相关文档推荐
-
12.6分 | 13481阅读 | 14人下载
-
21.0分 | 4928阅读 | 4人下载
-
30.6分 | 9648阅读 | 2人下载
-
42.7分 | 7334阅读 | 9人下载
-
52.9分 | 7214阅读 | 10人下载
-
61.0分 | 6875阅读 | 11人下载
-
70.7分 | 6068阅读 | 0人下载
-
81.2分 | 6033阅读 | 8人下载
-
91.1分 | 5922阅读 | 4人下载
-
101.2分 | 5307阅读 | 8人下载
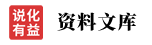
免费下载


点赞 0

收藏 0

分享
微信扫一扫分享给朋友
磷化工艺在工业上的应用
无论以消耗前处理和磷化化学药品的数量还是以处理钢材的吨位计算,磷化膜的最大用途是作为现代涂装底层。此外,磷化膜还广泛用于以下方面:
(1) 作为油或其他防蚀材料的底层。·
(2) 作为零件在有油或无油存在下接触面摩擦运动的润滑层,防止零件磨损和擦伤。
(3) 与拉延润滑剂结合用作冷变形加工的润滑层。
(4) 暂时的或短期的防锈。
(5) 作为塑料或橡胶与金属粘结的底层。
涂装前的磷化处理
磷化膜提高涂装涂层抗蚀性能的作用
很久以前,人们便发现磷化膜能提高钢铁类金属的防护性能。不过,如果不加后处理,磷化膜的防护性能是有限的。因此,通常金属表面经磷化处理后,还需根据实际使用情况进行钝化处理、涂油或涂漆以满足防蚀的要求。 任何涂漆金属制品的使用寿命主要决定于涂料层本身的耐久性能和漆膜与制品表面的附着性能。漆膜的主要作用是防止基体金属在其使用环境内发生腐蚀。 为了达到这个目标,制备金属表面处理的方法应能降低金属表面的活性,从而防止在漆膜与金属界面的膜下腐蚀。
磷化膜用作涂装底层可提高漆膜的附着性能,提高漆膜的耐潮湿和耐浸水性能,可以基本上阻止可能发生的腐蚀扩散。金属表面的金属或非金属覆膜损坏了之后,便会暴露出基体金属。由于基体金属的导电性和覆膜与基体之间的毛细管作用,在覆膜损坏的地方便构成微电池,基体便从这里开始腐蚀并向四面八方扩散出去。覆膜与基体之间的毛细管吸引电解液至覆膜下面,由此产生的膜下腐蚀导致覆膜起泡。金属表面磷化处理后,腐蚀过程便会被限制在覆膜损坏的地方,因为金属基体的其余部分为非导体的磷化膜所绝缘。磷化膜还与基体金属牢固地粘结在一起,因而可以防止电解液向水平方向扩散,从而抑制了膜下腐蚀。 涂装预处理中最基本的问题是磷化膜必须与底漆有良好的配套性,而磷化膜本身的防锈性是次要的。这一点是许多磷化液使用厂家最容易忽略的问题。在生产实践中,往往碰到厂家对磷化膜的性能要求不科学,片面要求磷化膜的防腐性能,他们要求越高越好,而对与漆膜配套性几乎不关心。涂装预处理中,磷化膜的主要功能在于作为金属基体和涂料(油漆)之间的中间介质,它提供了一个良好的吸附界面,将涂料(油漆)牢牢地覆盖在金属表面,同时细腻、光滑的磷化膜能提供5μm以上且防腐性能很好时,将这样的膜层送去作电泳漆,这会使我们几乎不能得到电泳漆膜。而磷化膜的防锈性能,只是提供一个工序间的防锈作用。另外,粗厚磷化膜会对漆膜的综合性能产生负效应。因此磷化体系与工艺的选定主要由工件材质、油锈程度、几何形状、磷化与油漆的时间间隔、磷化与涂装(油漆)层的配套性、底涂品种等条件决定。
一般情况下,对于有锈工件必须经过酸洗工序,而酸洗后的工件将给磷化带来诸多的麻烦。例如,工序间生锈泛黄、残留酸液的清洗、磷化膜出现粗化等。酸洗后的工件在进行锌系、锌锰系磷化前要进行表面调整处理。如果工件磷化后没有及时涂漆,那么当存放期超过10天以上,应采用中温磷化,磷化膜质量最好在1-5g/m2-5g/m2之间,此类磷化膜本身才具有较好的防锈性。磷化后的工件应立即烘干或用热水烫干,如果是自然晾干,易在夹缝、焊接处形成锈蚀。
在某些情况下,磷化后涂漆所得的复合膜的防护性能比金属覆膜的防腐性能还好。
漆前磷化工艺的发展概况
防腐蚀磷化所用的磷化液在1914年一1939年间有了较大的发展。( 在这一阶段,涂料涂装工业还未发展到目前的水平,磷化膜上的油漆涂层的防蚀效果十分依赖于磷化膜的质量。因此,在第二次世界大战期间主要努力于生产厚的磷化膜,使得金属与腐蚀环境尽可能地完全绝缘,如生成磷酸锰磷化膜的磷化工艺(称为Parkcrization工艺)。
1932年,出现薄膜防蚀磷化处理工艺(称为Bonderite工艺),标志着当时有关磷化观点的转变。从Bonderite这个词可知,注意力在于防护膜与基体粘结的因素,确定研究方向在于使磷化膜对金属具有最大的结合力,而且对漆膜也有很好的结合力。
除了工艺方法上的改进(如采用喷液方法磷化)以外,对于磷化液的研究则致力于生成既能满足与漆膜结合的要求又尽可能厚的磷化膜,使复合膜具有最大的防蚀性能。然而,发现这两个要求是互相矛盾的,即要得到与漆膜结合良好的性能就要求磷化膜薄,而要得到磷化膜良好的防护性能则要求磷化膜厚。
磷化膜是由脆性的结晶组成的,因此经过磷化的零件的任何大小变形都有可能使使之损坏,这对涂漆的零件更为有害。因为松脱的磷酸盐结晶会刺破漆膜而暴露出基体金属,这些漆膜与磷化膜脱落的地方会立即锈蚀。降低磷化膜的厚度可以提高磷化膜适应机械变形的能力。所以薄的磷化膜(1-5μm)最适用作油漆的底层。磷化膜越薄,涂在磷化膜上的漆膜的抗机械变形性能越高。-
