧化膜本身具有合适的颜色,且没有金相结构的差别,如晶粒大小不一或严重偏析等。
2.简述有机涂料和无机涂料的染色机理。
(1)有机染料的染色基于物质的吸附理论,有物理吸附和化学吸附。
物理吸附:分子或离子以静电力方式的吸附。氧化膜的组成是非晶态的氧化铝,内层靠近铝基体的为致密的阻挡层,上面生长着呈喇叭状向外开张的多孔型结构,呈现出优良的物理吸附性能,当染料分子进入膜孔时,就被吸附在孔壁上。
化学吸附:以化学力方式的吸附。此时有机染料分子与氧化铝发生了化学反应,由于化学结合而存在于膜孔中。这种吸附有以下几种:氧化膜与染料分子上的磺基形成共价键;氧化膜与染料分子上的酚基形成氢键;氧化膜与染料分子生成络合物。
(2)无极染料染色机理:染色时将氧化后的工件按照一定的次序先浸渍在一种无机盐溶液中,再依次浸入另一种无机盐溶液中,使这些无机物在膜孔中发生化学反应生成不溶于水的有色化合物,填塞氧化膜孔隙封住,因而使膜层现颜色。
3.有机染料染色工艺的流程与规范。
工艺流程:前处理-阳极氧化-清洗-氨水中和或其他处理-清洗-染色-清洗-封孔处理-烘干。
工艺规范:1)染色容易的浓度:染浅色调,浓度一般控制在0.1~1g/L,而染深色要求2~5 g/L,染黑色要求10 g/L以上;2)染色溶液的温度:一般控制在50~70℃;3)染色溶液的PH值:PH范围5~6;4)染色时间:通常为5~15min。
4.有机染色工艺中染色液的杂质影响及其控制。
(1)硫酸钠的影响:硫酸钠降低染色速率,这种影响随染料离子中硫磺基团的增加而增加,特别是金属络合物染料。
(2)氯化钠的影响:引起电蚀点(白点)的主要原因。电蚀点被阴极电流所抑制。
(3)表面活性剂的影响:非离子型表面活性剂对染色无影响,但阳离子表面活性剂如加入铝黑MLW中会减慢染色,故除油剂中不适宜添加离子型表面活性剂,因某些阴离子对染色不利。
(4)三价铝离子的影响:少量Al3+ 对许多染液无影响,除非达到500~1000ug/g,此时可能造成变色,如蓝色变成带红等。
(5)重金属离子的影响。
(6)阴离子的影响。
(7)细菌作用对染色的影响:细菌在染液中繁殖,使染液发霉,首先在染液表面起小泡,当染液不工作静置时,在泡的周围聚集一些不溶解的有色颗粒,使染色不正常。假如肉眼可见,应将悬浮于表面的发霉物捞掉,并加入0.05~0.10g/L合适的杀菌剂,如二氯酚G4,用乙醇溶液溶解后加入槽中。有时只有将染液倒掉。此时应用杀菌剂或次氯酸溶液清洗槽壁,然后重新配置。
(8)不溶杂质对染色的影响:染色液中有时不可避免地会带入油污,玷污工件使染色发花,此时应用吸油纸吸沾除去或加入少量非离子表面活性剂,使油滴分散不致聚集在染液表面。
5.列举常用的无机染色工艺及其步骤与参数(至少五种颜色以上)
6.
一般在常温下进行操作,通常分两步进行,现在第一种溶液中浸5~10min,取出清洗后再在第二种溶液中浸5~10min,则染成所需的颜色。
常用无机染色工艺规范
色彩
溶液成分
含量/(g/L)
生成有色盐
蓝色
1亚铁氰化钾[K4Fe(CN)6.3H2O]
2三氯化铁[FeCl3]或者硫酸铁[Fe2(SO4)2]
30~50
40~50
亚铁氰化铁(普鲁士蓝)
黑色
①醋酸钴[CoAc2]
②高锰酸钾[KMnO4]
50~100
15~25
氧化钴
黄色
①醋酸铅[PbAc2.3H2O]
②重铬酸钾[K2Cr2O7]
100~200
50~100
铬酸铅
白色
①醋酸铅[PbAc2.3H2O]
②硫酸钠[Na2SO4]
10~50
10~50
硫酸铅
褐色
①铁氰化钾[K3Fe(CN)6]
②硫酸铜[CuSO4.5H2O]
10~50
10~100
铁青华铜
金色
草酸高铁铵[NH4Fe(C2O4)2](Ph=4.8~5.3,35~50oC,2min)
10(浅)
25(深)
7.染色常见的问题以及解决方法。
1)不上色 。 解决办法:a、调换颜料 b、调整PH c、提高膜层厚度 d、及时染色 e、选用合适颜料。
2)部分着不上色或颜色浅。 解决办法: a、加强保护措施 b、提高颜料浓度 c、提高膜层厚度 d、夹紧工件,调正位置 e、调换着色液 f、改进颜料溶解。
3)染色后表面呈白色水雾状。 解决办法: a、去除水汽 b、调整褪色液浓度 c、缩短褪色时间。
4)染色后发花。 解决办法:a、调整PH 加强清洗 b、改进颜料溶解 c、降低染液温度。
5)染色后有点状。 解决办法: a、用水冲洗试样表面 b、过滤染液 c、氧化后工件放入清水槽 d、加强防护。
