近年来,随着磷化前处理技术的不断发展和进步,越来越多的电泳涂装前都会对工件进行磷化处理,目的是为了提高电泳漆膜的附着力、耐蚀性能和全涂层的装饰性。而传统磷化、过渡磷化工艺和薄膜前处理这三者的关系可以理解成技术的升级,后者可以说是为了弥补前者的缺陷而诞生的,为什么我会这样说呢?看看我接下来的分析就可以理解了。
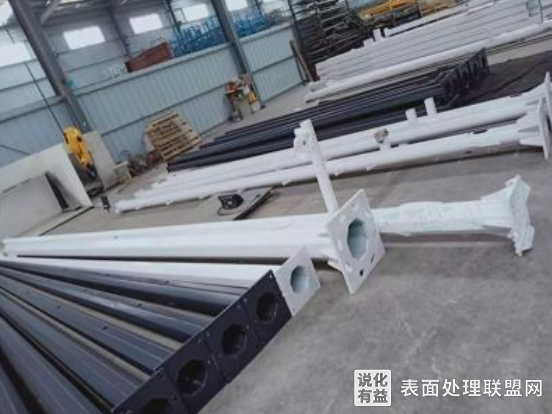
考虑到磷化处理应用的范围较广泛,这里我们来具体了解一下它们的工艺原理。
1、传统磷化
传统磷化处理是将钢铁零件在含有锌、锰、钙铁或碱金属磷酸盐溶液中进行化学处理,在其表面形成一层不溶于水的磷酸盐膜的过程。而这种处理工艺中多含有锌、镍、锰等有害重金属,并且如果想要磷化效果好,就需要较高的处理温度,温度控制不当,磷化效果也不理想,并且因此产生废水、废渣处理起来比较复杂。
传统磷化的处理工程可分为四步:
①当金属浸入磷化液中时,先与磷化液中的磷酸作用,生成一代磷酸铁,并有大量的H2析出。其化学反应为:Fe+2H3PO4=Fe(H2PO4)2+H2↑,表明磷化开始时,仅有金属的溶解,而无膜生成。
②在实际处理过程中,微阴极部分反应生成H2而引起的极化使得磷化反应速度渐趋缓慢。为了在一合适的时间内完成磷化膜的形成,必须采取一些加速促进措施,较为普遍采用的是添加氧化型化学促进剂,其作用除了促进磷化膜的形成和控制溶液的铁含量外,还可与初生态氢迅速发生反应,减少工件氢脆现象的发生。目前使用较多、效果较好的是亚硝酸钠,由于其不仅具有氧化性,还具有还原性,在空气中易被氧化失去效用,因此必须在生产中不断添加。其化学反应式为:3Zn(H2PO4)2+Fe+2NaNO2=Zn3(PO4)2+2FePO4+N2↑+2NaH2PO4+4H2O。由于促进剂添加时会产生沉淀,所以需要缓慢滴加。
③由于金属工件表面的氢离子浓度急剧下降,pH上升,导致离解平衡向右移动,最终产生磷酸根。磷化槽液中基本成分是一种或多种重金属的酸式磷酸盐,其分子式Me(H2PO4)2,这些酸式磷酸盐溶于水,在一定浓度及pH下发生水解反应,产生游离磷酸。
④上述磷酸根和槽液里的锌离子、铁离子反应生成沉淀。因此一般磷化膜中存在两种不同成分:Zn3(PO4)2·4H2O (磷锌矿)和Zn2Fe(PO4)2·4H2O (磷叶石),另外还有Mn2Zn(PO4)2·4H2O和Ni3(PO4)2·8H2O。
当处理铁和钢时,一部分从基材上溶解下来的铁与涂层结合生成了磷酸锌铁,它(磷叶石)具有优良的附着力和抗腐性能。此种磷酸锌铁盐组成了部分转化膜,磷酸锌转化膜的其余部分为纯磷酸锌。磷酸锌转化膜中磷酸锌铁所占比例随所用的工艺不同而不同,在喷淋工艺中为50% ~ 75%,而在浸渍工艺中可得到100%磷酸锌铁。
金属工件溶解出的二价铁离子一部分作为磷化膜的组成部分被消耗掉,而残留在磷化槽液中的二价铁离子,则氧化成三价铁离子,并成渣。不同的配方,生成的渣量有较大的差异。通常,高锌磷化液的产渣量较大,可达7 ~ 10 g/m2,一般低锌磷化的渣在3 g/m2 左右,膜在2 ~ 3 g/m2。所以磷化有渣是正常的,关键看产品的选择及是否有正确的设备保养以避免产生过多的渣,比如泵的能力是否足够。磷化渣的多少直接影响到设备的投资与维护。