事实上,经过不断的改进,现在已经可以采用最薄的磷化膜作油漆底层,而且对基体金属的防护性能即使在最坏的条件下仍然非常好。这种成就应归功于两方面的改进,即磷化的化学成分和结晶结构的改进,以及漆膜质量的不断改进。在这种情况下,倾向于采用一代磷酸钠之类的碱金属磷酸盐处理钢,这种方法又称为转化型磷化(生成无定形磷化膜)。这种方法得到的磷化膜含有氧化铁和磷酸铁,具有良好的防蚀性能,而且由于单位膜重轻(0 .5g/m2 --- 1 g/m2)大大改善了漆膜的粘结强度。不过,近几十年来,结晶磷化也得到不断的改进,现在已经可以获得极均匀的厚度为l- l .2μm(1. 5g/m2-2g/m2)的磷化膜。
20世纪70年代初期,美国发展了一种钢带连续涂漆技术。钢带先磷化后涂漆,所得复合膜可经受非常苛刻的冷变形加工而不脱落。用含有磷酸锌、磷酸镍和氟活化剂,并以硝酸根亚硝酸根作加速剂的磷化液磷化钢、铝和镀锌钢可以得到令人十分满意的磷化膜,只要磷化7s-10s,膜重便可达到1g/m2一3g/m2。证明结晶磷化工艺现在的适应性可以广泛满足各种不同工艺的要求。这种膜的性能很值得注意,即使涂漆的钢板变形了,这种膜仍然保持着有效的防烛性能。
漆前磷化工艺
漆前磷化工艺可分为两类: (1)结晶磷化,生成重金属磷酸盐结晶的磷化膜,通常为锌,锌/钙或锌、锰磷化。 (2)无定形磷化,以碱金属磷酸盐为主组成磷化液,生成含有氧化铁和磷酸铁的无定形磷化膜。用作油漆底层的磷化膜的膜重通常在0 . 2g/m2 --- 2.5g/m2范围内。一般地说,膜越重抗蚀性能越好,但其他性能,如漆膜的光泽和附着力则在上述膜重范围较轻的膜最好。锌磷化用于在腐蚀性较强的环境使用和在户外使用的制品上,如汽车车身、拖拉机机身板、洗衣机机壳等。无定形磷化用于腐蚀性不太强的环境使用和在户内使用的制品上,如钢制家俱、冷冻机机壳、荧光灯灯架等。
漆前锌系磷化液一般为以亚硝酸钠或氯酸钠加速的含有磷酸锌和硝酸盐的酸性溶液,通常还加有细化剂以期得到结晶细致密和附着力好的磷化膜,最常使用的细化剂是柠檬酸和酒石酸。有时还加有氟化物以改善磷化膜的均匀性,并使磷化液能用于由多种金属组成的部件的磷化。当对磷化膜或磷化液有特殊要求时,还可加人其他重金属,如镍、锰和钙等。磷化液中还可加人某些有机添加剂,使在加热器上形成的垢及沉渣软化便于除去。用这样的磷化液,通常在40℃一60℃喷液磷化,磷化时间为60s-90s,得到浅灰色结晶磷化膜,膜重一般为1.5g/m2一 3.5g/m2。现在采用的电泳涂漆技术要求磷化膜重最好在1.g/m2一2g/m2范围内,以期漆膜获得更好的粘结性能和抗碎石冲击性能。
锌系磷化液用锰盐改性可在较低温(25℃-35’C)下进行磷化,得到膜重约 2g/m2的磷化膜。 用于喷液磷化组成相似的磷化液,也可采用浸液法磷化。通常磷化温度为 30℃一50℃,磷化时间一般为2一5min。 经过改进的浸液法也可在低温(25℃一35℃)下进行磷化,生成膜重约为 2g/m2的磷化膜。 在浸液磷化的锌系磷化液中加入钙,可使零件经碱洗或酸洗后不经细化预处理也能获得细结晶的磷化膜,特别适合于作为涂漆的底层。
无定形磷化是用碱金属一代磷酸盐(一般为 钠或铵盐)处理钢铁零件,生成的磷化膜含有氧化铁和磷酸铁。这种溶液不加特殊的加速剂也可以磷化,不过这种溶液含有亚硝酸盐,钼酸盐,溴酸盐和氯酸盐等加速剂,也可以含有氟化物以适应由多种金属构成的组件磷化。这种溶液通常在30 -60℃磷化,用喷液法磷化约需lmin- 2min,得到的磷化膜膜重为0.4g/m2一 0 .7g /m2,与漆膜有良好的结合性能,有较好的抗蚀性能,但比锌磷化膜差一些。 在无定形磷化液中加入恰当的表面活性剂可使脱脂和磷化两个工序在同一溶液中同时进行。
零件经漆前磷化后还要进行水洗和后处理以提高抗蚀性能。后处理通常采用含有六价铬或含有六价铬和三价铬的溶液处理。随着阴极电泳涂漆技术的发展,已发现用只含三价铬的溶液作后处理很有好处,特别可以提高漆膜的附着力性能。
用作阴极电泳涂漆漆膜底层的磷化膜应具有下述特性
磷化膜必须均匀,只有均匀的磷化膜才有良好的抗蚀性能、良好的漆膜附着力和平滑的阴极涂漆漆膜。
磷化膜的结晶必须细并与基体牢固结合,只有这样的磷化膜才能使漆膜粘结牢固并有良好的抗碎石冲击性能。
P/(P+H)值要高,这也是要获得良好的抗蚀性能和附着力性能所必需的。P/(P十H)值代表锌磷化膜的组成,一般要求P比值大于等于85%。
膜重最好控制在1. 4g/m2 – 2.2g/m’范围内,这样漆膜可获得最佳的附着力性能。
表面没有锈和氧化皮的零件的电泳漆前磷化工艺程序一般如下:
脱脂、除去金属表面的油脂,保证金属表面在以后的步骤中能被处理液完全润湿。
冷流水清洗。
热水清洗。目的有二:除去脏物和预热零件以增加金属表面在磷化液中的初始活性。
表面调整。
磷化处理。
冷流水冲洗。
钝化后处理。
去离子水清洗。
电泳涂漆。
磷化有锈或氧化皮的零件时,需在脱脂水洗工序与磷化工序之间增加下述工序:
用适当的酸溶液或碱溶液(用于铝及其合金)清洗。
冷流水清洗。
细化结晶预处理。例如,用胶体钛盐溶液预处理。
上述工艺程序可用于喷液法和浸液法。汽车车身磷化处理还可以用喷浸结合的方法。
铝制品如果不采用阳极氧化或钝化处理,通常也用锌磷化处理。 磷化电镀镀锌钢或热渗镀锌钢,用含有锌和镍的磷化液处理时,可选用简单的或络合的氟化物作催化剂。
低温磷化工艺