6)染色后易褪色。 解决办法: a、调高PH b、提高染色槽温度,延长染色时间,调整封孔槽PH,延长封孔时间。
7)染色表面易擦掉。 解决办法:a、重新氧化 b、提高染色液温度 c、调高氧化温度。
8)染色过暗。 解决办法:a、冲稀染液 b、降低温度 c、缩短时间。
第十二章 铝阳极氧化膜的封孔
1.封孔:铝阳极氧化后对氧化膜进行的化学或物理过程,以降低氧化膜的孔隙率和吸附能力。其封孔原理主要有(1)水合反应 ;(2)无机物充填;(3)有机物充填。
2.热封孔技术是通过氧化铝的水合反应,将非晶态氧化铝转化为称为勃姆体的水合氧化铝,即Al2O3•H2O(AlOOH)。 热封孔的机理本质是水合反应,常称为“水合-热封孔”。
3.水合反应的作用:体积膨胀了30%,体积增大使氧化膜的微孔得到填充和封闭,抗污染性和耐腐蚀性随之提高,同时导纳降低(阻抗增加),介电常数变大
4.水中杂质的的影响:1)封孔的效果很大程度上取决于水的质量和PH控制;
2)常见的杂质:SiO2、H2SiO3;3)措施:离子交换 。
5.沸水封孔参数和冷封孔参数比较
1)沸水封孔的温度:一般95度以上。冷封孔为室温;2)沸水封孔的PH值:最佳范围5.5~6.5。冷封孔范围5.5~6.5,工业控制以6为最佳。3)沸水封孔的时间:取决于膜厚、孔径大小和封孔品质试验要求。冷封孔一般规定为10~15min。
第十八章
1.简述常用的阳极氧化膜质量检测方法及其优点
1)外观和色差 检测方法:目视和仪器检测法 优缺点:目视法简单,但易受试样的形状和大小,照光的强弱等因素的影响 仪器法解决了目视法的缺点,适用于测定反射光的颜色。
2)氧化膜的厚度 测量方法:a、横断面厚度显微镜测量法:膜厚大于5um, 垂直 b、分光束显微镜测量法:膜厚大于5um,氧化膜折射率1.59~1.62 c、质量损失法:膜厚小于5um,溶解法,表面密度,氧化膜密度(硫酸液氧化)封闭前后为2.6和2.4g\cm3 d、涡流法:不适用于薄的膜
3)封孔质量:a、指印试验 b、酸处理后染色斑点质量,不适用于cu高于2%和si高于4%的含量 c、磷铬酸实验
4)耐蚀性:a、盐雾腐蚀试验 b、含SO2潮湿大气腐蚀试验 c、马丘腐蚀试验 d、耐湿热腐蚀试验 e、滴碱腐蚀试验
5)耐化学稳定性:a、耐酸实验 b、耐碱实验 c、耐砂浆试验
6)耐候性:a、自然暴露实验 b、人工加速耐候实验
7)硬度:a、压痕硬度 b、铅笔硬度 c、显微硬度
8)耐磨性:a、喷磨试验仪检测耐磨性 b、轮式磨损试验仪检测耐磨性 c、落砂试验仪检测耐磨性
9)附着性:a、划格实验 b、仪器实验:划痕法
10)力学性能:a、耐冲击性 b、抗弯曲性 c、疲劳性能 d、结合强度 e、抗变形破裂 f、抗热裂性
11)电绝缘性:击穿电位法
12)反光性能
13)其他:a、涂层聚合作用性能 b、耐沸水性 c、加工性能
2.耐磨性影响因素:合金成分、膜厚、高聚合物涂料的固化条件、阳极氧化条件和封孔条件等
第一章引论
1.铝及铝合金的性能特点
密度低;塑性好;易强化;导电好;耐腐蚀;易回收;可焊接;易表面处理
2.简述铝合金的腐蚀性及其腐蚀形态
1)腐蚀性:(1)酸性腐蚀:铝在不同的酸中有不同 腐蚀行为,一般在氧化性浓酸中生成钝化膜,具有很好的耐蚀性,而在稀酸中有“点腐蚀”现象。局部腐蚀;(2)碱性腐蚀:铝在碱性溶液中的腐蚀,碱能与氧化铝反应生成偏铝酸钠和水,然后再进一步与铝反应生成偏铝酸钠和氢气。全面腐蚀;(3)中性腐蚀:在中性盐溶液中,铝可以是钝态,也可能由于某些阳离子或者阳离子的作用发生腐蚀。点腐蚀。
2)腐蚀形态:点腐蚀,电偶腐蚀,缝隙腐蚀,晶间腐蚀,丝状腐蚀和层状腐蚀等
点腐蚀:最常见的腐蚀形态,程度与介质和合金有关
电偶腐蚀:接触腐蚀,异(双)金属腐蚀,在电解质溶液中,当两种金属或合金相接触(电导通)时,电位较负的金属腐蚀被加速,而电位较正的金属受到保护的腐蚀现象。
缝隙腐蚀:两个表面接触存在缝隙,该处充气溶解氧形成氧浓差原电池,使缝隙内产生腐蚀。
晶间腐蚀:与热处理不当有关,合金元素或金属间化合物沿晶界沉淀析出,相对于晶粒是阳极,而构成腐蚀电池。
丝状腐蚀:丝状腐蚀是一种膜下腐蚀,呈蠕虫状在膜下发展,这种膜可以是漆膜,或者其他涂层,一般不发生在阳极氧化膜的下面。丝状腐蚀与合金成分、涂层前预处理和环境因素有关,环境因素有适度、温度、氯化物;
层状腐蚀:剥层腐蚀,也叫剥蚀。
3.铝合金表面处理技术包括哪几个方面?
