相关文档推荐
-
11.0分 | 7718阅读 | 4人下载
-
21.0分 | 4590阅读 | 1人下载
-
32.4分 | 7002阅读 | 8人下载
-
42.5分 | 8702阅读 | 10人下载
-
51.0分 | 7796阅读 | 3人下载
-
60.1分 | 7634阅读 | 0人下载
-
71.4分 | 5955阅读 | 8人下载
-
81.2分 | 5564阅读 | 8人下载
-
91.2分 | 4962阅读 | 4人下载
-
101.5分 | 4705阅读 | 11人下载
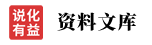
免费下载


点赞 1

收藏 1

分享
微信扫一扫分享给朋友
化学镀镍的配方与实操使用实例
1 铸铁复合化学镀镍前的活化工艺
铸铁复合化学镀镍前处理工艺为:机械抛光→除油除锈→活化处理。但不同的活化方法,直接影响镀层的结合力和孔隙率。筛选最佳阴极活化工艺为:70%H2SO4,室温(最佳200OC),DK=8A/dm2,10s。本活化液可保证镀层结合力最大、孔隙率均为零。
2、如何改善不锈钢化学镀镍层的结合力
不锈钢件(传动轴、啮合件、动配合件等)化学镀镍,可改善镀层的均匀性和自润滑性,比电镀铬好。但不锈钢化学镀镍常因前处理不好而造成镀层与基体结合力不理想,成为实际生产中迫切需要解决的问题。
原工艺流程:机械抛光→有机溶剂除油→化学除油→热水洗→电化学除油→热水洗→冷水洗→30%HCl→冷水洗→20%HCl(50OC)→冷水洗→闪镀镍→化学镀镍。
原工艺的缺点:单独用HCL除氧化皮效果不好;形状复杂件闪镀镍因覆盖能力不好而影响到化学镀镍的均匀性;因工序较长有可能造成不锈钢新鲜表面重新被氧化成膜;闪镀镍溶液易污染化学镀镍溶液等。为此,有人改进工艺。
改进工艺流程:抛光、除油工序同原工艺→混酸除膜(25%HCl+8%HNO3+10%HF)→冷水洗→活化(10%HCl+5%NH4F,60OC)→热水洗→化学镀镍。
改进工艺的优点:①采用混酸除去不锈钢表面难溶的FeCrO4氧化膜、Si、SiO2,使基体表面的化学活性增强;②工序简化,避免了不锈钢新鲜表面重新被氧化;③增加基体的预热工序,消除镀层与基体因温差而产生的应力。因此,化学镀镍与基体结合力好,镀速快等。3 如何进行减压化学镀镍
减压化学镀镍,用镀液的动态载荷取代静态载荷,大大扩展了化学镀镍的应用范围,镀层光亮平整、针孔隙低、耐蚀性好。本法适用小口径长管内壁化学镀镍(φ内≥4cm以上各种细其整平性)。解决办法:系列压力差(P0—P1)控制在(-5.3×-66.7)×103Pa内,管径细,适当减少压差,降低镀液流速;管径粗,可适当增加压差,提高镀液流速。本工艺系统负压不高,操作安全简便。
4 喷淋化学镀镍工艺
采用喷淋可解决大型工件局部化学镀镍的困难,是实行现场施镀的有效方法,既经济又省时。
列举牵引轮(直径2050mm,轮面宽70mm,轮壁厚25mm,自重约2t)过线的外圆面喷淋化学镀镍工艺过程:除锈抛光(手动砂轮)→磨光(砂纸)→除油(表面活性剂)→带压热水冲洗→带压冷水冲洗→双面喷淋酸浸蚀→带压双向水冲洗→双向喷淋弱浸蚀→甩干轮面浮酸→双面喷淋化学镀镍。
注意问题:①在浸蚀、水洗、甩干浮酸时要提高牵引轮转速;②弱浸蚀用CP级盐酸,并加热至65OC,为牵引轮预热;③为消除弱浸蚀过程轮面上滞留酸的影响,开始喷淋化学镀镍的pH值取上限值(pH=10.0),喷淋过程中牵引轮转速不低于10r/min。
5 钢铁化学镀镍的防护作用
(1)提高海洋结构件的抗腐蚀疲劳寿命
试验表明:海洋结构件化学镀镍可提高抗腐蚀疲劳寿命1.5~2.5倍,且镀层具有相当塑性,与基体结合力牢固。
(2)提高磨损件的使用寿命
如纺机件“钢令”及气压件填料盒化学镀镍后,前者上机台运行半年,表面未出现沟槽仍能正常使用,可操作性良好(无走速期,纺纱光滑而羽毛很短,也不易断头)。克服了渗碳钢“钢令”走速期长,耐磨性差(运行三个月需抛光才能用),可操作性差(纺纱断头频繁、纺纱羽毛长、表面粗糙不光滑)等缺点。后者运行二年后,无腐蚀、磨损,镀层仍然完好,保持原有光泽,优于不锈钢填料盒(不锈钢填料盒运行二年后表面发生蚀点),节省填料盒的材料及机加费用。
(3)提高风机叶轮的防护性
如磷肥厂的风机叶轮原使用橡胶或玻璃钢衬层防腐,因磷酸尾气中含有氟化氢等强酸性气体,且使用温度高,使用寿命仅有4个月左右(发生脱层和脆性破裂现象)。改为化学镀镍后使用寿命延至两年左右,保证了生产的安全运行,又节约了4%的资金。
(4)提高大型设备整体抗恶劣环境和工作条件的能力。
如烯烃厂的EA-123换热器(面积达3000m2),因恶劣环境和工作条件,成为抗腐蚀能力差的老大难问题。经整体一次性化学镀镍(表面均匀无斑点、裂纹、结瘤,无边解效应,结合力强等),运行二年后,清除表面油污后仍可见明显的镀层光泽,镀层保持完好。这在国内尚属首例。又如炼油厂的冷换设备化学镀镍取代了有机涂料的防腐,使用寿命显著提高,确保了系统的长期安稳运行。尤其在低碳钢的管束上化学镀镍后,在H2S、HCl-H2S-H2O、常顶油气、硫磺尾气等介质中抗腐蚀性能优良,还能延缓冷却水的结垢速度。
大型设备化学镀镍工艺流程:喷砂除锈→冷水冲洗→酸洗活化→冷水冲洗→化学镀镍(作防腐层厚度25-50μm)→冷水冲洗→钝化→冷水冲洗。
由于化学镀镍的优异防腐蚀性,可获得可观的经济效益。据介绍,换热器管速(长6m,直径1m)化学镀镍获得直接经济效益109.6万元,间接经济效益更为可观。
化学镀镍配方:NiSO4·6H2O 23g/L,NaH2PO2·H2O 20g/L,CH3COONa·3H2O 14g/L,Na3C5H6O72H2O 6g/L,pH=4.0~5.0,温度74~84OC,沉积速度约20μm/h,镀层磷含量8.5%~12.5%。
6 模具化学镀镍的几个问题
为了提高模具加工件的质量,改善加工件的脱模性,延长模具使用寿命,模具必须镀覆硬铬或化学镍层,但它们各有利弊,如硬铬层的硬度高、摩擦系数小、脱模性好等,但耐蚀性较差;化学镀镍操作方便,耐蚀性好,而其他镀层性能却较硬铬层差。所以,模具单一镀硬铬或化学镀镍使用寿命都短(仅2周左右),无法满足工业要求。最好选择复合镀层。
(1)化学镀镍套硬铬工艺
施镀工艺流程1#:化学镀镍→热处理→阴极活化处理→镀硬铬
热处理条件:(95±10℃,3~5h;阴极活化:H2SO4 250~350g/L,含氟添加剂 15~25g/L,DK=2~5A/dm2。
化学镀镍配方:NiSO4·6H2O 21g/L,NaH2PO2·H2O 24g/L,C3H6O3 27ml/L,C3H6O2 2ml/L,NaC3H5O2 15g/L,pH=4.6~4.82,温度88±2OC。
本工艺流程适宜于普通模具镀覆,使用寿命高。
施镀工艺流程2#:闪镀镍→后继工序同流程1#。
本工艺流程适宜PUC塑料模具镀覆,镀层结合力非常好,使用寿命高。若取消闪镀镍,化学镀镍层与基体(合金钢)结合力仍较差,铬层和镍层一起从基体上起皮。
(2)成套模具选择不同的单一镀层组合使用
施镀工艺流程1#除油→水洗→酸洗→活化→水洗→化学镀镍→热处理(400℃,1h)。
本工艺流程适用于玻璃钢窗成套模具之一的有沟槽模具化学镀镍,由于镍层均匀一致(沟槽处皆为38~40μm镀层厚度),克服了镀硬铬因尖角效应而导致钩槽处无镀层的缺陷,保证了玻璃钢窗框的拉制。有沟槽模具系A3钢制成,抛光后表面粗糙度为Ra0.1~0.2,镀镍层光亮如镜。
化学镀镍配方:NiSO4·6H2O 20~30g/L,NaH2PO2·H2O 30~40g/L,NaAC20g/L,柠檬酸5~7g/L,丁二酸9~10g/L,十二烷基硫酸钠0.01~0.02g/L,硫脲0.002g/L;pH=4.5~4.8,温度(88~90)±3OC,2h,装载量1dm2/L,镀速17μm/h。