近代大量生产的漆前磷化线趋向于采用低温磷化。现在已经有可在24℃浸或喷液磷化的无定形磷化液,生成膜重为0.44g/m2一0.66g/m2的磷化膜。锌磷化液已经能在38℃生成3.3g/m2一5.5g/m2膜重的磷化膜。用于电泳涂漆前磷化的锌磷化液已经能在25℃一35℃生成1.4g/m2一2.2g/m2膜重的磷化膜。 低温磷化可以大大降低能量消耗,还可节约加热系统的投资。
改用在24℃磷化工艺,除了需要供给泵的能量外不需要热量。两种工艺生成磷化膜的膜重均为0.44g/m2-0.5g/m2 。 虽然浸液磷化比喷液磷化热损失小得多,但是采用低温磷化也还是可以节约能量的。一般磷化温度在60℃以上时,热损失迅速增加。
防锈磷化(工序间或贮存零件防锈)
工序间或贮存零件的防锈磷化,通常要求用厚的磷化膜以求得到良好的防蚀性能。零件经磷化处理后还要浸油、脂或蜡以提高防蚀性能。 英国标准3189把在钢铁表面生成膜重大于7.5g/m2的铁、锰或锌磷化膜称为厚磷化膜。实际上,通常膜重在10g/m2--20g/m2范围内。在某些条件下,膜重常达40g/m2。防锈磷化可采用铁、锰或锌盐磷化。一般工艺程序为
脱脂;
水洗;
磷化(浸液法);
水洗;
后处理;
干燥;
封闭处理,浸于特殊的封闭液中处理。
防锈磷化处理工艺的选择由许多因素决定,如产品的类型、清洗的方法、设备情况及处理时间等。
市场上出售的封闭处理剂品种繁多,如脱水液与油,油在水中的乳化液,矿物油,蜡(使用前溶于石油溶剂)和水基石蜡等。如用脱水液与油处理剂或油在水中乳化液作封闭处理,零件可不经干燥便进行封闭处理。
冷变形加工前磷化的作用
磷化膜对冷变形加工的作用
磷化膜对钢冷变形加工的重要作用是F. Sinzer发现的。直到1945年,冷变形加工前磷化工艺主要用于武器制造方面,后来这种工艺才在各个领域飞速发展,应用厂家遍及金属与工具接触在压力和低温下塑性变形加工各方面。
冷变形加工涉及金属在各种工具(如拔丝模、冲头和冲模)之间的压力塑性变形问题。在这样的加工作业中,金属与模具的表面应力很高,显然接触表面之间的摩擦特性很重要,良好的润滑在变形加工过程中起重要的作用。与金属表面牢固结合的磷化膜加上矿物油或植物油之类的辅助润滑剂可以很好地解决金属表面与模具之间的摩擦问题。磷化膜晶间区的毛细管作用有利于润滑剂浸透磷化膜。后来又发现用皂基润滑剂代替润滑油效果更好。
把磷化处理过的钢毛坯浸于温热的,pH值为8一10的皂液中,当磷化膜为三代磷酸锌时会发生复分解生成锌皂、主代磷酸钠、三代磷酸钾或烷烃胺等。 使用这类润滑剂不仅金属变形加工更容易,而且大大降低了工具的磨损。 浸了润滑剂的磷化膜应视作可以移动于工具和金属表面的膜。因此,每通过一次加工,润滑膜就会损失一部分。许多研究工作者曾用放射性示踪方法研究金属变形加工过程中这种膜的损失情况,发现金属拉伸增长38%、润滑膜大概损失原有膜重的11%。德国研究工作者A. Durer的报告损失大一些,约为20%一50%。
虽然冷变形加工和热变形加工大不相同,但是不能忽视冷变形加工施加于金属的极高的应力能使金属温度上升到200℃左右。在这样的条件下,磷化膜就会脱水。例如,含四个分子水的锌磷化膜会损失两个分子水。M : Gebhardt认为这样的磷化膜便会出现劈裂平面,有助于晶体颗粒在表面滑动过程转移。
工业上用的冷变形加工钢和铝的磷化膜是以磷酸锌为主的,再浸硬脂酸锌,磷化膜的膜重为5g/m2-25g/m2,锌皂量为l00g/m2一150mg/m2。有时因为润滑皂 (如硬脂酸钠)过多而使总膜重增加,这样会使工具堵塞,如高生产率的拔丝加工有时会发生这种情况。如果出现这种情况,建议加完润滑剂后用水冲洗以除去过多的皂,水洗对不溶解的锌皂无影响。
磷化处理在拔管工业的应用
在长的或短的芯棒上拔管或空心拔管都涉及金属内外表面不同程度的变形。 在磷化工艺出现之前,管子毛坯经酸洗清洗后便浸于热的皂液或乳化润滑剂中处理,然后进行冷拔管,使管子横截面减少25%一30%左右。冷拔管子会使金属硬化,因此在进一步冷拔之前需要退火,然后再次进行酸洗、润滑剂等处理。自从采用了磷化处理工艺后便发现毛坯可以连续冷拔两次或三次而不需要退火处理。
磷化处理对冷拔管工业的好处有下列几点:
可以减少摩擦力,减少动力消耗,提高冷拔速度,速度范围为30m/rrin – 100m/min,平均速度为50m/min – 60m/min。冷拔无缝钢管时,每次冷拔可减缩截面尺寸40%左右。
不经退火可进行多次冷拔,这样便可以减少零件在工序间的来回传送次数,减少中间退火、酸洗、浸润滑剂等工序的次数,提高生产效率。
减少工具的磨损。
降低了管子表面的粗糙度,大大减少了由于焊合和擦伤造成的废品。
上述各点大大地提高了拔管工业的生产效率,显著降低了成本,给拔管工业带来了很大的经济效益。
冷拔管磷化处理的典型工艺如下:
毛坯用热硫酸或室温的盐酸酸洗。这道工序很重要,其目的是彻底除去退火处理时生成的氧化物或氧化皮,并使金属表面活化与磷化膜结合得更牢固。
冷流水清洗。
二次冷流水清洗,含有中和盐更好。
锌磷化(浸液法)。
冷流水清洗。
热水清洗,含有中和盐更好。
活性润滑剂处理。
干燥。
毛坯管束最好倾斜地进人槽液,待完全浸人后把管子的倾斜方向反过来,这样可以很快排出管子内面的空气,使管子内表面得到圆满的处理。管子外表面的完全润湿是靠槽底的摇架使管束松开来达到的。