表面机械预处理(机械抛光或扫纹等)(2)化学预处理或化学处理(化学转化或化学镀等)(3)电化学处理(阳极氧化或电镀等)(4)物理处理(喷涂、搪瓷珐琅化及其物理表面技术改性)等。
搪瓷珐琅:将无机物的混合物熔融成不同熔点玻璃态物质。
4.铝合金阳极氧化膜的特性有哪些?
有:耐蚀性;硬度和耐磨性;装饰性;有机涂层和电镀层附着性;电绝缘性;透明性;功能性
第二章铝的表面机械预处理
1.预处理的目的:(1)提高良好的表观条件和表面精饰质量。(2)提高产品品级。(3)减少焊接的影响。(4)产生装饰效果。(5)获得干净表面。
2.磨光操作要求
(1)磨料种类和粒度的选择:根据工件材料的软硬程度、表面状况和质量要求等选用;表面越硬或越粗糙则用较硬及较粗的磨料。
(2)磨光应分多步操作,工件压向磨轮的压力要适度。
(3)新磨轮在黏结磨料前应预先刮削使之平衡后才能粘结磨料。
(4)定期更换新磨料。
(5)根据不同的需要选择合金材料。
(6)选择适当的磨轮转速,一般控制在10~14m/s。
(7)磨光效果取决于磨料、磨轮的刚性和轮子的旋转速度、工件与磨轮的接触压力等因素,以及实践经验和熟练技巧等。
3.磨光和抛光的概念
磨光:将布轮黏结磨料后的操作。目的:去除工件表面的毛刺、划痕、腐蚀斑点、砂眼、气孔等表观缺陷。;
抛光:将抛光膏抹于软布轮或毡轮后的操作
4.常见的问题和解决办法:
常见问题:“烧焦”印。
原因:(1)磨光轮、磨料和抛光剂的选择不当;(2)抛光用力不当;(3)磨触时间过长;(4)磨触过热。
措施:(1)在稀碱溶液中进行轻微的碱蚀;(2)用温和的酸浸蚀:如铬酸-硫酸溶液,或者质量分数为10%的硫酸溶液加温后使用;(3)3wt%Na2CO3和2wt%Na3PO4,溶液在40~50℃温度下处理,时间为5min,严重的可延长至10~15min
经上述处理清洗并干燥后,应立即用精抛轮或镜面抛光轮重新抛光。
预防:采用适当的磨光轮、抛光轮;采用适当的抛光剂;工件与抛轮的磨触时间要适当掌握。
第三章铝的化学预处理
1.铝材的脱脂方法有哪些?工艺原理分别是什么?
1)脱脂方法:酸性脱脂、碱性脱脂和有机溶剂脱脂。目的:清除铝表面的油脂和灰尘等污染物,使后道碱洗比较均匀,提高阳极氧化膜的质量
2)(1)酸性脱脂的作用机理:在以H2SO4、H3PO4和HNO3为基的酸性脱脂溶液中,油脂发生水解反应,生产甘油和相应的高级脂肪酸,达到脱脂的目的。(2)碱性脱脂的作用机理:碱与油脂发生皂化反应,生成可溶性的肥皂,用皂化反应消除油脂与铝材表面的结合,达到脱脂的目的。(3)有机溶剂脱脂的作用机理:利用油脂易溶于有机溶剂的特性进行,既能溶解皂化油,也能溶解非皂化油,具有很强的脱脂能力,且速度快,对铝无腐蚀性,达到脱脂的目的。
2.碱洗的目的、存在哪些缺陷?相应的对策应如何?