施镀工艺流程2#:前处理工序同流程1#→镀硬铬。
本工艺流程适宜玻璃钢窗成套模具之一的无沟槽模具镀硬铬,可降低生产成本(低于化学镀镍),硬度高(1100HV0.1)。
(3)控制化学镀镍质量的因素
①控制镍层磷含量。镍层磷含量升高,硬度降低,呈现出压应力;反之,磷含量降低,引起拉应力(可达15~45MPa),表面产生孔隙和 裂纹。所以,化学镀镍磷含量控制在7%~11%。②掌握热处理条件。化学镀镍层经热处理可提高显微硬度、耐磨性及耐热性能;消除镀层的脆性,降低镀层的内应力;大大改善镀层与基体的结合力。但热处理条件视模具对耐蚀性的要求不同而异。如注射模、挤压模热处理温度190~210OC,保温3h。若温度高于260OC时,开始形成弥散的Ni3P质点,使体积收缩达40%~50%,呈现出拉应力状态,使镀层产生微裂纹,以致于基体金属裸露出来。但是,精密模具的工作温度会高达600℃左右,故处理温度600OC为佳。
7 铝合金化学镀镍前的预处理新工艺
铝合金化学镀镍前采用二次浸锌最普通,但浸锌存大的缺陷:①锌层易溶解于酸性化学镀镍溶液中;②由于基体与镍层之间夹杂锌层,在腐蚀介质中形成电偶腐蚀(Al-Zn-Ni),将导致镀层鼓泡或脱落,降低耐蚀性;③经浸锌后化学镀镍,不宜进行400oC热处理,会造成浸锌层空松。同时铝和镍膨胀系数相差悬殊,在高温时会引起足够的应力,使镀层与铝之间产生破裂。而以活化代替浸锌,为化学镀镍提供了一个较好的底层,镀层与在材有结合力能达到同浸锌一样好的结果,是一种很有用途的铝合金前处理新工艺。
活化处理液为:NiSO4。6H2024~30g/L,HEDP 40~50g/L,稳定剂N25~30ml/L,Ph(NaOH调整)>12,室温,1~4min。控制活化时间至关重要,对某一具体配方,可通过实验杰确定最佳浸清时间,即当表面完全呈均匀灰色时,进行化学镀镍可得到最佳镀层质量。
8 如何保证电子微组铝件化学镀镍的质量
微组铝件(放大器铝腔体、微波开关、振荡器和天线蚀电架等)化学镀镍取代铝镀银工艺必须保证外观装饰性、优异附着力、耐腐蚀性和理想的物理、化学特性(电磁屏蔽、焊接性、高硬度、耐磨、高低温等)。关键在于优化工艺配方和镀层组合。
典型工艺流程:有机溶剂支油(LYC2被镀铝件)→碱性除油(或碱腐蚀) →硝酸浸蚀→二次浸锌→碱性化学镀镍→酸性化学镀镍→热处理
(1)改良特殊预处理工艺
选择了含镍盐和辅助络合剂的改良锌酸盐酸方,碱浓度适中,特别是含有镍盐,并将酒石酸钾钠含量升高,又增加添加剂,使镍离子呈较稳定络离子开式存在,从而使镍离子与锌离子一起缓慢而均匀地置换沉积在铝表面,得到的锌镍合金层比从传统浸锌液中获得的浸锌层更薄更均匀。且控制Zn-Ni层重量在1~2mg/dm2范围,能充分保证铝上镀层附着力和抗蚀性良好;特别是含镍的锌层为随后的化学镀镍沉积初期提供了充足的催化核心,得到均匀细小晶核,这是提高随后镀镍层附着力的一上重要因素。
改良锌酸盐配方:NaOH 240g/L,ZnSO4 120g/L,NiSO4 60g/L,KnaC4H4O6 120g/L,添加剂10~30g/L,室温,2~3min。
(2)改善预镀底层
由于锌层不耐性液腐蚀,必须预镀碱性化学镀镍作底层。但碱性镀镍液存在沉积速度较慢(5~10m),含P量较低(4%~6%),抗蚀性较差等缺点。要求改变还剂和络合剂浓度,选择最佳期PH值范围,保证镀液稳定,镀速适中,并能在浸锌层表面得到一层结晶细小、均匀与基体结合良好的预镀薄镍层。
改进碱性镀镍配方:NiSO4。6H2O 25g/L,NaH2PO。H2O 25g/L,Na3C6H5O7 45g/L NH4Cl 30g/L,35~45Oc,Ph=8~9
(3)提高镀层的防护性与装饰性
优选酸性化学镀镍配方,含有少量学亮剂,镍离子与次亚磷酸根子的摩尔浓度比值控制在0.4左右,保证镀速适中(16~20m/h),溶液稳定(6周期以上,即使煮沸镀液也不会分解)。此外加入复合络合剂,防止生成亚磷酸镍沉淀。从本久液中可镀出呈学亮黄白色的镍层(含磷量8%~10%),耐蚀性好(镍层厚度25μm经中性盐雾试验48h,耐蚀等级9.5)。建议在海上或恶劣环境使用的工件化学镀镍厚度设计为≥25μm。
优良酸性化学镀镍溶液:NiSO4。6H2O 27g/L,NaH2PO2H2O 29g/L,C2H5Ona 25g/L,Na3C6H3O7 25g/L,络合剂适量,学亮剂少量,pH=5,85~90oC,装截量0.5~1.5dm2/L。日常生产根据分析结果加镍盐、还原剂。
(4)适当的后处理
铝合金化学镀镍后进行热处理(150~200oC,3h),可以消除层中残留的H原子,松驰内应力,进一步提高镀层与基体附着力和硬度。
9 铸铝轮毂化学镀镍的工艺过程
铸铝轮毂化学镀镍能提高其使用性能和装饰性能,具有硬度高、耐磨、耐腐蚀、外型复制好等特点。铸铝合金(AlSi7MgO3)化学镀镍工艺流程:手工除油(洗衣粉溶液)→化学除油→化学浸蚀→二次浸锌→碱性化学镀镍→酸性化学镀镍→烘干
主要工序如下:
⑴化学浸蚀:
除去轮毂表面的铝氧化膜及Si、Mg等元素,以保证表面呈均匀的富铝状态;同时起到抛学作用。化学浸蚀溶液:HNO3 60-70ml/L,HF15-20ml/L,甘油ml/L,室温,0.25-0.5min。
⑵浸锌
经二次浸锌,锌层更均匀、细致,与基体结合力更好。浸锌溶液:NaOH 525g/L,ZnO 100g/L,FeCl3。6H2O1g/L,酒石酸钾钠12g/L,室温,一次浸锌0.5min,二次浸锌15~20s。浸锌后工件清洗一定要充分。
⑶碱性化学镀镍
NiSO4。6H2O 30g/L,NaH2PO2。H2O 30 G/L,Na3C6H5O7。2H2O 10~15g/L,三乙醇胺50g/L,pH=8.5~9.5,30~35Oc,3~5min。
⑷酸性化学镀镍
NiSO4。6H2O 30g/L,NaH2PO2。H2O 30g/L,乳酸ml/L,络合剂Ⅱ(丁二酸、丙二酸等)10g/L,缓蚀剂(乙酸、丙酸、钾盐、钠盐等)10g/L,加速剂(脂肪酸、NaF等)2g/L,稳定剂(pb2+、MoO2-4),Ph=4.6~5.4,88+-2oC,装载量1dm2/L。
本配方使用二种络合剂,可形成由两种络合剂同时与镍离子络合的混合物,既可提高镀速,又能增加镀液的稳定性,有效抑制亚磷镍的沉淀。
10 铝合金电子机壳化学镀镍的优越性
电子机壳化学镀镍综合性能好。提高了装饰性(银白色、柔和、美观)、防护性(防护性是电镀Ni层的二倍)、导电性(电阴率51~60μΩ。Cm,导电、电磁屏蔽效果好)、散热惦、润滑性(P有一定的自润滑作用)、精密性(厚度均匀、可控,盲孔处的镀层完好)、钎焊性、可修复必(Ni层再镀性好)等。大幅度提高了整体涂覆的质量,满足了军事电子系统工程的设计和使用要求,既保证了高可靠性,又改善了机壳的接地和互联效果。总的来说,电子机壳化学解放区昝最佳涂覆。
11 解决铝质槽筒化学镀镍层易擦灰的方法
为了增络纱机上铝质槽筒表面的耐磨性,一般采用化学镀镍工艺。但在使用过程中纱与槽筒表面的镍层磨擦后,白纱表面附着一层黑灰,影响产品质量。为了解决其表面擦灰问题,采用镀后热处理。由于P和Ni会转变为Ni3P并高度弥散析出(镀层结构部分或全部转变为晶态结构,增加了镀层塑性变形时势滑动阻力,使镀层强化,使其耐磨性和硬度均大大提高。但热处理条件的正确与否,直接影响到工件的变形及镀层的耐蚀性。因铝件槽筒在高温热处理后易变形,况且久层的耐蚀性随着热处理温度升高而降低(镀层结构变为混合相,结构高度不均匀,形成电位差,混合相间就易形成腐蚀微电池)。因此,最佳热处理温度不超不定280oC,保温3h。
12 何保证铝基剪杆化学镀镍套铬的质量?