关于上述的工艺程序,还必须作一些补充说明。 酸洗时由管子的表面状态、酸洗槽液的缓蚀程度、酸洗槽液被铁离子污染的程度等因素而定。对焊接管和要求得到“光亮管”的毛坯酸洗时间要短些。第((3)步 和第(6)步有时可在同一个槽内进行。 还必须强调,浸润滑剂前的第(6)步中和处理是很重要的。因为从磷化液出来的管子ph值为2---2.5,不能直接浸人pH值为9的润滑剂槽中,否则,碱性皂和磷化膜的反应就会受到影响,从而降低润滑效果。有时第(5)步清洗可以把毛坯送回第(3)步进行处理,但是在这种情况,第(6) 步的碱中和处理就是必不可少的了。浸润滑剂的时间以刚好能形成锌皂为宜,如,4min – 6min。浸渍时间太长会导致磷化膜被破坏。磷化膜与润滑剂反应,以及可能机械带入的杂质会污染润滑剂槽液,主要污染杂质为氢氧化铁,可由它本身的深棕色及润滑性能的丧失而看出来。把润滑剂槽液连续离心除去杂质可以延长槽液的使用寿命,保持满意的润滑性能,这是美国广泛使用的方法。
干燥过程必须把皂基润滑剂表面层的结合水全部去掉,通常使用热风吹入倾斜的室内使之干燥。
拔管工业使用的磷化液,长期使用氯酸盐作加速剂,最好和硝酸盐一起使用以得到膜重为5g/m2一l0g/m2的磷化膜。但是这类磷化液有时会严重腐蚀金属,因而不可能经常获得光亮的成品。
汽车减震器用的无缝钢管的表面粗糙度要求为5μm – 15μm (0.1μm -0.4μm) 。正是在这方面出现了大大改进了的磷化液。这些磷化液包括以磷酸锌,磷酸钙为基础,用硝酸盐/亚硝酸盐加速,并含有多磷酸盐作为细化剂的磷酸锌溶液。在这一特殊情况,总是希望能得到膜重为4g/m2一8g/m2,与金属牢固结合的磷化膜,而且金属的晶格又不为酸深度腐蚀。
过去普遍使用磷酸锌槽液,单独用硝酸盐加速,在含有铁的情况下磷化,近来明显地倾向于使用硝酸盐/亚硝酸盐加速的磷化液。这种溶液能自动催化再生亚硝酸根离子,因而溶液中不存在亚铁离子。这种系统的磷化液如果小心控制总酸度,可以得到非常好的结果。这种不含亚铁离子的磷化液的最大优点是,材料消耗少、沉渣少,因而与用氯酸盐加速的磷化液相比,可使用较长的时间才需要消除沉渣。
对于无缝钢管来说,所用磷化液生成的磷化膜只有几微米厚已足以冷拔一两次了。化学品消耗从60g/m2一70g/m2降到30g/m2一40g/m2 。焊接管也常用含有细化剂的磷化液处理,这样膜重可减至2g /m2。
磷化处理在拔丝工业的应用
正如拔管工业那样,拔丝工业也很快便认识到磷化对提高拔丝机的效率和改善产品质量有很大的益处。虽然过去冷拔低碳钢用粉状硬脂酸盐干润滑剂是没有什么困难的,但冷拔硬钢和冷镦大直径线材就需要借助于磷化处理了。
典型的工艺程序如下:
用盐酸或硫酸酸洗。
用冷流水清洗,可能的话最好用喷液法清洗。 一次冷流水清洗,用温水更好。
磷酸锌盐磷化处理。
冷流水清洗、用喷液法或洒水器冲洗更好。
用润滑剂槽液或用含有硼砂或石灰的悬浮液作后处理。
干燥。
金属线材可以成捆处理,也可以把线材拉开连续通过各种槽液进行处理,最后重绕成捆,还可以采用Helicof i1方法让线材沿卧式圆筒做螺旋运动连续磷化。采用连续磷化技术,通常只磷化20s-60s。这样短的磷化时间,要得到满意的结果, 必须提高总酸度到80点或120点。处理成捆的线材要求浸液磷化5-10min, 还要注意定期分开各圈以保证均匀处理。
有些处理粗冷镦线材的连续生产线只用研磨或喷砂的方法作表面处理,然后用热水喷淋冲洗和磷化几十秒钟。磷化液总酸度达到60点。 连续磷化完全有可能在20s-40s内得到4g/m2一6g/m2膜重的磷化膜。传统的线材成捆浸液磷化所得磷化膜的膜重通常为5g/m2一l0g /m2。 线材拔丝前磷化也长期使用以氯酸盐或氯酸盐与硝酸盐作加速剂的磷化液。这种磷化液虽然操作简单,但化学药品消耗量大,同时生成大量的沉渣,所以后来只采用以硝酸盐作加速剂的磷化液。但是,这样又因磷化膜中含有磷酸铁,所以拔丝模很快便损坏了。
过去几年有采用自动再生NO2-以N03- ,NO2-离子对作加速剂的磷化液的趋势。调整操作条件可以使磷化膜膜重在5g/m2一15g/m2范围内,而用氯酸盐作加速剂的磷化液所得磷化膜膜重为4g/m2一8g/m2。这种磷化液还有下述优点、 ①化学材料消耗少;②形成沉淀少;③工具磨损较少;④磷化膜质量稳定;⑤由于不含氯离子,防锈性能更好些。
磷化后拔丝,线材截面可在连续拔8次一16次后缩小至原来的10%以下,拔丝速度可达1000m/min,由此可见磷化处理可给拔丝工业带很大的经济效益。 与线材处理有关的冷镦螺栓滚压加工等方面发展得很快,磷化处理在这方面可能会由于使用合金含量更高的合金钢材料而使磷化成膜困难。 用于这方面的磷化膜必须能经受相当大的变形,而且在送到冷镦机之前还会受到最后的校形处理。所以在校形之前磷化膜必须是高强度的,而且膜重应达到 20g/m2- 30g/m2。目前使用的含有促进磷酸锌生长的催化剂的磷化液获得一定的成功。这样的磷化液可以处理含碳0.15% -0.35%(有时达到1%),铬0.5%一 1.5%,锰、钼、镍0.6%一1.2%的钢。
磷化处理在冷挤压加工方面的应用-
冷挤压加工涉及用高达4000t – 6000t的压力使金属塑性变形的问题。磷化使钢冷挤压加工成为可能。如果考虑到这种工艺迅速发展的情况,便可以认识到这不是一件小事。A. A. Dykiel对冷挤压工艺所作的经济分析表明,1950年美国用这种工艺生产的产品是很少的,但到1965年便达到了320000t。联邦德国则从1950年的2000t增加到1965年的180000t。美国市场1970年一1980年间达 1000000t.