1)目的:去除表面的赃物,彻底去除铝表面的自然氧化膜,显露出纯净的金属基体,为后续的表面处理主工序做好准备。
2)碱洗的三大缺陷:外观粗糙、斑点、流痕。
3)(1)外观粗糙:是碱洗法生产砂面铝材时常见问题,常是由原始铝材存在组织缺陷(粗晶或金属间化合物沉淀粒子大)引起;提高原始铝材的内在组织质量才能从源头上解决问题。
原因:A:挤压用的铝棒原始晶粒尺寸大。B:铝棒加热温度偏高或挤压速度太快。C:采用的挤压机吨位偏小。 D:挤压后淬火不足。E:碱洗速度太快。
对策:选用晶粒度复合国家标准的挤压铝棒;控制好挤压制品的出口温度;加强挤压后的淬火;合理控制碱洗速度等。
(2)斑点:是铝材表面处理的致命缺陷:中断后续工序或报废回炉处理。
原因:
A:熔炼铸棒时加入回收铝的比例太高。Al2O3熔点高达2050℃,熔炼时不熔化,仅是破碎;碱洗过程中的浸蚀导致雪花状腐蚀斑点。 对策:控制阳极氧化膜的回收铝的比例,应小于10%;熔体的精炼除渣,铸造前熔体静止约25min和熔体过滤等。
B:水中氯离子含量高。当铝材的材质品质较差,而所用水的氯离子含量也较高时,碱洗或碱洗前后水洗都会显露出腐蚀斑点。 对策:改善原始铝材的材质;采用复合国家标准的自来水;改用硝酸或硝酸加硫酸除灰;在水槽镍加入1~5g/L HNO3也可有效抑制氯离子的腐蚀影响。
C:大气腐蚀。铝材在沿海大气环境中放置约3天、腐蚀性气氛熔炼炉旁、阴雨天气等其表面常有腐蚀斑痕或斑点形成。 对策:缩短原始铝材转入阳极氧化的周期时间;带阳极氧化的原始铝材放置在环境干燥、空气良好的位置;对长时间放置或阴雨天,可对原始铝材进行适当的遮盖处理等。
D:挤压“热斑”。铝材与出料台的导热良好的石墨辊相接触,因局部冷速不同,导致铝材内有析出相(Mg2Si相,温度范围400~250℃)形成,呈现间隔状斑点。 对策:控制挤压出料台的运行速度(应大于铝的挤出速度);采用导热效果差的其他耐热材料替代石墨辊;借枪风冷淬火力度;快速将挤压出口铝材降至250℃以下。
(3)流痕:碱洗工艺条件和操作不当造成碱洗流痕缺陷(碱洗速度太快和转移速度太慢)。 对策:A:加快转移。B:降低碱洗槽液温度。C:降低槽液中的NaOH浓度。D:铝材装料过密,应适当减少。
3.除灰的目的是什么?铝合金表面除灰有哪几种方法?
目的:去除表面挂灰,防止后道阳极氧化槽液的污染,提高氧化膜质量。
方法:硝酸除灰,硫酸除灰,
4.氟化物砂面处理的缺陷和对策是什么?
氟化物砂面处理是利用氟离子使铝材表面产生高度均匀、高密度点腐蚀的一种酸性浸蚀工艺。
缺陷与对策:
(1)上表面有斑痕:槽内沉淀物较多、氟离子浓度较低时,反应强度较弱,沉淀物在吕爱表面上沉积或停留过久,阻碍氟离子的正常腐蚀。
对策:清除槽内过多的沉淀物、降低铝材密度、添加适量的氟化氢铵和添加剂,提高氟离子浓度,增加反应强度。
(2)表面不易起砂:槽液受前道酸脱脂的污染而使PH降低,氟离子和添加剂浓度不足。 对策:用氨水或氟化铵调节PH值、补加氟化氢铵和添加剂等。
(3)表面沙粒太粗:槽内氟离子浓度太高或添加剂不足,或处理时间太长。
对策:采取相应的措施控制。
(4)表面光泽度有差异:槽工艺条件控制不当,或选用添加剂不适当,或铝材存在问题。 对策:采取相应的措施控制。
(5)局部不起砂:局部存在复合氧化膜。 对策:调整工艺流程,如磨光、抛光、重新酸洗或碱洗等。
第四章铝的化学抛光和电化学抛光
1.简述化学抛光和电化学抛光的机理的异同点。
1)化学抛光:通过控制铝材表面选择性的溶解,使表面微观凸部比凹部优先溶解,达到表面平整和光亮的目的。
2)电化学抛光,又称电解抛光。原理与化学抛光相似,依靠选择性溶解表面凸出部分而达到平整光滑,不同的是有外加电流作用,处理时间较短
3)共同点:抛光机理相同; 不同点:电化学抛光在处理过程中施加了电流,化学抛光使用的是化学氧化剂。
2.化学抛光和电化学抛光具有哪些优点?