铝基剪杆化学镀镍套硬络,既具有很高的耐磨性和耐腐蚀性,又有较好的抗冲击性能,避免了高硬度的铬层与较软的铝基体直接接触而可能引起的开裂、凹陷。施镀工艺流程:除油→二次浸锌→化学镀镍→活化→硬铬→除氢。为保证化学镀镍套铬的质量,关键工艺在于:
(1)化学镀镍层的结合力受浸锌液成分影响较大。较佳的浸锌液:
①NaOH 180~200g/L,ZnO 18~30g/L,NaC4H4O6。H2O 50g/L,NaNO2 1~2g/L,25~35Oc,40~45S;②NaOH 100g/L,ZnO 30g/L,KnaC4H4O6。6H2O 10g/L,FeCl3 2g/L,NaNO3 1g/L,室温,30~60s。
(2)保证化学镀镍层无孔隙
由于镀铬溶液的腐蚀性和高电流冲击。很容易把镍层剥落。所以镍层必须无孔隙。当镍层达到15μm时,已测不出孔隙。
(3) 有合理的镀硬铬工艺
试验表明,传统的镀铬液均不满意(镍层肃离或铬层起皮),唯有稀土镀铬液可施镀厚镍 层(20μm)上套厚铬(5·10·15μm铬层)。稀土镀铬液:铬酸130-150g/L,硫酸0.5~0.8 g/L,稀土添加剂1.5~2.0 g/L, Cr3+1~2 g/L ,50~55℃,DK40~45A/dm2,镀速40μm/h。
(4)化学镀镍层与硬铬层必须有合适的厚度比
当硬铬层要求20μm时,化学镀镍层>25μm,双层镀层结合力优良。这是因为硬铬层有很大的内应力(表现为拉应力),随镀层度增加而迅速增大,当应力大于镍层与基体的结合力时,就可以把镍层剥落,所以,只有化学元素镀镍层达到相应的厚度,才能使镍层的结合力大于硬铬层的拉应力。且镀后进行除氢处理品,消除铬层部分内应力。
本工艺用于剪杆大批量生产并出口,质量达到国外水平。
13 化学镀镍的常见故障及解决办法
(1)沉速低
镀液pH值过低:测pH值调整,并控制pH在下限值。虽然pH值较高能提高沉速,但会影响镀液稳定性。
镀液温度过低:要求温度达到规范时下槽进行施镀。新开缸第一批工件下槽时,温度应达到上限,反应开始后,正常施镀时,温度在下限为好。
溶液主成分浓度低:分析调整,如还原剂不足时,添加还原补充液;镍离子浓度偏低时,添加镍盐补充液。对于上规模的化学镀镍,设自动分析、补给装置是必要的,可以延长连续工作时间(由30h延至56h)和镍循环周期(由6周延至11周)。
亚磷酸根过多:弃掉部分镀液。
装载量太低:增加受镀面积至1dm2/L。
稳定剂浓度偏重:倾倒部分,少量多次加浓缩液。
(2)镀液分解(镀液呈翻腾状,出现镍粉)
温度过高或局部过热:搅拌下加入温去离子水。
次亚磷酸钠大多:冲稀补加其它成分。
镀液的pH值过高:调整pH值至规范值。
机械杂质:过滤除去。
装载量过高:降至1dm2/L
槽壁或设备上有沉淀物:滤出镀液,退镀清洗(用3%HNO3溶液)。
操作温度下补加液料大多:搅拌下少量多次添加。
稳定剂带出损失:添加少量稳定剂。
催化物质带入镀液:加强镀前清洗。
镀层剥离碎片:过滤镀液。
(3)镀层结合力差或起泡
镀前处理不良:提高工作表面的质量,加工完成后应清除工件上所有的焊接飞溅物和焊渣。工件表面的粗糙度应达到与精饰要求相当的粗糙义,如碳钢工件表面粗糙度Ra<1.75μm时,很难获得有良好附着力的镀层;对于严重锈蚀的非加工表面,可用角向磨光机打磨,最好采用喷砂或喷丸处理;工件镀前适当的活化处理可以提高镀层的附着力。如合金钢、钛合金可用含氟化物的盐酸活化后,与碳钢件混装施镀;高级合金钢和铅基合金预镀化学镍;碳钢活化时注意脱碳。
温度波动太大:控制温度在较小的范围波动。
下槽温度太低:适当提高下槽温度。
清洗不良:改进清洗工序。
金属离子污染:用大面积废件镀而除去。
有机杂质污染:活化炭1-2g/L 处理。
热处理不当:调整热处理时间和温度。
(4)镀层粗糙
镀液浓度过高:适当冲稀镀液。
镀液的pH值过高:降低pH值至规范值。
机械杂质:过滤除去。
亚磷酸盐过高:弃掉部分镀液。
加药方法不对:不可直接加固体药品或用镀液溶解药品。
清洗不够 ,带入污染:加强清洗。
络合剂浓度偏低:补充络合剂。
工艺用水污染:使用去离子水或蒸馏水。
(5)镀层不完整(漏镀)
前处理不当、镀件局部钝化或油污、清洗水不干净等:加强前处理,更换清洗水。
装挂不对有气袋:改进装挂方法、抖动工件、变换位置等。
十二烷基硫酸钠污染:活性炭吸附。
金属离子污染:除去(见上述),过滤。
底金属影响:镀前闪镀镍。
稳定剂过量:弃去部分镀液。
(6)镀层针孔(通常镀层厚度达10μm以上是无孔)
工件前处理不当和酸洗后停留时间过长:提高工件表面加工质量,酸洗后应在30s内进入镀液。
pH值过高:降低pH值。
镀液组份变质和老化:报废镀液。
悬浮不溶物:过滤除去。
装载量过大:减至1dm2/ L,降低pH值。
金属离子污染:除去。对于含pb、cd、Zn、Sn等元素的基材,在施镀镍前,最好电镀1~5μm的镍打底,以阻止有害元素进入镀液。
搅拌不充分:摆动工作。
有机杂质污染:活性炭处理。
(7)镀液不沉积镍
稳定剂浓度过高:弃去部分镀镍。
表面未活化:改进镀前处理工艺。
表面非催化:镀前表面催化处理
镀液pH值、温度过低:调整之。
金属离子污染:加1~2g/L活性炭过滤,通电处理。
(8)pH值变化快
前处理溶液带入:改进清洗工序。
装载量太大:减少受镀面积。
pH值出范围:调pH至最佳范围。
(9)镍离子消耗过快
槽壁和设备镀上镍:处理方法同(2)--⑥
载量太大:减少装载量。
液分解:滤去镀液分析调整或报废。
补充硫酸镍不及时:补加主盐。
(10)镀层光亮度下降、发黑或不均匀
镀液过度浓缩(水份蒸发超过30%):补水
镀液老化(使用寿命达6周期):报废旧液。
络合剂用错或络合剂、稳定剂变质:无法恢复镀液性能时只能将镀液报废。
施镀条件不当,如pH值或温度过高,溶液搅拌和工件阴极移动不良等:调低pH值至规定值的下限,当镀液寿命超过2周期时,pH值控制在4.2为好。但pH=3.5---4.0之间也能得到光亮的镀层;良好的镀液搅拌系统工程和工件移动以及低温施镀都有利于提高镀层光亮度。并控制镀液流速<0.3m/s,避免造成漏镀。
有机杂质污染:处理方法同(3)---⑥。
前处理不充分:加强前处理。
(11)镀层有麻点
工件表面光洁度较低:尽量提高工件的表面质量。
在施镀时调整pH值:施镀时不调pH值。
镀液不稳定和镀液中悬浮颗粒较多:加强过滤,补充一定的稳定剂。
工件摆放位置不当:工件较重要的表面朝下或竖直成90o,并将工件预热到70oC以上施镀,可改善工件向上的光洁度。
(12)镀层厚度不均匀(可以看到镀液中气泡的析出量较正常情况下要多)
由于工件几何形状影响工件表面上的氢气逸出不易,有妨碍氢气顺利排出的部位可能造成镀层较薄:最好采用滚镀法。对于较大的工件也应尽可能性在施镀过程中移动、镀液搅拌、降温等,以利于氢气的排出,提高镀层厚度的均匀性。
工件材质不同:不同材料的化学镀镍速度是不同的,所以不同材质的工件一起施镀时,必须分别测量不同材质工件的镀层厚度。
(13)镀层表面化有大量"花斑",局部有暗色条纹或斑块状沉积物(用10倍放大镜观察)
前处理清洗不良,工件表面粘附了某些杂质:更换洗净剂,镀层恢复了均匀的光亮表面。
(14)镀液中毒(工件上的析氢量较正常情况下多,且沉积速度很慢)
稳定剂过量:通电处理。(工件作阴极,不锈钢件阳极,Dk=0.6~1.0A/dm2,电解1~5min;将镀液置于80oC保温24h;如镀液还不行,最好将镀液储存起来,分批与新镀液混合使用。
缓蚀剂污染镀液:酸洗液中缓蚀剂的加入要慎重,要防止微量缓蚀剂带入镀槽中。
(15)镀槽不沉积镀层
镀液中产生一些固体颗粒:将镀液打入备用槽,再用30%(wt)HNO3在40OC下清洗(不能冷洗),钝化镀槽5h,然后用水洗净硝酸,再用干净棉纱擦洗镀槽上附着物。用清水清洗干净。
镀槽的防镀效果不好:为了防止镀槽上沉积镀层,必须采取相应的防镀方法。据称,采用阳极保护法时,以工件作为阴极和参比电极效果 好。在75~85OC的镀液中维持不锈钢镀槽相对施镀的工件的参比电位为+350~550mv时,镀槽有良好的钝化性能。此时的阳极电流密度为20~90mA/m2。当机械杂质进入镀槽或镀槽上有镀层产生时,其维钝电流将有所上升,但很快将下降至正常水平。这样防镀效果好,并且可以提高镀速10%~20%,而且对镀层质量无显著影响。
加热管功率与其表面积之比不当:同样功率的加热管,应作得尽量长一些,管子粗一些,缩小加热管,应作得尽量长一些,管子粗一些,缩小加热管功率与其表面积之比。
施镀设备及挂具用硝酸清洗不够:每次开缸前用硝酸浸泡镀槽、加热管、挂具、滚筒等,即使没有发现镍镀层也应这样做。
(16)镀液混浊
主盐、还原剂浓度超过上限:调整溶液。
络合剂浓度低:补充络合剂。
pH值过高:降低镀液pH值。
14 锌合多铸件如何化学镀镍
锌合金压铸件化学镀镍可提高其表面硬度,改善耐磨性能,拓宽使用范围。由于锌的两性行为,必须进行特殊处理,选择下列工艺:
(1)确定合理的工艺流程
二种典型工艺流程:①弱碱除油→弱腐蚀(1%H2SO4)→活化(焦磷酸盐)→预镀中性镍→化学镀镍→热处理;②水喷蚀(1%~20%H2SO4,10~15s)→预镀中性镍→预热→(柠檬酸1~2g/L,80~90℃,1min)→化学镀镍→热处理。
(2)预镀中性镍
中性镍配方1#:硫酸镍160~180g/L,柠檬酸钠192~216g/L,氯化钠10~16g/L,硼酸25~30g/L;pH=7,DK=4A/dm2,45℃,≥20min。配方2#:硫酸镍100~180g/L,柠檬酸钠130~200g/L,氯化钠15~20g/L,硼酸30~40g/L,添加剂A 3ml/L;pH=7~7.5,DK=1~1.5A/dm2,冲击电流2~4A/dm2,冲击时间5~7min,50~60℃,20~25min,阴极移动20~30次/min。
预镀中性镍应注意:①采用以硫酸镍为主盐的预镀液,接近化学镀镍的成份。pH值应控制在7~7.5左右。②保证底层有足够厚度,改善底层的质量。如配方2#中加入添加剂A,能提高底层与基体结合力,外观变得光滑细致,产品成品率达95%以上。③妥善处理溶液中产生的Ni(OH)2沉淀,恢复镀液的施镀能力。如用虹吸的办法将镀液中下部的沉淀与上部清液分开,然后用稀硫酸或柠檬酸将沉淀溶解,再将两部分溶液混合,用5%NaOH调整pH至规定值。
(3)化学镀镍
化学镀镍配方1#:硫酸镍20~30g/L,次亚磷酸钠20~30g/L,硼酸10~20g/L,乳酸10~30ml/L,pH=4.5~6.0,83±2℃。镀液的pH由6.0逐渐调至4.5,然后平稳施镀,可得到非晶态的化学镀镍层。若起镀时pH=4.5左右,这样镀层与预镀层由于pH相差较大,镀层磷含量变化太大,从而引起内应力,造成镀层分层脱落现象。配方2#:NiSO4.7H2O25~30g/L,NaH2PO2.H2O 25~30g/L,NaAC 15~20g/L,Na3C6H5O7.2H2O 15~20g/L,添加剂B1(稳定剂)适量,添加剂B2(加速剂)适量,pH=4.8~5.2,88±2℃,1h,装载量1dm2/L,压缩空气搅拌150cm2/min,镀速15~20μm/h。
(5)热处理
化学镀镍层的硬度可通过热处理进行调整,组织仍为非晶状,使底层含量分布趋于均匀,且从基体就开始有少量的磷,使底层与镀层的结合力更好,组织更均匀细小,弥散度提高,镀层表面的光洁度、镀层的耐蚀性、耐磨性均有所提高。考虑到锌合金的熔点较低,为防止工件变形,采用底温度长时间热处理,如220±5℃,5h显微硬度增加5倍以上。也有人采用180℃×1h的热处理条件。
15 镁合金化学镀镍的预处理方法
按照常规的涂覆工艺,在镁合金表面很难获得结合力好的化学镀镍层。因为在化学镀镍的前处理工序转换间镁合金也易氧化。本工艺在化学镀镍前增加一道碱活化工序,将前处理进行中生成的氟化物及氧化物膜溶解,使表面活化再化学镀镍,便能获得结合力良好的化学镀镍层。
预处理工艺流程:除油(碱液煮沸)→碱刻蚀(Na4P2O7.10H2O 100~200g/L,NaNO330~100g/L,室温,1~2min)→酸活化(H3PO4.200ml/L,NH4HF 100g/L,室温,1~2min)→碱活化(Na2HPO2.H2O 25g/L,螯合剂15g/L,pH=9~10,室温,1~2min)
化学镀镍配方:Ni3K6H5O7,NaHPO4.H2O 25g/L,Na4P2O7.10H2O 50g/L,NH4F 5~10g/L,=9~10,<60℃,10~60.
