传统磷化处理和硅烷处理之间的区别与优缺点
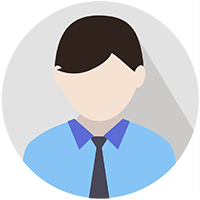
2022-06-15 16:42

+1
取消

+1
取消

微信扫一扫分享给朋友
硅烷化处理与传统磷化相比具有以下多个优点:无有害重金属离子,不含磷,无需加温。硅烷处理过程不产生沉渣,处理时间短,控制简便。处理步骤少,可省去表调工序,槽液可重复使用。有效提高油漆对基材的附着力。但就目前的国内技术来说,不是十分成熟,有待提高!尤其是硅烷助剂的选择上,需要继续研发创新。
图片来自于网络
项目 | 磷化处理 | 硅烷处理 | |
工艺原理 | 磷化处理就是金属表面与磷化液接触发 生化学反应,在金属表面生成稳定的不 溶性的无机化合物膜层的化学处理方 法,所生成的膜被称为磷化膜。磷化膜 的作用是在充分脱脂的基础上能提供清 洁、均一、无油的表面。 | 硅烷化处理是以有机硅烷为主要原料对 金属或非金属材料进行表面处理的过 程。是利用氟锆酸与硅烷的水解反应, 在金属表面形成一种由氧化锆 ZrO2 和氧 化硅 SiO2 组成的三维网状化合物,该化 合物在被处理的金属表面起到耐腐蚀并 增加附着力的作用。 | |
工艺流程 | 脱脂-水洗-新水洗-表调-磷化-水洗-水 洗-纯水洗:8 道工序 | 脱脂-水洗-新水洗-硅烷-水洗-水洗-纯 水洗:7 道工序 | |
硅烷工艺无需表面调整。 表面调整的目的是促使磷化,形成晶粒细致、密实的磷化膜,以及提高磷化速度。 表面调整剂主要有两类,一种是酸性表调剂,如草酸,另 一种是胶体钛。前者还兼 有除轻锈 (工件运行过程中形成的“水锈”及“风锈”)的作用。 在磷化前处理工艺中,是否选用表面调整工序和选用哪一种表调剂都是由工艺与磷 化膜的要求决定的。一般原则是:涂装前打底磷化、快速低温磷化需要表调。如果 工件在进入磷化槽时已经二 次生锈,最好采用酸性表调。 | |||
工艺技术 | 工艺流程需要表面调整; 含磷及锌镍锰铬等重金属; 污染物大; 耗能高(35℃-55℃); 处理时间长(120s-180s); 沉渣多 | 工艺流程无需表面调整; 无磷及锌镍锰铬等重金属; 污染物排放量较少; 无需加热(室温); 处理时间较短(60s-120s); 几乎无渣 | |
皮膜 | 皮膜构造:磷酸锌结晶; 皮膜厚:2-3g/m²; 耐酸碱性:溶解。 | 皮膜构造:非晶态混合薄膜; 皮膜厚:0.2-0.4g/m²; 耐酸性:氢氟酸 HF 以外全不溶解; 耐碱性:不溶解。 | |
沉渣 | 磷化反应机理大致分为酸蚀反应和磷化 反应。磷化反应是金属表面与磷化液中 的磷酸盐反应,最终以磷酸锌的形式在 被处理物表面结晶,形成保护膜的化学 过程。在整个反应过程中,由于溶解下 来的金属离子被氧化,所以会产生大量 沉淀。沉淀的产生是伴随磷化反应过程 同步生成的,无法消除。 | 几乎无渣 |
1、环保性
硅烷产品和磷化相比,不含锌、镍、锰等重金属,显著减少水耗量,显著减少废水处理量;室温工作,不含磷,不含氧化还原剂,无氮氧化物废气排放,几乎无渣(所有金属出渣量<0.1g/m2),由于出渣量低,可完全闭路水处理,循环用水,不产生废水。
2、管理的便捷
磷化工艺的副产品是大量的磷化渣,每隔一段时间,生产线必须停产,对磷化槽进行除渣处理,除渣结束后不仅要清洗磷化槽,磷化液也不可避免有部分浪费。磷化渣的处理也是件费力的事情。而使用硅烷产品,以上的一切问题都不再存在了。磷化过程中需要控制游离酸、总酸、氟硅酸、促进剂点等各参数,而硅烷只需控制PH和活化点。硅烷过程还无需表调槽,从而节约了表调槽的化学品消耗和控制,操作更简单。
声明:说化有益·表面处理联盟网专业视角栏目旨在免费为同行提供知识共享和储存,所有文章均由业内专业人士发布(包括转帖),文末都会标注作者,版权归作者所有。文章仅代表作者本人的观点,本站不保证文章等内容的有效性。
知识互通,携手共进,我们欢迎各方(自)媒体,机构转载,引用我们原创内容,但需严格注明来源。同时,我们也倡导尊重与保护知识产权,如发现文章内容涉及侵权,请通过在线咨询进行投诉,我们会在第一时间核实处理。
相关视角