化学抛光和电化学抛光与机械抛光相比较,具有如下优点:
(1)设备简单,工艺参数易调控,节省成本等以及表面更光亮;
(2)可处理大型零部件或大批量的小型零部件,以及复杂形状的工件;
(3)表面更洁净,无残留的机械抛光粉尘,具有良好的抗腐蚀性;
(4)化学抛光的表面镜面反射率更高,金属质感也较好,表面不会形成粉“霜”。
3.简述化学抛光和电化学抛光的缺陷和对策。
1)化学抛光缺陷及对策(以磷酸-硫酸-硝酸工艺为例)
(1)光亮度不足:铝材的成分影响、硝酸的含量影响等。
对策:采用高纯铝、控制硝酸的浓度,抛光前的铝材要干燥。
(2)白色附着物:铝溶解过多,需控制其在槽液中的含量。
对策:调整槽液中的溶铝量到正常范围。
(3)表面粗糙:硝酸含量过高,反应过于剧烈;或Cu含量过高。
对策:应严格控制硝酸含量;提高材质内部质量、减少添加剂量等。
(4)转移性腐蚀:化学抛光后转移到水洗过程中迟缓造成;
对策:应迅速转移至水中进行清洗。
(5)点腐蚀:绿箭表面气体累积形成气穴而产生;或因硝酸或Cu含量偏低造成。 对策:应合理装料,增加工件倾斜度,加强搅拌使气体逸出。清洗表面干净;控制硝酸含量等。
2)电化学抛光缺陷及对策(以磷酸-硫酸-铬酸工艺为例)
(1)电灼伤:导电借助面积不足、接触不良、工件通电电压上升过快、电流密度瞬间过大等; 对策:注意工件与电夹具接触良好、接触面积满足大电流需要,施加电压升压不宜过快等。
(2)暗斑:电流密度过低、电力线局部分布不均匀等
对策:装料量不宜过多、避免电力线分布不到的死角区等。
(3)气体条纹:气体逸出造成
对策:装料时使工件的每个面倾斜,装饰面垂直放置且朝向阴极、避免气体聚集等。
(4)冰晶状附着物:槽液中溶铝量太高或者磷酸含量高而形成磷酸铝沉淀。
对策:降低槽液中的溶铝量、或降低磷酸含量等
第五章
第六章铝阳极氧化与阳极氧化膜
1.铝阳极氧化膜分类:
(1)壁垒型:也叫屏蔽型或阻挡层氧化膜,紧靠金属表面,致密无孔、薄,厚度取决于氧化电压,不超过0.1μm,主要用于电解电容器。
(2)多孔型:由两层氧化膜组成,底层是阻挡层,与壁垒膜结构相同的致密无孔的薄氧化物层,厚度与电压有关;主体部分是多孔层结构,其厚度取决于通过的电量。
(阻挡层:指多孔型氧化膜的多孔层与金属铝分隔的,具有壁垒膜性质和生成规律的氧化层。)
2.多孔型氧化膜的厚度、结构和成分
多孔型阳极氧化膜组成:阻挡层和多孔层;阻挡层的结构和形成规律相当于壁垒型氧化膜;多孔层的生成规律、结构和成分与阻挡层完全不同。
1)阻挡层的厚度:取决于外加氧化电压,与氧化时间无关。成膜率或成膜比δb/Va ;壁垒型氧化膜的成膜率大于多孔型氧化膜的阻挡层的成膜率。
多孔层的厚度:总厚度=多孔层 + 阻挡层;总厚度与电流密度和氧化时间的乘积(即通过的电量)成正比
2)阻挡层的成分:致密无孔的非晶态氧化物。
多孔层的成分:非晶态的Al2O3,但不是纯的。
3)阻挡层的结构:双层结构。外层:含有溶液阴离子;内层:基本上由纯氧化铝组成。
多孔层结构:外层:含有γ-Al2O3和α-AlOOH;内层:非晶态Al2O3,水的渗入氧化膜逐渐转化为假勃姆体α-AlOOH。
第七章阳极氧化工艺
1.硫酸阳极氧化的工艺影响有哪些?
铝硫酸阳极氧化工艺参数的影响
(1)硫酸浓度的影响:影响氧化膜阻挡层厚度、电解液的导电性、对氧化膜的溶解作用、氧化膜的耐蚀性及后续的封孔质量等。
(浓度高对氧化膜的溶解作用大,形成的阻挡层薄,维持一定电流密度所需的电压降低;反之膜则厚,电压高。高浓度硫酸维持一定电流所需电压低,但对氧化膜的影响大。随硫酸浓度和温度上升,所需电压下降。但较高的硫酸浓度增加了酸对氧化膜的浸蚀。随硫酸浓度上升,效率降低:即获得一定厚度氧化膜的电耗大。随硫酸浓度增加,膜的耐蚀性和耐磨性降低)
(2)槽液温度的影响:1)槽液温度在一定范围内提高,获得的氧化膜种类减少,膜变软但较光亮;2)槽液温度较高,生成的氧化膜外层膜孔径和孔锥度趋于增大,造成封孔难度大,也易起封孔“粉霜”。3)较高槽液温度得到的氧化膜容易染色,但难保持颜色深浅的一致性,一般染色膜的氧化温度为20~25℃;4)降低槽液温度获得的氧化膜硬度高、耐磨性好,但在养护过程中维持同样电流密度所需电压较高,普通膜采用18~22℃。