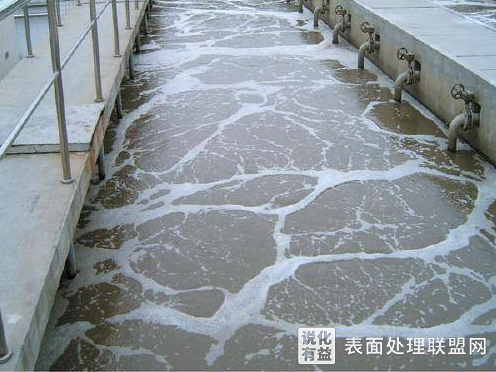
2、过渡磷化
对于传统的磷化工艺,铝件的增多会导致磷化渣大量增加,同时铝渣相对于镀锌钢板的磷化渣来说更难去除,并且在磷化反应中产生的铝离子过多不能及时去除的话,会导致磷化槽液中毒,抑制所有板材表面的晶粒生长,磷化膜发黑,并且造成结合力下降。一般来讲,对于混线生产的生产线来说,如果使用传统磷化,铝件占比不能大于20%,然而随着当代汽车等行业的轻量化发展,铝合金板材的应用只会越来越多,因此传统磷化技术不得不做出些许变革和升级,通过使用添加剂,降低铝板在磷化中成膜,很好地配合了铝件的应用。
3、薄膜前处理:薄膜前处理常被提及的有硅烷薄膜前处理和锆系薄膜处理
3.1、硅烷薄膜前处理
通过研究发现,硅烷可以有效地用于金属或合金的防腐,并且能在室温下与镀锌钢、冷轧钢、铝板等多种金属基材表面发生反应,硅烷在水溶液中通常以水解的形式存在:—Si(OR)3+3H2O→Si(OH)3+3ROH。
锆系薄膜前处理工艺的原理可以这样理解:硅烷水解后通过其SiOH基团与金属表面的MeOH基团的缩水反应而快速吸附于金属表面。一方面硅烷在金属界面上形成Si—O—Me共价键。一般来说,共价键间的作用力可达700 kJ/mol,硅烷与金属之间的结合是非常牢固的;另一方面,剩余的硅烷分子通过SiOH基团之间的缩聚反应在金属表面形成具有Si—O—Si三维网状结构的硅烷膜。该硅烷膜在烘干过程中和后续的电泳漆或喷粉通过交联反应结合在一起,形成牢固的化学键。从而基材、硅烷和油漆之间可以通过化学键形成稳固的膜层结构。
3.2、锆系薄膜前处理工艺的成膜原理是,在基材表面形成原电池,金属底材作为原电池的阳极,金属溶解,氧化锆和其他成分作为原电池阴极,沉积在金属表面形成非常致密的锆系膜,为金属表面提供良好的抗腐蚀能力。
传统磷化和过渡磷化都有着相同的缺点,那就是加工时会产生大量的废水和废渣,给生产企业造成治污、排污的困扰,工厂需要投资大量的资源进行废水废渣处理,而薄膜前处理工艺的优点就显而易见了,就是环保,并且成本低,产品消耗量低,“三废”处理成本低。那薄膜前处理如此完美吗?并不是,薄膜前处理也有缺点,可以总结为以下几点:
① 对脱脂要求高,必须选择高效环保的脱脂工艺以达到优异的脱脂效果;
② 处理后的电泳泳透力要比磷化工艺的电泳泳透力有所下降,所以在使用硅烷前处理工艺时需要选择与之配套的电泳工艺参数;
③ 对底材的表面状态要求较高,因为膜层非常薄,很难遮盖底材的缺陷。
其实这是可以理解的,传统的磷化工艺可以说已经比较成熟了,任何新生的技术都有缺点,知而战之,这不是我们国人的优良传统吗?直面挑战,才能战胜它,随着薄膜前处理技术的不断成熟和人们对环保意识的不断提升,薄膜前处理技术亦能克服当前的缺陷,亦能成为主流技术之一,同理,磷化技术也在想绿色环保理念出发,终能攻克污染问题。