在第二次世界大战时,冷挤压技术主要是在德国发展起来的,直到1947年这种技术才出现在法国,尤其是美国花了很大的投资使这种技术大规模地发展起来。 由于冶金工业的普遍进步和工具设计的改进,包括使用高速钢和碳化钨制成的冲头和模具,挤压机的生产效率不断地提高。不过,尽管如此,如果没有磷化工艺的作用,在高达150kgf /rnm2 --- 200 kgf /rnm2 (1500Mpa.- 2000Mpa)压力下,金属流动的问题仍然是难以应付的。现在冷挤压工艺已经能够应用于软钢、超软钢、碳钢、合金钢等材料的挤压加工上。
挤压小零件时,使用从钢棒上切下来的、直径准确的钢坯。钢坯在冷挤压前先用碱性清洗液除去上一道工序带来的磷酸盐和润滑剂,然后退火、酸洗,再磷化,再加润滑剂。.
某些大工厂用这样的方法每天能生产几十万个零件。挤压机每分钟挤压60 次一70次。
一般冷挤压加工前磷化处理的工艺程序如下:
用强碱液脱脂以除去上道工序带来的磷化膜和油脂。
冷流水清洗。用温水更好。
用硫酸酸洗。
热水清洗。
锌磷化处理。一般用N03-,NO2-作加速剂。
冷流水清洗。
用碱性溶液中和。
皂基活性润滑剂处理。
干燥(用热空气)。
铝及其合金使用适当的润滑剂,即使不经化学处理,也能很好地变形加工。但在某些加工较困难的情况下,还是需要有一层磷酸锌和磷酸铝的磷化膜。铝磷化的前处理比较复杂,但要获得良好的结果就必须严格按照工艺程序进行处理。因为铜、硅一类合金成分在碱性浸蚀时会析出,在进一步处理前必须把这些合金成分除去。下列程序是不可缺少的:
在含有有机络合物的强碱性溶液中腐蚀。有机络合物可以控制碱对铝的腐蚀,并可防止生成不溶物。
热水清洗。
用20%一30%硝酸溶液去污物。
冷水清洗。
用含有胶体钦盐的溶液做晶粒细化处理。
用含有氟化物的锌磷化液磷化。氟化物是用来溶解铝,并在铝超过溶解度极限时使之沉淀成为废渣。
冷水清洗。
中和处理。
浸于皂基润滑剂中处理。
干燥。
这种工艺得到的磷化膜膜重为2g/m2一7g/m2相当于1 – 5 μm,主要成分为三代磷酸锌。
目前趋向于用硝酸盐作加速剂,尤其是用硝酸锌作加速剂的磷化液代替用氯酸盐作加速剂的磷化液。这种磷化液的硝酸盐磷酸盐平衡自动再生亚硝酸根,所以溶液中不含亚铁离子。当然,这样就必须使用不同浓度的浓磷化液来配制槽液和补充槽液。此外,还必须十分小心控制温度(70℃一75℃)和槽液的组成(用酸度滴定法)。不过下面所述优点可以补偿这些不便之处。
从技术上看,用硝酸盐作催化剂的磷化液有下述优点:
磷化膜不含氯化物,因此在变形加工前和加工后都有较好的抗蚀性能; 磷化液不含亚铁,可以保证磷化膜的组成稳定; 即使生产量很大,也可以延长槽液的使用寿命; 磷化膜与金属结合极好,有良好的冷变形加工特性。
从经济上看,这种磷化液有下述优点:
处理每平方米金属表面消耗的化学材料较少;工具磨损较少; 沉渣较少,因而降低设备清理的频率,降低运转费用。
冷变形加工前表面处理除了在磷化液方面改进以外,对所用润滑剂也有许多改进。例如,除了使用皂类润滑剂外,还采用乳化矿物 ,极压添加剂、蜡等润滑剂。近来在某些特殊场合还有用磷化和润滑二合一槽液在金属表面生成活性复合润滑膜的。
必须知道,这些磷化液只适用于含有少量铬、镍、钥等合金元素的钢。处理不锈钢有一种工艺是先用草酸盐处理,然后再磷化。不过,应该指出,如果生产不锈钢丝,只用草酸盐处理,再加适当的润滑剂便可满足生产要求了。
磷化处理在变薄拉延加工方面的应用
深拉延熨平又称变薄拉延,这种技术是用冲头把金属板毛坯挤压通过一个模子,冲头与模子之间的间隙小于毛坯的厚度,这祥金属板毛坯便变薄拉延成杯状零件,这些零件的长度主要受压力机行程和毛坯直径的限制。许多产品是用这样的方法制造的,如扬声器壳体、灭火器筒体、制冷压缩机壳体、汽车发动机薄壁缸套等。
有许多变薄拉延加工,使用极压性能好的压延润滑剂就可以了。但当使用较厚的钢板毛坯或零件比较长时,就要考虑在拉延过程中有可能产生擦伤或熔合的危险,这会损坏工具和产生废品。在某些情况,需要采用先把毛坯压成杯,然后退火,再分次深拉延成型的工艺。为了防止在拉延过程中产生擦伤和熔合的故障,以及减少退火和拉延的次数,往往采用磷化膜作为润滑剂的底层构成复合润滑膜,这样处理可以获得非常好的效果。
冷变形加工前磷化工艺的新近发展
磷化与润滑同时进行的新工艺
20世纪70年代发展了一种磷化与润滑在一种溶液中同时进行的新工艺,如美国专利提出了一种磷化与润滑同时进行的组合物。这种组合物含有如下成分:
1)30%一70%(质量计)由C14一C24不饱和脂肪酸和一种胺H (NHCH2CH)n NH2(其中n =2-6)衍生的酰胺磷酸盐。
2)15%-55%烃基化合物,不干性甘油脂或由C14一C18脂肪酸和少于10个碳的链烷醇生成的酯。
3)3%一10%水。
4)2%一7%游离磷酸。
5)8%一15%己烯乙二醇或甲基甲酰胺,二甲基甲酰胺的磷酸盐