(对于厚度大于15μm的氧化,槽液温度升高,膜质量和金属损失比显著减少,且膜的外层硬度较低。温度对氧化膜质量影响显著:温度高于15℃都是生产非晶体的软膜。温度低有助于制备致密的氧化膜。随温度升高,膜硬度下降。要获得硬度高、耐磨性好的膜层,必须采取低温阳极氧化。除3004合金外,一般合金在20℃时耐蚀性最好。随温度升高耐蚀性下降,40℃下降到最低。)
(3) 氧化电压的影响:电压决定氧化膜的孔径大小:低压——孔径小、孔数多——孔径大、孔数少。
(在一定范围内,高压有利于生成致密、均匀的氧化膜。在恒定电压下,电流密度随氧化时间延长而下降。维持一定电流所需的电压越高,则氧化过程所释放的热量就越多,不利于氧化膜性能稳定。电流一定时,温度越低电压越高。)
(4) 氧化电流的影响:氧化电流直接影响生产效率:高电流生产效率高。
(高电流需要电容量大的电容器,膜厚度波动大,易引起工件“烧伤”。
低电流下氧化时间长,使膜的耐蚀性和耐磨性下降。最佳电流为1.2~1.8A/dm2。硫酸浓度越高,槽液导电性好,同电压下的电流密度越大。铝含量增大,槽液电阻增大,导电性下降。)
(5)槽液搅拌的影响:为了使阳极氧化槽液温度和浓度均匀,特别是采用较大电流时,膜-槽液界面上产生大量热量,搅拌使界面温度降低。
(6) 氧化时间的影响:恒流下氧化,在一定时间内氧化膜厚度的增长与时间成正比。(根据:电解液浓度、槽液温度、电流密度、氧化膜厚度和性能要求等。)
2.简述硫酸、铬酸、磷酸、草酸硼酸和碱性等电解液的阳极氧化工艺特点和氧化膜性质差异。
1)硫酸工艺:生产成本低;膜的透明度高;耐蚀性和耐磨性好;电解着色和化学染色容易。2)铬酸工艺:氧化膜厚度一般,表面粗糙;膜层质软;耐磨性不然硫酸氢化膜,但弹性好。3)草酸工艺:氧化膜孔隙率低,耐蚀性、耐磨性和电绝缘性比硫酸膜好,但成本高。4)磷酸工艺:氧化膜较薄,而孔径较大。
3. 硫酸交流阳极氧化和硫酸直流阳极氧化比较
1)交流:电流效率低;氧化膜的耐蚀性差,硬度低。
2)直流:生产成本高;膜的透明度高;耐蚀性和耐磨性好;电解着色和化学染色容易。
4. 硫酸容易中铝离子和杂质的影响
主要是影响氧化膜的耐磨性、耐腐蚀性、光亮度和槽液导电性等
(1)铝离子:含量在1~10g/L 内是有利的,大于10g/L将造成影响。电流随铝离子浓度增大而减小;染色难度增大;铝含量较高时有不溶性的铝盐沉积于铝材工件表面、 槽壁和热交换器上,影响产品外观和热交换效率。
(2)阳离子Fe、MN、Cu和Ni等:
Fe:有害杂质,主要来源于硫酸和铝材。当Fe含量超过25~50μg/g时导致氧化膜出现很多问题:如光亮度下降、膜软松等。
Mn:影响与Fe相似,但没有Fe显著。
Cu和Ni:主要来源于合金化的铝材,它们影响相似,当含量超过100μg/g时,氧化膜耐蚀性降低。
(3)阴离子磷酸根、硝酸根、氯离子等:
磷酸根:化学抛光后水洗不足导致;含量很少时(ppm级)影响不大,含量多时主要危害是磷酸根被氧化膜吸附,而在水合封孔时释放出来,超过5μg/g时将会对封孔质量产生危害。
硝酸根:主要来源于前道工序后水洗不足和槽液商品硫酸。当含量超过30μg/g时对光亮度不利,过高还会使槽液溶解能力增强不利于成膜。
氯离子:主要来源于使用的水,自来水中氯离子含量较高。当Cl-和F-超过50μg/g时氧化膜产生腐蚀斑点。
第八章铝的硬质阳极氧化
1.简述硬质阳极氧化膜与普通氧化膜的制备工艺参数的异同点。
硬质阳极氧化膜的制备:与普通的阳极氧化原理、设备和工艺等无本质区别,仅是具体工艺措施方面略有区别。区别:降低氧化过程中氧化膜的溶解速度。
2.硬质阳极氧化莫与普通阳极氧化膜比较
硬质阳极氧化膜厚度大、硬度比较高、耐磨性较好、孔隙率较低、耐击穿电压较高、而表面平整性稍差。(外加电压大,浓度低,处理时间长,则膜厚,硬度高,耐磨性好,耐击穿电压高,孔隙率低,孔径大,表面平整性差。)
3.铸造铝合金的硬质阳极氧化工艺与硫酸等硬质阳极氧化工艺的异同点。
(1)槽液温度低:小于5℃,温度越低膜硬度越高。普通硫酸阳极氧化的槽液温度在20℃左右。(2)槽液浓度低:对于硫酸一般小于15%;普通阳极氧化的槽液浓度在20%左右。(3)硫酸槽液中添加有机酸:草酸、酒石酸、柠檬酸等;(4)外加电流/电压较高:2~5A/dm2,25~100V。普通阳极氧化1.0~1.5 A/dm2,18V以下;(5)逐步递增电压的操作方法:阶梯式加压;(6)采用脉冲电源或特殊波形电源:高Cu合金或高Si铸造铝合金。