16 钛合金化学镀镍的预处理方法
由于钛金属活性大,新鲜表面暴露在含氧介质中很快被氧化,形成一层致密的、稳定性很高的氧化膜,若在其表面直接化学镀镍是相当困难的。为了在钛合金上获得结合力好的镍层,必须在施镀前采用适当的预处理以改善镀层与基体的结合力。采用下列预处理方法,操作简单,可实现钛合金直接化学镀镍,获得结合力良好的镀层。
(1)浸蚀
较好的钛合金浸蚀必须含少量氢氟酸,但含量不能太高,否则会造成钛合金表面腐蚀不均匀,甚至出现凹凸不平的表面。这是因为合金中钒比其它元素更耐蚀的缘故。同时如果溶液中含有硝酸,使钛表面发生钝化,不能进行镍的自催化沉积。
浸蚀液为:盐酸(36%~38%)94~96份,氢氟酸(70%)4~6份,室温,2min。钛合金浸蚀后,外观腐蚀均匀光亮。
(2)活化
活化液中含有氟化物和乳酸。氟离子的存在加速了钛氧化膜的溶解。乳酸作为镍的络合剂,当溶液中没有乳酸时,活化膜结合力差。因为活化的钛合金较容易与溶液中的镍离子发生置换反应:2Ti+3Ni3+→2Ti3++3Ni。随着乳酸的加入,镍离子被络合,发生上述反应的困难越大,导致置换反应后镍与钛基体的结合力越牢固。过量乳酸对活化没有影响。温度越高越有利于钛氧化膜溶解和活化基表面与镍离子的置换反应;若温度越低,活化时间增长,效果变差。pH值越低活化反应越迅速,不但钛氧化膜溶解,而且活性钛也发生腐蚀,置换反应的镍同时也受到浸蚀,导致活化膜的结合力越差;pH值越高,钛氧化膜越稳定(不溶解或很少溶解),活化反应越慢。当pH值>6时活化反应几乎不发生。其他条件正常下,活化时间越长活化越充分,当活化基础课表面露出后,表面生成一层具有催化活性的、均匀的黄褐色膜,便发生了镍与钛的置换反应,直至钛合金基体被镍层完全覆盖后转换反应停止,所以活化时间越长越好。如果活化不充分,将使后续的化学镀镍局部无镀层或鼓泡。
活化液为:乙二醇700ml/L,酸性氟化铵35g/L,氯化镍20g/L,硼酸50g/L,乳酸20ml/L,醋酸(99%)180ml/L,pH<6,>50℃,30min
(3)化学镀镍
工艺酸方:硫酸镍20g/L,次亚磷酸钠25g/L,络合剂15g/L,乳酸18g/L,丙酸钠18g/L,pb2+微量,pH=5,85%,阴极移动。本配方适用Ti-6Al-4V和Ti-15V-3Al-3Cr等钛合金施镀,镀层结合力良好。
17 粉末冶金件化学镀镍的预处理方法
(1)烘油
烘油温度250~300℃,油烟除尽为止。烘油是化学镀镍的关健工序之一,对后继的除油除锈工作起很大的促进作用。
(2)洗涤
热水洗涤温度>85℃,比一般材料表面处理热水洗涤的温度高些,利于清洗工件孔内渗入的碱液及皂、脏物等。
(3)阳极除油
为更大限度地减少碱液渗入工件内孔的机会,利用阳极除油。除油液为:NaOH 30~50g/L,Na2CO3 20~30g/L,Na3PO4.10H2O 20~30g/L,NiSiO3 3~5g/L,60~90℃,DA=3~10,3~5min。
(4)弱腐蚀
HCl100~150g/L,室温,0.5~2min,时间不能过长,洗涤要彻底。
值得指出,粉末冶金件不宜用吹砂除锈,尽管吹砂后表面光洁,但砂末能渗入工件孔隙,在化学镀镍时,砂末会逸出和附看在工件表面,影响镀层质量。另外工件洗涤要彻底,避免镀层出现“发花”现象。
18 退除化学镀镍层有哪些衫配方
化学镀镍导的退除要比电镀镍层困难得多,特加紧是对于高耐蚀化学镀镍层更是如此。不合格的化学镀镍层应在热处理前就进行退除,否则镀层钝化生退镀更困难。要求退镀液必须对基体无腐蚀,其次镀层厚度、退镀速度、退镀成本等因素都要考虑。
(1)化学退镀法
化学退镀法不使工件受腐蚀,适用几何形状复杂的工件,且可做到退镀均匀。
配方1#:浓HNO3,20~60℃。本液成本低,速度快(30~40μm/h),毒性小。适用尺寸精密要求不高的工件退镀,防止带入水、退镀完毕迅速入流水中清洗。
配方2#:HNO3(1∶1),20~40℃,退速快(10μm/5~6min),适用不锈钢。
配方3#:浓HNO3 1000ml/L,NaCl 20g/L,尿素10g/L(抑制NOX气体的生成),六次甲基四胺5g/L,室温,退速20μm/h。
配方4#:间硝基苯磺酸钠60~70g/L,硫酸100~120g/L,硫氰酸钾0.5~1g/L,80~90,适用铜及铜合金工件的退镀,退镀表面为深棕色时,取出后充分清洗,再除棕色膜(NaCN 30g/L,NaOH 30g/L,室温)。
配方5#:HNO3∶HF=4∶1(体积比),冬天适当加温,退速快,铁基体不腐蚀。但HF一定要用分析纯(用工业级HF配槽,易发生爆炸)。
配方6#:硝酸铵100g/L,氨三乙酸40g/L,六次甲基四胺20g/L,pH=6,室温,退速1/5min,成本低。
除上述酸性化学退镍法外,还有碱性化学退镍法,对普通碳钢工件无腐蚀作用,但温度高、时间长、效率低。如间硝基苯磺酸钠100g/L,NaOH 100g/L,乙二胺120ml/L,十二烷基硫酸钠0.1g/L,60~80℃。调整时补加间硝基磺酸钠,可使退速恢复到最高退速的80%。
(2)电解退镀法
配方为:NaNO3 100g/L,氨三乙酸15g/L,柠檬酸20g/L,硫脲2g/L,葡萄糖酸钠1g/L,十二烷基硫酸钠0.1g/L,pH=4,室温,DA=2~10A/dm2,阴极10#钢,SK∶SA=23∶1。
19 如何选好化学镀镍的设备
(1)避免槽体材料的污染性
槽体材料和内壁涂料的优劣的对化学元素镀镍有一定的影响。一般认为聚丙烯槽、内衬软PVC钢槽、耐酸搪瓷槽、耐热耐酸陶瓷槽都存在导热性和槽体强度差的缺点,唯有不锈钢槽(1Cr18Ni9Ti)效果很好。因不锈钢在化学镀镍液中呈惰性,镍不易在其表面还原沉积。且导热性好,强度高和制做方便等。但不锈槽需通以0.5A/dm2的阳极电流保护,结构复杂。最好在不锈钢槽内壁浸涂一层ZD-1溶胶,或TZ103-3防腐涂料,还可喷涂适当厚度的聚四氟乙烯,如TEFLONS、F46等涂料,情况十分理想,不会发生槽壁有金属还原沉积之迹象。而且槽结构简单,维护方便(涂层可修补)。
实践还表明,软、硬PVC(聚氯乙烯)、软、硬PP、耐酸橡胶对化学镀镍溶液有不同程度的影响,表现为:镀液稳定性异常差;分散能力下降;镀速下降或停镀;镀层光亮提高,但脆性增大等。其中软PVC的影响显著,其危害具有持久性,即无论镀液更换多少次,镀液都会受到软PVC污染。而其他几种材料对镀液的影响较小,并且都是一次性影响。为消除它们的影响,建议不选用软PVC外,对其他几种材料预先用80℃以上的热水浸泡10b以上,效果良好。
(2)改善加热管的传热性
采用水套外电炉加热,避免槽液成分分解过快,兼有调控温度的功能(配套调压器)。还可用蒸汽直接加热,不但提高了蒸汽的利用率,而且加快了升温速度。加热管应用经抛光的316不锈钢管,加热管的下方应设有空气搅拌(无油空气),这样可加速热传递,防止局部过热。为减轻蒸汽冲水发出的噪音,可在蒸汽管上焊一段直径2倍于蒸汽管的消音管,消音管上有20个平行槽底的小孔,这些出气孔的总各要大于消音管直径的确2倍,消音效果极佳。一般也允许采用浸入式加热器直接加热,如石英加热管、聚四氟乙烯加热管等。
(3)改良滚筒结构的合理性
小工件应装入滚筒旦滚镀,滚桶应做得大一些,透水性要好(工件密集,负载极高),滚筒装载工件不应超过容积的1/3,小工件装载还应少一些。为了提高生产效率,应把流通筒做成长方形,每个镀槽放多个滚筒同时工作。
(4)注意过滤机的使用性
注意化学镀镍溶液的过滤形式及滤芯精度的选择。对于镀层要求不高,特别是一些滚镀工件,采用间歇过滤或低温过滤,即在升温过程中过滤镀液;对于要求较高、镀层较厚,特别是一些挂镀工件,或一些精密工件,则必须连续过滤,应成对配置过滤机,便于清洗和更换滤芯。
必须选择合适的滤芯精度和流量,一般滤芯精度为0.1~0.2μm,流量为3~5m3/h,或为镀液体积的10~30倍/h。同时用10m3/h的泵循环搅拌镀液
铸铁复合化学镀镍前处理工艺为:机械抛光→除油除锈→活化处理。但不同的活化方法,直接影响镀层的结合力和孔隙率。筛选最佳阴极活化工艺为:70%H2SO4,室温(最佳200OC),DK=8A/dm2,10s。本活化液可保证镀层结合力最大、孔隙率均为零。
2、如何改善不锈钢化学镀镍层的结合力
不锈钢件(传动轴、啮合件、动配合件等)化学镀镍,可改善镀层的均匀性和自润滑性,比电镀铬好。但不锈钢化学镀镍常因前处理不好而造成镀层与基体结合力不理想,成为实际生产中迫切需要解决的问题。
原工艺流程:机械抛光→有机溶剂除油→化学除油→热水洗→电化学除油→热水洗→冷水洗→30%HCl→冷水洗→20%HCl(50OC)→冷水洗→闪镀镍→化学镀镍。