6)达5%的表面活性剂。
配制组合物时,先配好(1)然后与(2)、(5)和(6)混合。毛坯经一次磷化润滑处理便可连续进行几次冷变形加工。
美国专利提出一种含有乳化有机润滑剂的磷化液,使磷化和润滑处理同时进行。这种溶液可用于浸或喷的方法。该专利提出的溶液含有0.2%一15%磷酸根(质量计,下同);0.3%一16%乳化有机润滑剂,有机润滑剂选自C8~ C40羧酸与醇类组成的化合物,包括酯类、单胺盐和多胺盐、单烷基和多烷基(Cl – C18)胺盐及它们的混合物,1%-10%乳化剂,乳化剂选自具有1-5 丙烯胺基用的N-牛油多丙烯胺、噁唑啉,蜡及它们的混合物,0.1%-5%腐蚀抑制剂,抑制剂由C7-C8有机竣酸盐和最高达C12的脂族胺和水组成。用噁唑啉化合物作乳化剂可改善工作液的稳定性。操作温度可在26℃一93℃,最好为49-71℃。金属处理完后应在比较高的温度下干燥、
浓溶液具体配方如下:磷酸二氢锌2.6%;磷酸(75%): 5.6%;N-牛油聚丙烯四胺乳化剂2.0%;硬脂酸2.9%;部分氧化了的高分子量酸,酯和醇2:5%;1,3丙 二胺二油酸酯2.0%;三乙醇胺辛酸盐0.2%,余量为水。如果用噁唑啉代替N-牛油1,3丙二胺二油酸醋,可提高溶液的稳定性。
1份浓溶液加3份水稀释配成工作液。工作液加热至77℃便可使用。毛坯经脱脂、除锈、水洗干净后便可浸于工作液中,磷化润滑处理10mino烘干后便可进行冷变形加工
锰盐磷化
英国专利提出冷变形加工前用锰磷化代替通常采用的锌磷化,可解决锌磷化膜在高温(如焊接、退火)分解而产生的零件外表脏污问题。该专利提出的工艺包括下述四个步骤:
用无机酸酸洗。
用含有0.1g/L-8gg/L二代或三代磷酸锰悬浮液处理。
用磷酸锰或磷酸锰铁磷化液处理,使金属表面生成磷化膜。
用润滑剂处理,使金属表面形成润滑膜。
磷化膜增厚处理方法
英国专利提出一种含有氯酸盐加速剂和硫酸根离子的酸性磷酸锌溶液。硫酸根的存在可使磷化膜厚度增加50%左右,同时磷化膜与金属表面的粘结性能也有提高,特别适用于作为冷变形加工润滑剂的底层。
该专利提出的磷化液含有:Zn(浓度大于6g/L),P2O5(浓度大于5g/L),加速剂(以C103-计)(浓度大于lg/L,总酸大于20点,游离P2O5与总P2O5的质量比为0.2-0.6:1。特别是P205, Zn2 + ,CLO3-的质量比最好为1:0.5-4:0.1-1. 硫酸根用量为1g/L-50g/L,最好为5g/L-20g/L。磷化液可以单独使用氯酸盐作加速剂,在这种情况下,氯酸根含量不应少于1g/L。磷化液也可用氯酸盐和硝酸盐作加速剂,在这种情况,氯酸根和硝酸根离子之和必须不少于1g/L,硝酸根含量是以氯酸根氧化当量来计算的。有硝酸根存在总是有利的,P205, N03-质量比应为1:0.2—1:60氯酸根离子一般不超过5g/L,而以0.2g/L---2g/L为最好。磷化液最好含有铜离子,镍离子或钴离子,或者上述都有。镍离子量最好为5~ 1000mg/L, Cu2+最好为lmg/L一50mg/L。
配制磷化液时,可分别溶解各组分于水中,也可用稀释浓磷化的方法来配制,硫酸根则单独加入。磷化液的补充液最好使用浓缩液。补充液中五氧化二磷/锌离子/硝酸根/氯酸根应为1:(0.36一0.8) :(0.1一0.6) :(0.15一0.6),游离P2 05与总P2O5的比值为0.2:1-0.7:1
磷化最好在35℃一98℃进行,采用浸液法。磷化前可用热水洗或用胶体磷酸钛溶液活化金属表面。后处理一般用水洗,也可用钝化液处理。最后用润滑剂处理。
冷变形加工用的皂液润滑剂
冷变形加工磷化后使用的皂液可含有一种或多种可溶性碱金属皂或胺皂,也可以把难溶金属皂分散其中。例如,碱金属皂液可由C10 –C20饱和或不饱和脂肪酸的钠、钾或三乙醇胺盐组成。皂液浓度最好为5g/L一50g/L。适用作难溶金属皂的有前面讲到的脂肪酸的锌、锰、铅、钙、钡和镁盐。用量也可在5g/L--- 50g/L 范围内。皂液温度必须达到至少有部分碱金属皂以溶解状态存在的程度。一般而言,50℃一60℃是适宜的,与金属接触时间0.5min-5min。
当润滑剂以干粉的形式使用时,最合适的是硬脂酸钠和硬脂酸钙。
几种配方:
(1) 三乙醇胺油酸30g/L;硬脂酸锌10g/L ;使用温度 50℃ 处理时间 3min
(2) 硬脂酸钠50g/L ,硬脂酸钙 l0g/L ;使用温度 70℃; 处理时间 5min
(3) 硬脂酸钠 50g/L; 硬脂酸锌 5g/L ;硬脂酸钙 5g/L; 使用温度 75℃ 处理时间 5min
(4) )四亚乙基五胺 3.2(%,下同) 氢氧化钠 3 .5 油酸 22 .8 水 70 .5
(5) )三乙醇胺 5 . 氢氧化钠 1 .8 妥尔油 23.2 水 70.0
(6) 单乙醇胺 2 .8 氢氧化钠 2 .6 椰子脂酸 24 .7 水 70.