第九章
第十章铝阳极氧化膜的电解着色
1.简述Sn盐与Ni盐电解着色的工艺及其优缺点
1)Sn盐电解着色工艺:主要是单Sn盐、Sn-Ni混合电解着色,主要的着色盐是SnSO4,利用Sn2+点解还原在阳极氧化莫的微孔中析出而着色。优点:Sn盐的抗杂质性能好,点解着色溶液分布能力强,工业控制简单,交流Sn盐着色本身不存在困难。缺点:Sn2+稳定性差,着色的色差和色调比较难以控制。
2)Ni盐点解着色工业:与Sn盐电解着色工业相似,析出Ni而着色。优点:Ni盐着色速度快,槽液稳定性好。缺点:对槽液的杂质比较敏感
2.交流与直流电解着色的优缺点。
1)交流着色。优点:克服了直流电解着色存在氧化膜剥落的危险。
缺点:在交流着色中阳极电压会影响阴极着色反应的速度,使得阳极电流密度下降,阴极电流密度减小,从而 着色速度减慢。
2)直流着色。优点:着色速度快,电能利用率高;缺点:直流电解着色存在氧化膜剥落的危险。
第十一章铝阳极氧化膜的染色
1.氧化膜应具有哪些条件才能进行染色处理
(1)铝在硫酸溶液中得到的阳极氧化膜无色而多孔;
(2)氧化膜应具备一定的厚度,应大于7um;
(3)氧化膜应具有一定的松孔和吸附性;
(4)氧化膜层应完整、均匀,不应有划伤、沙眼、点腐蚀等缺陷;
(5)氧化膜本身具有合适的颜色,且没有金相结构的差别,如晶粒大小不一或严重偏析等。
2.简述有机涂料和无机涂料的染色机理。
(1)有机染料的染色基于物质的吸附理论,有物理吸附和化学吸附。
物理吸附:分子或离子以静电力方式的吸附。氧化膜的组成是非晶态的氧化铝,内层靠近铝基体的为致密的阻挡层,上面生长着呈喇叭状向外开张的多孔型结构,呈现出优良的物理吸附性能,当染料分子进入膜孔时,就被吸附在孔壁上。
化学吸附:以化学力方式的吸附。此时有机染料分子与氧化铝发生了化学反应,由于化学结合而存在于膜孔中。这种吸附有以下几种:氧化膜与染料分子上的磺基形成共价键;氧化膜与染料分子上的酚基形成氢键;氧化膜与染料分子生成络合物。
(2)无极染料染色机理:染色时将氧化后的工件按照一定的次序先浸渍在一种无机盐溶液中,再依次浸入另一种无机盐溶液中,使这些无机物在膜孔中发生化学反应生成不溶于水的有色化合物,填塞氧化膜孔隙封住,因而使膜层现颜色。
3.有机染料染色工艺的流程与规范。
工艺流程:前处理-阳极氧化-清洗-氨水中和或其他处理-清洗-染色-清洗-封孔处理-烘干。
工艺规范:1)染色容易的浓度:染浅色调,浓度一般控制在0.1~1g/L,而染深色要求2~5 g/L,染黑色要求10 g/L以上;2)染色溶液的温度:一般控制在50~70℃;3)染色溶液的PH值:PH范围5~6;4)染色时间:通常为5~15min。
4.有机染色工艺中染色液的杂质影响及其控制。
(1)硫酸钠的影响:硫酸钠降低染色速率,这种影响随染料离子中硫磺基团的增加而增加,特别是金属络合物染料。
(2)氯化钠的影响:引起电蚀点(白点)的主要原因。电蚀点被阴极电流所抑制。
(3)表面活性剂的影响:非离子型表面活性剂对染色无影响,但阳离子表面活性剂如加入铝黑MLW中会减慢染色,故除油剂中不适宜添加离子型表面活性剂,因某些阴离子对染色不利。
(4)三价铝离子的影响:少量Al3+ 对许多染液无影响,除非达到500~1000ug/g,此时可能造成变色,如蓝色变成带红等。
(5)重金属离子的影响。
(6)阴离子的影响。
(7)细菌作用对染色的影响:细菌在染液中繁殖,使染液发霉,首先在染液表面起小泡,当染液不工作静置时,在泡的周围聚集一些不溶解的有色颗粒,使染色不正常。假如肉眼可见,应将悬浮于表面的发霉物捞掉,并加入0.05~0.10g/L合适的杀菌剂,如二氯酚G4,用乙醇溶液溶解后加入槽中。有时只有将染液倒掉。此时应用杀菌剂或次氯酸溶液清洗槽壁,然后重新配置。
(8)不溶杂质对染色的影响:染色液中有时不可避免地会带入油污,玷污工件使染色发花,此时应用吸油纸吸沾除去或加入少量非离子表面活性剂,使油滴分散不致聚集在染液表面。
5.列举常用的无机染色工艺及其步骤与参数(至少五种颜色以上)
6.