原工艺的缺点:单独用HCL除氧化皮效果不好;形状复杂件闪镀镍因覆盖能力不好而影响到化学镀镍的均匀性;因工序较长有可能造成不锈钢新鲜表面重新被氧化成膜;闪镀镍溶液易污染化学镀镍溶液等。为此,有人改进工艺。
改进工艺流程:抛光、除油工序同原工艺→混酸除膜(25%HCl+8%HNO3+10%HF)→冷水洗→活化(10%HCl+5%NH4F,60OC)→热水洗→化学镀镍。
改进工艺的优点:①采用混酸除去不锈钢表面难溶的FeCrO4氧化膜、Si、SiO2,使基体表面的化学活性增强;②工序简化,避免了不锈钢新鲜表面重新被氧化;③增加基体的预热工序,消除镀层与基体因温差而产生的应力。因此,化学镀镍与基体结合力好,镀速快等。3 如何进行减压化学镀镍
减压化学镀镍,用镀液的动态载荷取代静态载荷,大大扩展了化学镀镍的应用范围,镀层光亮平整、针孔隙低、耐蚀性好。本法适用小口径长管内壁化学镀镍(φ内≥4cm以上各种细其整平性)。解决办法:系列压力差(P0—P1)控制在(-5.3×-66.7)×103Pa内,管径细,适当减少压差,降低镀液流速;管径粗,可适当增加压差,提高镀液流速。本工艺系统负压不高,操作安全简便。
4 喷淋化学镀镍工艺
采用喷淋可解决大型工件局部化学镀镍的困难,是实行现场施镀的有效方法,既经济又省时。
列举牵引轮(直径2050mm,轮面宽70mm,轮壁厚25mm,自重约2t)过线的外圆面喷淋化学镀镍工艺过程:除锈抛光(手动砂轮)→磨光(砂纸)→除油(表面活性剂)→带压热水冲洗→带压冷水冲洗→双面喷淋酸浸蚀→带压双向水冲洗→双向喷淋弱浸蚀→甩干轮面浮酸→双面喷淋化学镀镍。
注意问题:①在浸蚀、水洗、甩干浮酸时要提高牵引轮转速;②弱浸蚀用CP级盐酸,并加热至65OC,为牵引轮预热;③为消除弱浸蚀过程轮面上滞留酸的影响,开始喷淋化学镀镍的pH值取上限值(pH=10.0),喷淋过程中牵引轮转速不低于10r/min。
5 钢铁化学镀镍的防护作用
(1)提高海洋结构件的抗腐蚀疲劳寿命
试验表明:海洋结构件化学镀镍可提高抗腐蚀疲劳寿命1.5~2.5倍,且镀层具有相当塑性,与基体结合力牢固。
(2)提高磨损件的使用寿命
如纺机件“钢令”及气压件填料盒化学镀镍后,前者上机台运行半年,表面未出现沟槽仍能正常使用,可操作性良好(无走速期,纺纱光滑而羽毛很短,也不易断头)。克服了渗碳钢“钢令”走速期长,耐磨性差(运行三个月需抛光才能用),可操作性差(纺纱断头频繁、纺纱羽毛长、表面粗糙不光滑)等缺点。后者运行二年后,无腐蚀、磨损,镀层仍然完好,保持原有光泽,优于不锈钢填料盒(不锈钢填料盒运行二年后表面发生蚀点),节省填料盒的材料及机加费用。
(3)提高风机叶轮的防护性
如磷肥厂的风机叶轮原使用橡胶或玻璃钢衬层防腐,因磷酸尾气中含有氟化氢等强酸性气体,且使用温度高,使用寿命仅有4个月左右(发生脱层和脆性破裂现象)。改为化学镀镍后使用寿命延至两年左右,保证了生产的安全运行,又节约了4%的资金。
(4)提高大型设备整体抗恶劣环境和工作条件的能力。
如烯烃厂的EA-123换热器(面积达3000m2),因恶劣环境和工作条件,成为抗腐蚀能力差的老大难问题。经整体一次性化学镀镍(表面均匀无斑点、裂纹、结瘤,无边解效应,结合力强等),运行二年后,清除表面油污后仍可见明显的镀层光泽,镀层保持完好。这在国内尚属首例。又如炼油厂的冷换设备化学镀镍取代了有机涂料的防腐,使用寿命显著提高,确保了系统的长期安稳运行。尤其在低碳钢的管束上化学镀镍后,在H2S、HCl-H2S-H2O、常顶油气、硫磺尾气等介质中抗腐蚀性能优良,还能延缓冷却水的结垢速度。
大型设备化学镀镍工艺流程:喷砂除锈→冷水冲洗→酸洗活化→冷水冲洗→化学镀镍(作防腐层厚度25-50μm)→冷水冲洗→钝化→冷水冲洗。
由于化学镀镍的优异防腐蚀性,可获得可观的经济效益。据介绍,换热器管速(长6m,直径1m)化学镀镍获得直接经济效益109.6万元,间接经济效益更为可观。
化学镀镍配方:NiSO4·6H2O 23g/L,NaH2PO2·H2O 20g/L,CH3COONa·3H2O 14g/L,Na3C5H6O72H2O 6g/L,pH=4.0~5.0,温度74~84OC,沉积速度约20μm/h,镀层磷含量8.5%~12.5%。
6 模具化学镀镍的几个问题
为了提高模具加工件的质量,改善加工件的脱模性,延长模具使用寿命,模具必须镀覆硬铬或化学镍层,但它们各有利弊,如硬铬层的硬度高、摩擦系数小、脱模性好等,但耐蚀性较差;化学镀镍操作方便,耐蚀性好,而其他镀层性能却较硬铬层差。所以,模具单一镀硬铬或化学镀镍使用寿命都短(仅2周左右),无法满足工业要求。最好选择复合镀层。
(1)化学镀镍套硬铬工艺
施镀工艺流程1#:化学镀镍→热处理→阴极活化处理→镀硬铬
热处理条件:(95±10℃,3~5h;阴极活化:H2SO4 250~350g/L,含氟添加剂 15~25g/L,DK=2~5A/dm2。
化学镀镍配方:NiSO4·6H2O 21g/L,NaH2PO2·H2O 24g/L,C3H6O3 27ml/L,C3H6O2 2ml/L,NaC3H5O2 15g/L,pH=4.6~4.82,温度88±2OC。
本工艺流程适宜于普通模具镀覆,使用寿命高。
施镀工艺流程2#:闪镀镍→后继工序同流程1#。
本工艺流程适宜PUC塑料模具镀覆,镀层结合力非常好,使用寿命高。若取消闪镀镍,化学镀镍层与基体(合金钢)结合力仍较差,铬层和镍层一起从基体上起皮。
(2)成套模具选择不同的单一镀层组合使用
施镀工艺流程1#除油→水洗→酸洗→活化→水洗→化学镀镍→热处理(400℃,1h)。
本工艺流程适用于玻璃钢窗成套模具之一的有沟槽模具化学镀镍,由于镍层均匀一致(沟槽处皆为38~40μm镀层厚度),克服了镀硬铬因尖角效应而导致钩槽处无镀层的缺陷,保证了玻璃钢窗框的拉制。有沟槽模具系A3钢制成,抛光后表面粗糙度为Ra0.1~0.2,镀镍层光亮如镜。
化学镀镍配方:NiSO4·6H2O 20~30g/L,NaH2PO2·H2O 30~40g/L,NaAC20g/L,柠檬酸5~7g/L,丁二酸9~10g/L,十二烷基硫酸钠0.01~0.02g/L,硫脲0.002g/L;pH=4.5~4.8,温度(88~90)±3OC,2h,装载量1dm2/L,镀速17μm/h。
施镀工艺流程2#:前处理工序同流程1#→镀硬铬。
本工艺流程适宜玻璃钢窗成套模具之一的无沟槽模具镀硬铬,可降低生产成本(低于化学镀镍),硬度高(1100HV0.1)。
(3)控制化学镀镍质量的因素
①控制镍层磷含量。镍层磷含量升高,硬度降低,呈现出压应力;反之,磷含量降低,引起拉应力(可达15~45MPa),表面产生孔隙和 裂纹。所以,化学镀镍磷含量控制在7%~11%。②掌握热处理条件。化学镀镍层经热处理可提高显微硬度、耐磨性及耐热性能;消除镀层的脆性,降低镀层的内应力;大大改善镀层与基体的结合力。但热处理条件视模具对耐蚀性的要求不同而异。如注射模、挤压模热处理温度190~210OC,保温3h。若温度高于260OC时,开始形成弥散的Ni3P质点,使体积收缩达40%~50%,呈现出拉应力状态,使镀层产生微裂纹,以致于基体金属裸露出来。但是,精密模具的工作温度会高达600℃左右,故处理温度600OC为佳。
7 铝合金化学镀镍前的预处理新工艺
铝合金化学镀镍前采用二次浸锌最普通,但浸锌存大的缺陷:①锌层易溶解于酸性化学镀镍溶液中;②由于基体与镍层之间夹杂锌层,在腐蚀介质中形成电偶腐蚀(Al-Zn-Ni),将导致镀层鼓泡或脱落,降低耐蚀性;③经浸锌后化学镀镍,不宜进行400oC热处理,会造成浸锌层空松。同时铝和镍膨胀系数相差悬殊,在高温时会引起足够的应力,使镀层与铝之间产生破裂。而以活化代替浸锌,为化学镀镍提供了一个较好的底层,镀层与在材有结合力能达到同浸锌一样好的结果,是一种很有用途的铝合金前处理新工艺。
活化处理液为:NiSO4。6H2024~30g/L,HEDP 40~50g/L,稳定剂N25~30ml/L,Ph(NaOH调整)>12,室温,1~4min。控制活化时间至关重要,对某一具体配方,可通过实验杰确定最佳浸清时间,即当表面完全呈均匀灰色时,进行化学镀镍可得到最佳镀层质量。
8 如何保证电子微组铝件化学镀镍的质量
微组铝件(放大器铝腔体、微波开关、振荡器和天线蚀电架等)化学镀镍取代铝镀银工艺必须保证外观装饰性、优异附着力、耐腐蚀性和理想的物理、化学特性(电磁屏蔽、焊接性、高硬度、耐磨、高低温等)。关键在于优化工艺配方和镀层组合。
典型工艺流程:有机溶剂支油(LYC2被镀铝件)→碱性除油(或碱腐蚀) →硝酸浸蚀→二次浸锌→碱性化学镀镍→酸性化学镀镍→热处理
(1)改良特殊预处理工艺