(7) 牛脂钠皂 16 .0 碳酸钾 20 .0 硼酸 20 .0 硼砂 38.0 聚乙烯醇(相对分子质量(6000) 6 .0
(8) )牛脂钠皂 15.0 硼砂 、85.0
(9) )单异丙醇胺 3 .0 氢氧化钾 1 . 大豆脂肪酸 23 .5 聚氧乙烯三油酸脂 8 水 64 .5
(10) )硬脂酸钠 45.0 亚硫酸钠 4.0 硼砂 38 .0 水 13 .0
(11) )氯化石蜡(50%氯) 20 ;SAE40润滑油 80
抗磨损磷化膜
磷化膜在防止钢铁零件摩擦面擦伤和减少磨损方面所起的作用
两个滑动摩擦接触的表面必须有一润滑膜隔开,如果在施加压力或切线应力时,这种膜被破坏,摩擦面便会严重地损坏,导致或迟或早地两个表面熔合卡住。 第二次世界大战前不久,除了对传统的润滑剂,如油、脂的改进,和引人如以二硫化钼为基础的各种新品种润滑剂以外,还认识到磷化膜作为润清剂底层的重要性。 1938年一1940年在美国出现的磷化工艺,在战争期间英国便采用了,而法国则在战争结束时,1945年才开始使用。这之前是利用传统的锌盐磷化或锰盐磷化,后来经验证明最好的抗磨损磷化膜是从含有磷酸和一代磷酸锰的磷化液中得到的。在1940年已经认识到镍在这类磷化液的重要性。
钢滑动面抗磨损磷化只用锰盐磷化,但磷化膜中含有磷酸镍更为有利。由于这类磷化所用的磷化液的氧化加速剂氧化性能较弱,磷化液中含有亚铁,所以得到的磷化膜含有硫酸锰和磷酸铁,还含有或不含有磷酸镍。磷化膜的主要成分为硫酸锰铁(Mn, Fe)5, H3 (P04 )4 .4H20,底层为氧化亚铁和磷酸亚铁。磷花膜中锰离子和铁离子比岁磷化液的组成而变。磷化液中铁的含量一般为1g/L-5g/L。在这方面已经证明,溶液中的亚铁含量不但影响磷化初期磷化液对金属的浸蚀速度, 而且影响结晶的成核和生长速度。
用四球机进行摩擦和熔合试验证明锰磷化膜的优越性能。这种试验是用一种有一定性能要求的钢制成的直径为12.7mm的钢球进行的。钢球的接触条件与轮齿接触相似。 三个球的磨损伤痕直径都按旋转方向(平行于伤痕线)和垂直方向测量,六个测量结果的算术平均值便是伤痕的平均直径,以毫米计。某些理由可以解释磷酸锰铁膜在这方面的优越性能。概括地说,这些理由有以下几点: (1)由于结晶膜具有良好的吸附性能,所以在金属表面能较好地保留润滑剂。 (2)由于磷化膜的非金属特性可以防止或延迟滑动面之间的局部熔化或扩散。(3)由于磷化膜的断面是波浪形的,所以滑动面以微表面接触,特别是在走合阶段更是如此。(4)磷化膜有足够的厚度(l0g/m2一15g/m2),又是非金属结晶层,能在某种程度上吸收应力。 (5)硫酸锰结晶石在酸性溶液中形成的,具有特殊结构,牢固地结合在基体金属上。
虽然最初的抗磨损磷化液的组成很简单,是磷酸和一代磷酸锰的溶液,但不久便进行某些改进。从1950年开始,对这种磷化液的使用条件已有足够的了解,可以加人硝酸盐一类的加速剂而不会把二价锰氧化成七价锰,即使是浓的磷化液也是这样。近来已经证明,这类磷化液可用硝酸根/亚硝酸跟离子对加速而不会影响稳定性,因而可以在没有铁离子的磷化液中磷化获得组成稳定的磷化膜。
抗磨损锰系磷化工艺
抗磨损磷化所用的磷化液一般比较浓,通常总酸度为40点一60点。酸度比(TA/FA)应在5-7的范围内,以保证磷化的金属表面有良好的活性。 同时,磷化过程是在比较高的温度下操作,常常接近于沸点(95℃一98’C ),如果操作条件不太合适,有时会破坏平衡。如果磷化液长时间保持在操作温度又不使用,便会发生水解反应,结果生成大量沉淀,溶液的游离酸度变得过高。锰磷化与锌磷化不同,磷酸锰结晶在85 -90℃难以成核和生长,所以必须在高温操作。 使用锰磷化液必然采用浸液磷化工艺,因为要求在高温下采用喷淋磷化实际上是不可能的。 要进行抗磨损磷化处理的零件,通常都是在铸造或热处理之后,又经过机械加工或其他方式加工处理的。经过这样处理的表面只要脱脂后便可以进行磷化处理了。1967年以前,要获得厚度适于装配间隙小的要求(径向4[μm.—8μm] ),结晶细而均匀的磷化膜只能用三氯乙烯、过氯乙烯或乳化清洗剂等一类有机溶剂脱脂,因为用碱脱脂或用酸去除钝化膜都会生成结晶粗大、不均匀、厚的磷化膜,以致影响装配。最广泛使用的磷化工艺程序如下:
使用适当的溶剂(三氯乙烯、汽油等)脱脂,或用有机溶剂与水构成的乳化液脱脂更好。使用乳化液时,脱脂温度可在20 -40℃范围内。
冷流水清洗。
热水清洗。
在95 -98℃的锰磷化液中磷化5min- 15min。
热水清洗,也可用铬酸溶液钝化或用弱碱性溶液中和。
干燥
浸润滑剂处理。
但用有机溶剂或乳化剂脱脂存在下述问题: ‘
脱脂以后用水清洗时,零件表面不被水润湿,因此难以正确判断表面清气洁度。
溶剂废液不易处理,脱脂液的浓度难以测定。
1967年出现一种新的前处理方法,可以用碱脱脂或酸洗都不会生成粗大和不均匀的磷酸盐结晶,这种方法就是用磷酸锰细结晶悬浮液预处理的方法。这种方法使锰磷化工艺具有更大的灵活性和适应性。 如果金属表面擦有研磨膏,只有用喷射碱液或乳化清洗剂的方法才能彻底清洗干净。如果零件热处理之后表面不再加工,表面的氧化物和氧化了的油未除去,零件脱脂后还必须用喷射磨料一类的方法处理,以除去氧化物和氧化油。可用气动喷枪把很细的二氧化硅磨料(40μm-10μm)、水和防锈剂的混合物,以很高的速度直接喷射到零件表面上除去脏物。也可用适当的酸洗方法把氧化物除去,还可以用专用脱脂剂处理这类油污。
抗磨损锰磷化工艺对提高摩擦零件的耐磨性能,防止擦伤、熔合,延长零件使用寿命等方而起重要的作用,已在许多工业领域广泛使用。例如,汽车工业可用这种工艺处理下述零件:后桥齿轮,变速箱的主动齿轮和行星齿轮,凸轮轴和推杆,摇臂轴和油泵,气阀,轴承座圈,轴销,活塞环,紧固件螺栓等。设备制造业也采用这种工艺处理零件,如钻井设备的管接头和套管(这种装置的紧固扭矩很大,因此要防止咬合和腐蚀)。工业和家庭冷冻压缩机所用的配对件间隙很小(以微米计),都经过精密加工,以保证安静地运转,可用这种锰磷化工艺处理的零件有活塞、连杆、滑板、曲轴。抗磨损磷化还可用于机床齿轮、武器装备,自动武器的滑动机构和粘结聚四氟乙烯的带体等的磷化。