一般在常温下进行操作,通常分两步进行,现在第一种溶液中浸5~10min,取出清洗后再在第二种溶液中浸5~10min,则染成所需的颜色。
常用无机染色工艺规范
色彩
溶液成分
含量/(g/L)
生成有色盐
蓝色
1亚铁氰化钾[K4Fe(CN)6.3H2O]
2三氯化铁[FeCl3]或者硫酸铁[Fe2(SO4)2]
30~50
40~50
亚铁氰化铁(普鲁士蓝)
黑色
①醋酸钴[CoAc2]
②高锰酸钾[KMnO4]
50~100
15~25
氧化钴
黄色
①醋酸铅[PbAc2.3H2O]
②重铬酸钾[K2Cr2O7]
100~200
50~100
铬酸铅
白色
①醋酸铅[PbAc2.3H2O]
②硫酸钠[Na2SO4]
10~50
10~50
硫酸铅
褐色
①铁氰化钾[K3Fe(CN)6]
②硫酸铜[CuSO4.5H2O]
10~50
10~100
铁青华铜
金色
草酸高铁铵[NH4Fe(C2O4)2](Ph=4.8~5.3,35~50oC,2min)
10(浅)
25(深)
7.染色常见的问题以及解决方法。
1)不上色 。 解决办法:a、调换颜料 b、调整PH c、提高膜层厚度 d、及时染色 e、选用合适颜料。
2)部分着不上色或颜色浅。 解决办法: a、加强保护措施 b、提高颜料浓度 c、提高膜层厚度 d、夹紧工件,调正位置 e、调换着色液 f、改进颜料溶解。
3)染色后表面呈白色水雾状。 解决办法: a、去除水汽 b、调整褪色液浓度 c、缩短褪色时间。
4)染色后发花。 解决办法:a、调整PH 加强清洗 b、改进颜料溶解 c、降低染液温度。
5)染色后有点状。 解决办法: a、用水冲洗试样表面 b、过滤染液 c、氧化后工件放入清水槽 d、加强防护。
6)染色后易褪色。 解决办法: a、调高PH b、提高染色槽温度,延长染色时间,调整封孔槽PH,延长封孔时间。
7)染色表面易擦掉。 解决办法:a、重新氧化 b、提高染色液温度 c、调高氧化温度。
8)染色过暗。 解决办法:a、冲稀染液 b、降低温度 c、缩短时间。
第十二章 铝阳极氧化膜的封孔
1.封孔:铝阳极氧化后对氧化膜进行的化学或物理过程,以降低氧化膜的孔隙率和吸附能力。其封孔原理主要有(1)水合反应 ;(2)无机物充填;(3)有机物充填。
2.热封孔技术是通过氧化铝的水合反应,将非晶态氧化铝转化为称为勃姆体的水合氧化铝,即Al2O3•H2O(AlOOH)。 热封孔的机理本质是水合反应,常称为“水合-热封孔”。
3.水合反应的作用:体积膨胀了30%,体积增大使氧化膜的微孔得到填充和封闭,抗污染性和耐腐蚀性随之提高,同时导纳降低(阻抗增加),介电常数变大
4.水中杂质的的影响:1)封孔的效果很大程度上取决于水的质量和PH控制;
2)常见的杂质:SiO2、H2SiO3;3)措施:离子交换 。
5.沸水封孔参数和冷封孔参数比较
1)沸水封孔的温度:一般95度以上。冷封孔为室温;2)沸水封孔的PH值:最佳范围5.5~6.5。冷封孔范围5.5~6.5,工业控制以6为最佳。3)沸水封孔的时间:取决于膜厚、孔径大小和封孔品质试验要求。冷封孔一般规定为10~15min。
第十八章
1.简述常用的阳极氧化膜质量检测方法及其优点
1)外观和色差 检测方法:目视和仪器检测法 优缺点:目视法简单,但易受试样的形状和大小,照光的强弱等因素的影响 仪器法解决了目视法的缺点,适用于测定反射光的颜色。
2)氧化膜的厚度 测量方法:a、横断面厚度显微镜测量法:膜厚大于5um, 垂直 b、分光束显微镜测量法:膜厚大于5um,氧化膜折射率1.59~1.62 c、质量损失法:膜厚小于5um,溶解法,表面密度,氧化膜密度(硫酸液氧化)封闭前后为2.6和2.4g\cm3 d、涡流法:不适用于薄的膜
3)封孔质量:a、指印试验 b、酸处理后染色斑点质量,不适用于cu高于2%和si高于4%的含量 c、磷铬酸实验
4)耐蚀性:a、盐雾腐蚀试验 b、含SO2潮湿大气腐蚀试验 c、马丘腐蚀试验 d、耐湿热腐蚀试验 e、滴碱腐蚀试验
5)耐化学稳定性:a、耐酸实验 b、耐碱实验 c、耐砂浆试验
6)耐候性:a、自然暴露实验 b、人工加速耐候实验
7)硬度:a、压痕硬度 b、铅笔硬度 c、显微硬度
8)耐磨性:a、喷磨试验仪检测耐磨性 b、轮式磨损试验仪检测耐磨性 c、落砂试验仪检测耐磨性
9)附着性:a、划格实验 b、仪器实验:划痕法
10)力学性能:a、耐冲击性 b、抗弯曲性 c、疲劳性能 d、结合强度 e、抗变形破裂 f、抗热裂性
11)电绝缘性:击穿电位法
12)反光性能
13)其他:a、涂层聚合作用性能 b、耐沸水性 c、加工性能
2.耐磨性影响因素:合金成分、膜厚、高聚合物涂料的固化条件、阳极氧化条件和封孔条件等
还有剩余内容未读
@ SKYIIII

声明:说化有益·表面处理联盟网资料文库文档均为用户分享上传,版权归上传者所有。文档内容是行业专业性知识,知识的严谨度及实用性极强,因此部分价值极高的文章需要付费查看,用户可根据实际需求进行已付费文档下载;付费记录可在“用户中心”-“我的订单”-“我的文库”内查看。由于知识产权的特殊性,付费成功后不支持退换,用户应根据自身需求判断是否需要继续操作。
我们欢迎各方(自)媒体、机构转载、引用我们原创内容,但需严格注明来源。同时,我们也倡导尊重与保护知识产权,如发现文章内容涉及侵权,请通过在线咨询进行投诉,我们会在第一时间核实处理。