选择了含镍盐和辅助络合剂的改良锌酸盐酸方,碱浓度适中,特别是含有镍盐,并将酒石酸钾钠含量升高,又增加添加剂,使镍离子呈较稳定络离子开式存在,从而使镍离子与锌离子一起缓慢而均匀地置换沉积在铝表面,得到的锌镍合金层比从传统浸锌液中获得的浸锌层更薄更均匀。且控制Zn-Ni层重量在1~2mg/dm2范围,能充分保证铝上镀层附着力和抗蚀性良好;特别是含镍的锌层为随后的化学镀镍沉积初期提供了充足的催化核心,得到均匀细小晶核,这是提高随后镀镍层附着力的一上重要因素。
改良锌酸盐配方:NaOH 240g/L,ZnSO4 120g/L,NiSO4 60g/L,KnaC4H4O6 120g/L,添加剂10~30g/L,室温,2~3min。
(2)改善预镀底层
由于锌层不耐性液腐蚀,必须预镀碱性化学镀镍作底层。但碱性镀镍液存在沉积速度较慢(5~10m),含P量较低(4%~6%),抗蚀性较差等缺点。要求改变还剂和络合剂浓度,选择最佳期PH值范围,保证镀液稳定,镀速适中,并能在浸锌层表面得到一层结晶细小、均匀与基体结合良好的预镀薄镍层。
改进碱性镀镍配方:NiSO4。6H2O 25g/L,NaH2PO。H2O 25g/L,Na3C6H5O7 45g/L NH4Cl 30g/L,35~45Oc,Ph=8~9
(3)提高镀层的防护性与装饰性
优选酸性化学镀镍配方,含有少量学亮剂,镍离子与次亚磷酸根子的摩尔浓度比值控制在0.4左右,保证镀速适中(16~20m/h),溶液稳定(6周期以上,即使煮沸镀液也不会分解)。此外加入复合络合剂,防止生成亚磷酸镍沉淀。从本久液中可镀出呈学亮黄白色的镍层(含磷量8%~10%),耐蚀性好(镍层厚度25μm经中性盐雾试验48h,耐蚀等级9.5)。建议在海上或恶劣环境使用的工件化学镀镍厚度设计为≥25μm。
优良酸性化学镀镍溶液:NiSO4。6H2O 27g/L,NaH2PO2H2O 29g/L,C2H5Ona 25g/L,Na3C6H3O7 25g/L,络合剂适量,学亮剂少量,pH=5,85~90oC,装截量0.5~1.5dm2/L。日常生产根据分析结果加镍盐、还原剂。
(4)适当的后处理
铝合金化学镀镍后进行热处理(150~200oC,3h),可以消除层中残留的H原子,松驰内应力,进一步提高镀层与基体附着力和硬度。
9 铸铝轮毂化学镀镍的工艺过程
铸铝轮毂化学镀镍能提高其使用性能和装饰性能,具有硬度高、耐磨、耐腐蚀、外型复制好等特点。铸铝合金(AlSi7MgO3)化学镀镍工艺流程:手工除油(洗衣粉溶液)→化学除油→化学浸蚀→二次浸锌→碱性化学镀镍→酸性化学镀镍→烘干
主要工序如下:
⑴化学浸蚀:
除去轮毂表面的铝氧化膜及Si、Mg等元素,以保证表面呈均匀的富铝状态;同时起到抛学作用。化学浸蚀溶液:HNO3 60-70ml/L,HF15-20ml/L,甘油ml/L,室温,0.25-0.5min。
⑵浸锌
经二次浸锌,锌层更均匀、细致,与基体结合力更好。浸锌溶液:NaOH 525g/L,ZnO 100g/L,FeCl3。6H2O1g/L,酒石酸钾钠12g/L,室温,一次浸锌0.5min,二次浸锌15~20s。浸锌后工件清洗一定要充分。
⑶碱性化学镀镍
NiSO4。6H2O 30g/L,NaH2PO2。H2O 30 G/L,Na3C6H5O7。2H2O 10~15g/L,三乙醇胺50g/L,pH=8.5~9.5,30~35Oc,3~5min。
⑷酸性化学镀镍
NiSO4。6H2O 30g/L,NaH2PO2。H2O 30g/L,乳酸ml/L,络合剂Ⅱ(丁二酸、丙二酸等)10g/L,缓蚀剂(乙酸、丙酸、钾盐、钠盐等)10g/L,加速剂(脂肪酸、NaF等)2g/L,稳定剂(pb2+、MoO2-4),Ph=4.6~5.4,88+-2oC,装载量1dm2/L。
本配方使用二种络合剂,可形成由两种络合剂同时与镍离子络合的混合物,既可提高镀速,又能增加镀液的稳定性,有效抑制亚磷镍的沉淀。
10 铝合金电子机壳化学镀镍的优越性
电子机壳化学镀镍综合性能好。提高了装饰性(银白色、柔和、美观)、防护性(防护性是电镀Ni层的二倍)、导电性(电阴率51~60μΩ。Cm,导电、电磁屏蔽效果好)、散热惦、润滑性(P有一定的自润滑作用)、精密性(厚度均匀、可控,盲孔处的镀层完好)、钎焊性、可修复必(Ni层再镀性好)等。大幅度提高了整体涂覆的质量,满足了军事电子系统工程的设计和使用要求,既保证了高可靠性,又改善了机壳的接地和互联效果。总的来说,电子机壳化学解放区昝最佳涂覆。
11 解决铝质槽筒化学镀镍层易擦灰的方法
为了增络纱机上铝质槽筒表面的耐磨性,一般采用化学镀镍工艺。但在使用过程中纱与槽筒表面的镍层磨擦后,白纱表面附着一层黑灰,影响产品质量。为了解决其表面擦灰问题,采用镀后热处理。由于P和Ni会转变为Ni3P并高度弥散析出(镀层结构部分或全部转变为晶态结构,增加了镀层塑性变形时势滑动阻力,使镀层强化,使其耐磨性和硬度均大大提高。但热处理条件的正确与否,直接影响到工件的变形及镀层的耐蚀性。因铝件槽筒在高温热处理后易变形,况且久层的耐蚀性随着热处理温度升高而降低(镀层结构变为混合相,结构高度不均匀,形成电位差,混合相间就易形成腐蚀微电池)。因此,最佳热处理温度不超不定280oC,保温3h。
12 何保证铝基剪杆化学镀镍套铬的质量?
铝基剪杆化学镀镍套硬络,既具有很高的耐磨性和耐腐蚀性,又有较好的抗冲击性能,避免了高硬度的铬层与较软的铝基体直接接触而可能引起的开裂、凹陷。施镀工艺流程:除油→二次浸锌→化学镀镍→活化→硬铬→除氢。为保证化学镀镍套铬的质量,关键工艺在于:
(1)化学镀镍层的结合力受浸锌液成分影响较大。较佳的浸锌液:
①NaOH 180~200g/L,ZnO 18~30g/L,NaC4H4O6。H2O 50g/L,NaNO2 1~2g/L,25~35Oc,40~45S;②NaOH 100g/L,ZnO 30g/L,KnaC4H4O6。6H2O 10g/L,FeCl3 2g/L,NaNO3 1g/L,室温,30~60s。
(2)保证化学镀镍层无孔隙
由于镀铬溶液的腐蚀性和高电流冲击。很容易把镍层剥落。所以镍层必须无孔隙。当镍层达到15μm时,已测不出孔隙。
(3) 有合理的镀硬铬工艺
试验表明,传统的镀铬液均不满意(镍层肃离或铬层起皮),唯有稀土镀铬液可施镀厚镍 层(20μm)上套厚铬(5·10·15μm铬层)。稀土镀铬液:铬酸130-150g/L,硫酸0.5~0.8 g/L,稀土添加剂1.5~2.0 g/L, Cr3+1~2 g/L ,50~55℃,DK40~45A/dm2,镀速40μm/h。
(4)化学镀镍层与硬铬层必须有合适的厚度比
当硬铬层要求20μm时,化学镀镍层>25μm,双层镀层结合力优良。这是因为硬铬层有很大的内应力(表现为拉应力),随镀层度增加而迅速增大,当应力大于镍层与基体的结合力时,就可以把镍层剥落,所以,只有化学元素镀镍层达到相应的厚度,才能使镍层的结合力大于硬铬层的拉应力。且镀后进行除氢处理品,消除铬层部分内应力。
本工艺用于剪杆大批量生产并出口,质量达到国外水平。
13 化学镀镍的常见故障及解决办法
(1)沉速低
镀液pH值过低:测pH值调整,并控制pH在下限值。虽然pH值较高能提高沉速,但会影响镀液稳定性。
镀液温度过低:要求温度达到规范时下槽进行施镀。新开缸第一批工件下槽时,温度应达到上限,反应开始后,正常施镀时,温度在下限为好。
溶液主成分浓度低:分析调整,如还原剂不足时,添加还原补充液;镍离子浓度偏低时,添加镍盐补充液。对于上规模的化学镀镍,设自动分析、补给装置是必要的,可以延长连续工作时间(由30h延至56h)和镍循环周期(由6周延至11周)。
亚磷酸根过多:弃掉部分镀液。
装载量太低:增加受镀面积至1dm2/L。
稳定剂浓度偏重:倾倒部分,少量多次加浓缩液。
(2)镀液分解(镀液呈翻腾状,出现镍粉)
温度过高或局部过热:搅拌下加入温去离子水。
次亚磷酸钠大多:冲稀补加其它成分。
镀液的pH值过高:调整pH值至规范值。
机械杂质:过滤除去。
装载量过高:降至1dm2/L
槽壁或设备上有沉淀物:滤出镀液,退镀清洗(用3%HNO3溶液)。
操作温度下补加液料大多:搅拌下少量多次添加。
稳定剂带出损失:添加少量稳定剂。
催化物质带入镀液:加强镀前清洗。
镀层剥离碎片:过滤镀液。
(3)镀层结合力差或起泡
镀前处理不良:提高工作表面的质量,加工完成后应清除工件上所有的焊接飞溅物和焊渣。工件表面的粗糙度应达到与精饰要求相当的粗糙义,如碳钢工件表面粗糙度Ra<1.75μm时,很难获得有良好附着力的镀层;对于严重锈蚀的非加工表面,可用角向磨光机打磨,最好采用喷砂或喷丸处理;工件镀前适当的活化处理可以提高镀层的附着力。如合金钢、钛合金可用含氟化物的盐酸活化后,与碳钢件混装施镀;高级合金钢和铅基合金预镀化学镍;碳钢活化时注意脱碳。
温度波动太大:控制温度在较小的范围波动。
下槽温度太低:适当提高下槽温度。
清洗不良:改进清洗工序。
金属离子污染:用大面积废件镀而除去。
有机杂质污染:活化炭1-2g/L 处理。
