众所周知铝合金与大气接触会在其表面自然形成的氧化膜,它会使金属表面失去原有的光泽,未解决这一困扰,我们会对铝合金进行阳极氧化处理,在铝合金表面形成一层比自然氧化膜厚得多的致密膜层,厚度一般为3-15微米,然后再经过封闭处理,无晶型的氧化膜转变成结晶型的氧化膜,孔隙也被封闭,因此使金属表面光泽能长久不变。所以铝合金件进行阳极氧化非常有必要。
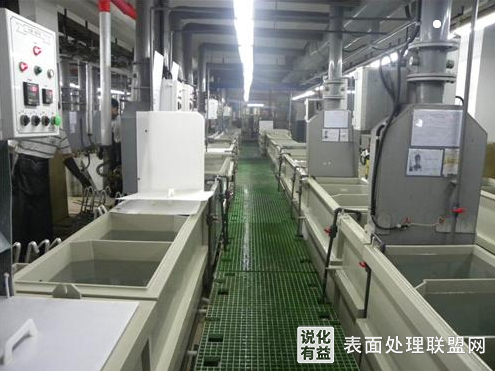
进行阳极氧化时的电解溶液多为硫酸、草酸、酪酸,其中,硫酸应用最为广泛,这主要是因为硫酸阳极氧化操作方便,电解液稳定,成本不高,且工艺成熟,并且生成的氧化涂层具有高吸附能力,易于密封和着色,耐腐蚀,明显美化外观等优点。但是即便是如此成熟的工艺,在实际生产运用中也会出现一些缺陷。
1、譬如铝合金在进行硫酸阳极氧化时,可能会出现部分未氧化的膜,体现在会有明显的黑点和条纹,或者氧化膜会出现鼓包的情况。这类现象可以考虑是铝和铝合金的组成、结构和相位均匀性问题。纯铝或铝镁合金更容易形成氧化物涂层,而且涂层的质量也很好。对于铝硅合金或含铜量高的铝合金,氧化膜更难形成,所形成的涂层是深色、灰色和低光泽的。如果表面由于金属相的异质性、结构的偏析、微观杂质的偏析或不适当的热处理而在每个部件中产生异质性结构,那么选择性氧化或选择性溶解就比较容易产生。如果铝合金的局部硅含量是孤立的,往往是局部没有氧化膜,或产生条纹状的黑点,或因局部选择性溶解而产生孔。电解液中悬浮的杂质、灰尘和铜、铁等金属杂质离子过多,也会使氧化膜上出现黑点或黑条,影响氧化膜的防腐蚀性能。
对于铝硅合金或含铜量高的铝合金,在进行阳极处理时,还是选择硫酸阳极氧化,只是需要研究清楚电解液浓度,电流密度,氧化时间和氧化温度对铝硅合金氧化膜厚度及电化学行为的影响,选择对症下药的阳极氧化工艺。
2、在阳极氧化处理中,可能会出现同一槽中的零件没有生成氧化膜或者氧化膜很薄或不完整,抑或是在夹具和零件的接触区有烧焦和腐蚀的现象。这种情况通常发生在阳极氧化工艺的过程中,这类情况会严重影响铝合金阳极氧化的质量。而出现这种现象的主要是因为主要是由于夹具和工件之间的接触不良,导电性差或夹具上的氧化膜没有完全去除的缘故。
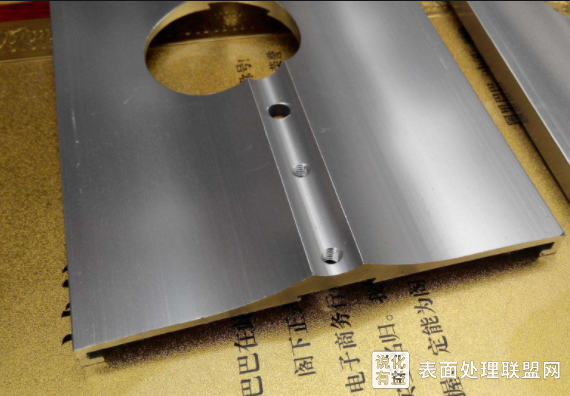
铝合金部件在阳极氧化前必须牢固地安装在一般或特殊的固定装置中,以确保良好的导电性。导电棒应该由铜或铜合金材料制成,以确保有足够的接触面积。夹具和部件之间的接触痕迹必须保持在最低限度,并允许电流自由流动。如果接触面积太小,电流密度太高,零件或夹具就有可能过热而烧毁。
3、铝合金硫酸阳极氧化后,特别是填充和密封后,用手触摸时,氧化膜松动,变成粉末,并进一步剥落,部件表面露出严重的粉末层,耐腐蚀性差。这种类型的故障主要发生在夏季,特别是在没有冷却系统的硫酸阳极氧化槽。在一个或两个罐体部件被处理后,会出现松散的粉末,这显然会影响氧化涂层的质量。出现这种情况是因为铝合金阳极氧化层的高电阻,在阳极氧化过程中会产生大量的焦耳热。电池电压越高,产生的热量就越大,电解质的温度也不断上升,从而导致氧化膜脱落。
因此,阳极氧化工艺必须要求使用搅拌或冷却装置,以保持电解质温度在特定范围内。在正常情况下,温度应控制在13至26℃之间,以提高氧化膜的质量。如果电解液温度超过30℃,氧化膜就会开始会松动,甚至变成粉状,严重时还会造成 "烧痕"。
4、硫酸阳极氧化后的铝合金的氧化膜可能会变得暗淡无光,并可能出现点状腐蚀。严重的甚至会出现非常明显的黑点,最终造成零件报废。这种相对比较严重的缺陷往往是偶然的。在铝合金的阳极氧化过程中,由于断电后重启,导致被切断的部分又长期停留在清洗槽中,所以清洗槽的酸性太强,水质不干净,含有悬浮物,所以氧化膜往往是暗淡无光。 泥沙经常增加,造成铝合金部件的电化学腐蚀和点状腐蚀的黑点。自来水可能被添加到电解液中,它可能被漂白剂处理过,Cl-含量可能超过标准,或者装有氯化氢的容器可能没有被彻底清洗,可能含有硫酸。 这导致多余的Cl-与阳极电解质混合。由此产生的铝合金部件的阳极氧化导致点状腐蚀,最终导致产品报废。
这种偶然的情况出现的几率可以说是很小的,这类情况就像是自然灾害一样,并没有特别有效的防范方法,除了规范工人的操作意识,还需要做好日常的机器检查维护工作,尽量确保不会出现无故断电的情况。
声明:说化有益·表面处理联盟网专业视角栏目旨在免费为同行提供知识共享和储存,所有文章均由业内专业人士发布(包括转帖),文末都会标注作者,版权归作者所有。文章仅代表作者本人的观点,本站不保证文章等内容的有效性。
知识互通,携手共进,我们欢迎各方(自)媒体,机构转载,引用我们原创内容,但需严格注明来源。同时,我们也倡导尊重与保护知识产权,如发现文章内容涉及侵权,请通过在线咨询进行投诉,我们会在第一时间核实处理。