热处理不当:调整热处理时间和温度。
(4)镀层粗糙
镀液浓度过高:适当冲稀镀液。
镀液的pH值过高:降低pH值至规范值。
机械杂质:过滤除去。
亚磷酸盐过高:弃掉部分镀液。
加药方法不对:不可直接加固体药品或用镀液溶解药品。
清洗不够 ,带入污染:加强清洗。
络合剂浓度偏低:补充络合剂。
工艺用水污染:使用去离子水或蒸馏水。
(5)镀层不完整(漏镀)
前处理不当、镀件局部钝化或油污、清洗水不干净等:加强前处理,更换清洗水。
装挂不对有气袋:改进装挂方法、抖动工件、变换位置等。
十二烷基硫酸钠污染:活性炭吸附。
金属离子污染:除去(见上述),过滤。
底金属影响:镀前闪镀镍。
稳定剂过量:弃去部分镀液。
(6)镀层针孔(通常镀层厚度达10μm以上是无孔)
工件前处理不当和酸洗后停留时间过长:提高工件表面加工质量,酸洗后应在30s内进入镀液。
pH值过高:降低pH值。
镀液组份变质和老化:报废镀液。
悬浮不溶物:过滤除去。
装载量过大:减至1dm2/ L,降低pH值。
金属离子污染:除去。对于含pb、cd、Zn、Sn等元素的基材,在施镀镍前,最好电镀1~5μm的镍打底,以阻止有害元素进入镀液。
搅拌不充分:摆动工作。
有机杂质污染:活性炭处理。
(7)镀液不沉积镍
稳定剂浓度过高:弃去部分镀镍。
表面未活化:改进镀前处理工艺。
表面非催化:镀前表面催化处理
镀液pH值、温度过低:调整之。
金属离子污染:加1~2g/L活性炭过滤,通电处理。
(8)pH值变化快
前处理溶液带入:改进清洗工序。
装载量太大:减少受镀面积。
pH值出范围:调pH至最佳范围。
(9)镍离子消耗过快
槽壁和设备镀上镍:处理方法同(2)--⑥
载量太大:减少装载量。
液分解:滤去镀液分析调整或报废。
补充硫酸镍不及时:补加主盐。
(10)镀层光亮度下降、发黑或不均匀
镀液过度浓缩(水份蒸发超过30%):补水
镀液老化(使用寿命达6周期):报废旧液。
络合剂用错或络合剂、稳定剂变质:无法恢复镀液性能时只能将镀液报废。
施镀条件不当,如pH值或温度过高,溶液搅拌和工件阴极移动不良等:调低pH值至规定值的下限,当镀液寿命超过2周期时,pH值控制在4.2为好。但pH=3.5---4.0之间也能得到光亮的镀层;良好的镀液搅拌系统工程和工件移动以及低温施镀都有利于提高镀层光亮度。并控制镀液流速<0.3m/s,避免造成漏镀。
有机杂质污染:处理方法同(3)---⑥。
前处理不充分:加强前处理。
(11)镀层有麻点
工件表面光洁度较低:尽量提高工件的表面质量。
在施镀时调整pH值:施镀时不调pH值。
镀液不稳定和镀液中悬浮颗粒较多:加强过滤,补充一定的稳定剂。
工件摆放位置不当:工件较重要的表面朝下或竖直成90o,并将工件预热到70oC以上施镀,可改善工件向上的光洁度。
(12)镀层厚度不均匀(可以看到镀液中气泡的析出量较正常情况下要多)
由于工件几何形状影响工件表面上的氢气逸出不易,有妨碍氢气顺利排出的部位可能造成镀层较薄:最好采用滚镀法。对于较大的工件也应尽可能性在施镀过程中移动、镀液搅拌、降温等,以利于氢气的排出,提高镀层厚度的均匀性。
工件材质不同:不同材料的化学镀镍速度是不同的,所以不同材质的工件一起施镀时,必须分别测量不同材质工件的镀层厚度。
(13)镀层表面化有大量"花斑",局部有暗色条纹或斑块状沉积物(用10倍放大镜观察)
前处理清洗不良,工件表面粘附了某些杂质:更换洗净剂,镀层恢复了均匀的光亮表面。
(14)镀液中毒(工件上的析氢量较正常情况下多,且沉积速度很慢)
稳定剂过量:通电处理。(工件作阴极,不锈钢件阳极,Dk=0.6~1.0A/dm2,电解1~5min;将镀液置于80oC保温24h;如镀液还不行,最好将镀液储存起来,分批与新镀液混合使用。
缓蚀剂污染镀液:酸洗液中缓蚀剂的加入要慎重,要防止微量缓蚀剂带入镀槽中。
(15)镀槽不沉积镀层
镀液中产生一些固体颗粒:将镀液打入备用槽,再用30%(wt)HNO3在40OC下清洗(不能冷洗),钝化镀槽5h,然后用水洗净硝酸,再用干净棉纱擦洗镀槽上附着物。用清水清洗干净。
镀槽的防镀效果不好:为了防止镀槽上沉积镀层,必须采取相应的防镀方法。据称,采用阳极保护法时,以工件作为阴极和参比电极效果 好。在75~85OC的镀液中维持不锈钢镀槽相对施镀的工件的参比电位为+350~550mv时,镀槽有良好的钝化性能。此时的阳极电流密度为20~90mA/m2。当机械杂质进入镀槽或镀槽上有镀层产生时,其维钝电流将有所上升,但很快将下降至正常水平。这样防镀效果好,并且可以提高镀速10%~20%,而且对镀层质量无显著影响。
加热管功率与其表面积之比不当:同样功率的加热管,应作得尽量长一些,管子粗一些,缩小加热管,应作得尽量长一些,管子粗一些,缩小加热管功率与其表面积之比。
施镀设备及挂具用硝酸清洗不够:每次开缸前用硝酸浸泡镀槽、加热管、挂具、滚筒等,即使没有发现镍镀层也应这样做。
(16)镀液混浊
主盐、还原剂浓度超过上限:调整溶液。
络合剂浓度低:补充络合剂。
pH值过高:降低镀液pH值。
14 锌合多铸件如何化学镀镍
锌合金压铸件化学镀镍可提高其表面硬度,改善耐磨性能,拓宽使用范围。由于锌的两性行为,必须进行特殊处理,选择下列工艺:
(1)确定合理的工艺流程
二种典型工艺流程:①弱碱除油→弱腐蚀(1%H2SO4)→活化(焦磷酸盐)→预镀中性镍→化学镀镍→热处理;②水喷蚀(1%~20%H2SO4,10~15s)→预镀中性镍→预热→(柠檬酸1~2g/L,80~90℃,1min)→化学镀镍→热处理。
(2)预镀中性镍
中性镍配方1#:硫酸镍160~180g/L,柠檬酸钠192~216g/L,氯化钠10~16g/L,硼酸25~30g/L;pH=7,DK=4A/dm2,45℃,≥20min。配方2#:硫酸镍100~180g/L,柠檬酸钠130~200g/L,氯化钠15~20g/L,硼酸30~40g/L,添加剂A 3ml/L;pH=7~7.5,DK=1~1.5A/dm2,冲击电流2~4A/dm2,冲击时间5~7min,50~60℃,20~25min,阴极移动20~30次/min。
预镀中性镍应注意:①采用以硫酸镍为主盐的预镀液,接近化学镀镍的成份。pH值应控制在7~7.5左右。②保证底层有足够厚度,改善底层的质量。如配方2#中加入添加剂A,能提高底层与基体结合力,外观变得光滑细致,产品成品率达95%以上。③妥善处理溶液中产生的Ni(OH)2沉淀,恢复镀液的施镀能力。如用虹吸的办法将镀液中下部的沉淀与上部清液分开,然后用稀硫酸或柠檬酸将沉淀溶解,再将两部分溶液混合,用5%NaOH调整pH至规定值。
(3)化学镀镍
化学镀镍配方1#:硫酸镍20~30g/L,次亚磷酸钠20~30g/L,硼酸10~20g/L,乳酸10~30ml/L,pH=4.5~6.0,83±2℃。镀液的pH由6.0逐渐调至4.5,然后平稳施镀,可得到非晶态的化学镀镍层。若起镀时pH=4.5左右,这样镀层与预镀层由于pH相差较大,镀层磷含量变化太大,从而引起内应力,造成镀层分层脱落现象。配方2#:NiSO4.7H2O25~30g/L,NaH2PO2.H2O 25~30g/L,NaAC 15~20g/L,Na3C6H5O7.2H2O 15~20g/L,添加剂B1(稳定剂)适量,添加剂B2(加速剂)适量,pH=4.8~5.2,88±2℃,1h,装载量1dm2/L,压缩空气搅拌150cm2/min,镀速15~20μm/h。
(5)热处理
化学镀镍层的硬度可通过热处理进行调整,组织仍为非晶状,使底层含量分布趋于均匀,且从基体就开始有少量的磷,使底层与镀层的结合力更好,组织更均匀细小,弥散度提高,镀层表面的光洁度、镀层的耐蚀性、耐磨性均有所提高。考虑到锌合金的熔点较低,为防止工件变形,采用底温度长时间热处理,如220±5℃,5h显微硬度增加5倍以上。也有人采用180℃×1h的热处理条件。
15 镁合金化学镀镍的预处理方法
按照常规的涂覆工艺,在镁合金表面很难获得结合力好的化学镀镍层。因为在化学镀镍的前处理工序转换间镁合金也易氧化。本工艺在化学镀镍前增加一道碱活化工序,将前处理进行中生成的氟化物及氧化物膜溶解,使表面活化再化学镀镍,便能获得结合力良好的化学镀镍层。
预处理工艺流程:除油(碱液煮沸)→碱刻蚀(Na4P2O7.10H2O 100~200g/L,NaNO330~100g/L,室温,1~2min)→酸活化(H3PO4.200ml/L,NH4HF 100g/L,室温,1~2min)→碱活化(Na2HPO2.H2O 25g/L,螯合剂15g/L,pH=9~10,室温,1~2min)
化学镀镍配方:Ni3K6H5O7,NaHPO4.H2O 25g/L,Na4P2O7.10H2O 50g/L,NH4F 5~10g/L,=9~10,<60℃,10~60.
16 钛合金化学镀镍的预处理方法
由于钛金属活性大,新鲜表面暴露在含氧介质中很快被氧化,形成一层致密的、稳定性很高的氧化膜,若在其表面直接化学镀镍是相当困难的。为了在钛合金上获得结合力好的镍层,必须在施镀前采用适当的预处理以改善镀层与基体的结合力。采用下列预处理方法,操作简单,可实现钛合金直接化学镀镍,获得结合力良好的镀层。
(1)浸蚀
较好的钛合金浸蚀必须含少量氢氟酸,但含量不能太高,否则会造成钛合金表面腐蚀不均匀,甚至出现凹凸不平的表面。这是因为合金中钒比其它元素更耐蚀的缘故。同时如果溶液中含有硝酸,使钛表面发生钝化,不能进行镍的自催化沉积。
浸蚀液为:盐酸(36%~38%)94~96份,氢氟酸(70%)4~6份,室温,2min。钛合金浸蚀后,外观腐蚀均匀光亮。
(2)活化
活化液中含有氟化物和乳酸。氟离子的存在加速了钛氧化膜的溶解。乳酸作为镍的络合剂,当溶液中没有乳酸时,活化膜结合力差。因为活化的钛合金较容易与溶液中的镍离子发生置换反应:2Ti+3Ni3+→2Ti3++3Ni。随着乳酸的加入,镍离子被络合,发生上述反应的困难越大,导致置换反应后镍与钛基体的结合力越牢固。过量乳酸对活化没有影响。温度越高越有利于钛氧化膜溶解和活化基表面与镍离子的置换反应;若温度越低,活化时间增长,效果变差。pH值越低活化反应越迅速,不但钛氧化膜溶解,而且活性钛也发生腐蚀,置换反应的镍同时也受到浸蚀,导致活化膜的结合力越差;pH值越高,钛氧化膜越稳定(不溶解或很少溶解),活化反应越慢。当pH值>6时活化反应几乎不发生。其他条件正常下,活化时间越长活化越充分,当活化基础课表面露出后,表面生成一层具有催化活性的、均匀的黄褐色膜,便发生了镍与钛的置换反应,直至钛合金基体被镍层完全覆盖后转换反应停止,所以活化时间越长越好。如果活化不充分,将使后续的化学镀镍局部无镀层或鼓泡。
活化液为:乙二醇700ml/L,酸性氟化铵35g/L,氯化镍20g/L,硼酸50g/L,乳酸20ml/L,醋酸(99%)180ml/L,pH<6,>50℃,30min
(3)化学镀镍
工艺酸方:硫酸镍20g/L,次亚磷酸钠25g/L,络合剂15g/L,乳酸18g/L,丙酸钠18g/L,pb2+微量,pH=5,85%,阴极移动。本配方适用Ti-6Al-4V和Ti-15V-3Al-3Cr等钛合金施镀,镀层结合力良好。
17 粉末冶金件化学镀镍的预处理方法
(1)烘油
烘油温度250~300℃,油烟除尽为止。烘油是化学镀镍的关健工序之一,对后继的除油除锈工作起很大的促进作用。
(2)洗涤
热水洗涤温度>85℃,比一般材料表面处理热水洗涤的温度高些,利于清洗工件孔内渗入的碱液及皂、脏物等。
(3)阳极除油
为更大限度地减少碱液渗入工件内孔的机会,利用阳极除油。除油液为:NaOH 30~50g/L,Na2CO3 20~30g/L,Na3PO4.10H2O 20~30g/L,NiSiO3 3~5g/L,60~90℃,DA=3~10,3~5min。
(4)弱腐蚀
HCl100~150g/L,室温,0.5~2min,时间不能过长,洗涤要彻底。
值得指出,粉末冶金件不宜用吹砂除锈,尽管吹砂后表面光洁,但砂末能渗入工件孔隙,在化学镀镍时,砂末会逸出和附看在工件表面,影响镀层质量。另外工件洗涤要彻底,避免镀层出现“发花”现象。
18 退除化学镀镍层有哪些衫配方
化学镀镍导的退除要比电镀镍层困难得多,特加紧是对于高耐蚀化学镀镍层更是如此。不合格的化学镀镍层应在热处理前就进行退除,否则镀层钝化生退镀更困难。要求退镀液必须对基体无腐蚀,其次镀层厚度、退镀速度、退镀成本等因素都要考虑。
(1)化学退镀法
化学退镀法不使工件受腐蚀,适用几何形状复杂的工件,且可做到退镀均匀。
配方1#:浓HNO3,20~60℃。本液成本低,速度快(30~40μm/h),毒性小。适用尺寸精密要求不高的工件退镀,防止带入水、退镀完毕迅速入流水中清洗。
配方2#:HNO3(1∶1),20~40℃,退速快(10μm/5~6min),适用不锈钢。
配方3#:浓HNO3 1000ml/L,NaCl 20g/L,尿素10g/L(抑制NOX气体的生成),六次甲基四胺5g/L,室温,退速20μm/h。
配方4#:间硝基苯磺酸钠60~70g/L,硫酸100~120g/L,硫氰酸钾0.5~1g/L,80~90,适用铜及铜合金工件的退镀,退镀表面为深棕色时,取出后充分清洗,再除棕色膜(NaCN 30g/L,NaOH 30g/L,室温)。
配方5#:HNO3∶HF=4∶1(体积比),冬天适当加温,退速快,铁基体不腐蚀。但HF一定要用分析纯(用工业级HF配槽,易发生爆炸)。
配方6#:硝酸铵100g/L,氨三乙酸40g/L,六次甲基四胺20g/L,pH=6,室温,退速1/5min,成本低。
除上述酸性化学退镍法外,还有碱性化学退镍法,对普通碳钢工件无腐蚀作用,但温度高、时间长、效率低。如间硝基苯磺酸钠100g/L,NaOH 100g/L,乙二胺120ml/L,十二烷基硫酸钠0.1g/L,60~80℃。调整时补加间硝基磺酸钠,可使退速恢复到最高退速的80%。
(2)电解退镀法
配方为:NaNO3 100g/L,氨三乙酸15g/L,柠檬酸20g/L,硫脲2g/L,葡萄糖酸钠1g/L,十二烷基硫酸钠0.1g/L,pH=4,室温,DA=2~10A/dm2,阴极10#钢,SK∶SA=23∶1。
19 如何选好化学镀镍的设备
(1)避免槽体材料的污染性
槽体材料和内壁涂料的优劣的对化学元素镀镍有一定的影响。一般认为聚丙烯槽、内衬软PVC钢槽、耐酸搪瓷槽、耐热耐酸陶瓷槽都存在导热性和槽体强度差的缺点,唯有不锈钢槽(1Cr18Ni9Ti)效果很好。因不锈钢在化学镀镍液中呈惰性,镍不易在其表面还原沉积。且导热性好,强度高和制做方便等。但不锈槽需通以0.5A/dm2的阳极电流保护,结构复杂。最好在不锈钢槽内壁浸涂一层ZD-1溶胶,或TZ103-3防腐涂料,还可喷涂适当厚度的聚四氟乙烯,如TEFLONS、F46等涂料,情况十分理想,不会发生槽壁有金属还原沉积之迹象。而且槽结构简单,维护方便(涂层可修补)。
实践还表明,软、硬PVC(聚氯乙烯)、软、硬PP、耐酸橡胶对化学镀镍溶液有不同程度的影响,表现为:镀液稳定性异常差;分散能力下降;镀速下降或停镀;镀层光亮提高,但脆性增大等。其中软PVC的影响显著,其危害具有持久性,即无论镀液更换多少次,镀液都会受到软PVC污染。而其他几种材料对镀液的影响较小,并且都是一次性影响。为消除它们的影响,建议不选用软PVC外,对其他几种材料预先用80℃以上的热水浸泡10b以上,效果良好。
(2)改善加热管的传热性
采用水套外电炉加热,避免槽液成分分解过快,兼有调控温度的功能(配套调压器)。还可用蒸汽直接加热,不但提高了蒸汽的利用率,而且加快了升温速度。加热管应用经抛光的316不锈钢管,加热管的下方应设有空气搅拌(无油空气),这样可加速热传递,防止局部过热。为减轻蒸汽冲水发出的噪音,可在蒸汽管上焊一段直径2倍于蒸汽管的消音管,消音管上有20个平行槽底的小孔,这些出气孔的总各要大于消音管直径的确2倍,消音效果极佳。一般也允许采用浸入式加热器直接加热,如石英加热管、聚四氟乙烯加热管等。
(3)改良滚筒结构的合理性
小工件应装入滚筒旦滚镀,滚桶应做得大一些,透水性要好(工件密集,负载极高),滚筒装载工件不应超过容积的1/3,小工件装载还应少一些。为了提高生产效率,应把流通筒做成长方形,每个镀槽放多个滚筒同时工作。
(4)注意过滤机的使用性
注意化学镀镍溶液的过滤形式及滤芯精度的选择。对于镀层要求不高,特别是一些滚镀工件,采用间歇过滤或低温过滤,即在升温过程中过滤镀液;对于要求较高、镀层较厚,特别是一些挂镀工件,或一些精密工件,则必须连续过滤,应成对配置过滤机,便于清洗和更换滤芯。
必须选择合适的滤芯精度和流量,一般滤芯精度为0.1~0.2μm,流量为3~5m3/h,或为镀液体积的10~30倍/h。同时用10m3/h的泵循环搅拌镀液
还有剩余内容未读
@ 大神呀

声明:说化有益·表面处理联盟网资料文库文档均为用户分享上传,版权归上传者所有。文档内容是行业专业性知识,知识的严谨度及实用性极强,因此部分价值极高的文章需要付费查看,用户可根据实际需求进行已付费文档下载;付费记录可在“用户中心”-“我的订单”-“我的文库”内查看。由于知识产权的特殊性,付费成功后不支持退换,用户应根据自身需求判断是否需要继续操作。
我们欢迎各方(自)媒体、机构转载、引用我们原创内容,但需严格注明来源。同时,我们也倡导尊重与保护知识产权,如发现文章内容涉及侵权,请通过在线咨询进行投诉,我们会在第一时间核实处理。