抗磨损锰磷化工艺适用于普通钢和低合金钢,不适用于不锈钢、耐热钢,对于这些高合金钢应用草酸盐处理工艺。机械加工造成的表面状态往往使磷化产生困难,因为在表面形成了无定型拜尔比层(Beiby)金属表面经摩擦发热,遭到晶格的破坏或变形,扰乱了次表层,生成了钝化层。轧钢和铸钢对这种现象的敏感性,取决于它们自身的化学成分和结构状态。最麻烦的是铬、钼两元素的共同影响,经验证明,抗磨损锰磷化只能在镍,铬、钼和钒等元素的百分含量总和小于5%的钢上生成均匀的、粘结性能强的磷化膜;对于铸铁来说,也是如此。
磨削加工时,磨轮的沾污不利于磷化膜的形成,这可能是因为生成的表面金属夹杂物不易除去的缘故。如果发生这样的情况,就必须经常修整磨轮。当铬和钼等合金元素含量接近于上限时,必须严格控制磷化液的酸度,以免过度地浸蚀金属。严重过度浸蚀会影响金属的显微结构,同时会生成粘结力很弱的磷化膜,还会受到析出的碳化物的影响。
(1) 作为油或其他防蚀材料的底层。·
(2) 作为零件在有油或无油存在下接触面摩擦运动的润滑层,防止零件磨损和擦伤。
(3) 与拉延润滑剂结合用作冷变形加工的润滑层。
(4) 暂时的或短期的防锈。
(5) 作为塑料或橡胶与金属粘结的底层。
涂装前的磷化处理
磷化膜提高涂装涂层抗蚀性能的作用
很久以前,人们便发现磷化膜能提高钢铁类金属的防护性能。不过,如果不加后处理,磷化膜的防护性能是有限的。因此,通常金属表面经磷化处理后,还需根据实际使用情况进行钝化处理、涂油或涂漆以满足防蚀的要求。 任何涂漆金属制品的使用寿命主要决定于涂料层本身的耐久性能和漆膜与制品表面的附着性能。漆膜的主要作用是防止基体金属在其使用环境内发生腐蚀。 为了达到这个目标,制备金属表面处理的方法应能降低金属表面的活性,从而防止在漆膜与金属界面的膜下腐蚀。
磷化膜用作涂装底层可提高漆膜的附着性能,提高漆膜的耐潮湿和耐浸水性能,可以基本上阻止可能发生的腐蚀扩散。金属表面的金属或非金属覆膜损坏了之后,便会暴露出基体金属。由于基体金属的导电性和覆膜与基体之间的毛细管作用,在覆膜损坏的地方便构成微电池,基体便从这里开始腐蚀并向四面八方扩散出去。覆膜与基体之间的毛细管吸引电解液至覆膜下面,由此产生的膜下腐蚀导致覆膜起泡。金属表面磷化处理后,腐蚀过程便会被限制在覆膜损坏的地方,因为金属基体的其余部分为非导体的磷化膜所绝缘。磷化膜还与基体金属牢固地粘结在一起,因而可以防止电解液向水平方向扩散,从而抑制了膜下腐蚀。 涂装预处理中最基本的问题是磷化膜必须与底漆有良好的配套性,而磷化膜本身的防锈性是次要的。这一点是许多磷化液使用厂家最容易忽略的问题。在生产实践中,往往碰到厂家对磷化膜的性能要求不科学,片面要求磷化膜的防腐性能,他们要求越高越好,而对与漆膜配套性几乎不关心。涂装预处理中,磷化膜的主要功能在于作为金属基体和涂料(油漆)之间的中间介质,它提供了一个良好的吸附界面,将涂料(油漆)牢牢地覆盖在金属表面,同时细腻、光滑的磷化膜能提供5μm以上且防腐性能很好时,将这样的膜层送去作电泳漆,这会使我们几乎不能得到电泳漆膜。而磷化膜的防锈性能,只是提供一个工序间的防锈作用。另外,粗厚磷化膜会对漆膜的综合性能产生负效应。因此磷化体系与工艺的选定主要由工件材质、油锈程度、几何形状、磷化与油漆的时间间隔、磷化与涂装(油漆)层的配套性、底涂品种等条件决定。
一般情况下,对于有锈工件必须经过酸洗工序,而酸洗后的工件将给磷化带来诸多的麻烦。例如,工序间生锈泛黄、残留酸液的清洗、磷化膜出现粗化等。酸洗后的工件在进行锌系、锌锰系磷化前要进行表面调整处理。如果工件磷化后没有及时涂漆,那么当存放期超过10天以上,应采用中温磷化,磷化膜质量最好在1-5g/m2-5g/m2之间,此类磷化膜本身才具有较好的防锈性。磷化后的工件应立即烘干或用热水烫干,如果是自然晾干,易在夹缝、焊接处形成锈蚀。
在某些情况下,磷化后涂漆所得的复合膜的防护性能比金属覆膜的防腐性能还好。
漆前磷化工艺的发展概况
防腐蚀磷化所用的磷化液在1914年一1939年间有了较大的发展。( 在这一阶段,涂料涂装工业还未发展到目前的水平,磷化膜上的油漆涂层的防蚀效果十分依赖于磷化膜的质量。因此,在第二次世界大战期间主要努力于生产厚的磷化膜,使得金属与腐蚀环境尽可能地完全绝缘,如生成磷酸锰磷化膜的磷化工艺(称为Parkcrization工艺)。
1932年,出现薄膜防蚀磷化处理工艺(称为Bonderite工艺),标志着当时有关磷化观点的转变。从Bonderite这个词可知,注意力在于防护膜与基体粘结的因素,确定研究方向在于使磷化膜对金属具有最大的结合力,而且对漆膜也有很好的结合力。
除了工艺方法上的改进(如采用喷液方法磷化)以外,对于磷化液的研究则致力于生成既能满足与漆膜结合的要求又尽可能厚的磷化膜,使复合膜具有最大的防蚀性能。然而,发现这两个要求是互相矛盾的,即要得到与漆膜结合良好的性能就要求磷化膜薄,而要得到磷化膜良好的防护性能则要求磷化膜厚。
磷化膜是由脆性的结晶组成的,因此经过磷化的零件的任何大小变形都有可能使使之损坏,这对涂漆的零件更为有害。因为松脱的磷酸盐结晶会刺破漆膜而暴露出基体金属,这些漆膜与磷化膜脱落的地方会立即锈蚀。降低磷化膜的厚度可以提高磷化膜适应机械变形的能力。所以薄的磷化膜(1-5μm)最适用作油漆的底层。磷化膜越薄,涂在磷化膜上的漆膜的抗机械变形性能越高。-
事实上,经过不断的改进,现在已经可以采用最薄的磷化膜作油漆底层,而且对基体金属的防护性能即使在最坏的条件下仍然非常好。这种成就应归功于两方面的改进,即磷化的化学成分和结晶结构的改进,以及漆膜质量的不断改进。在这种情况下,倾向于采用一代磷酸钠之类的碱金属磷酸盐处理钢,这种方法又称为转化型磷化(生成无定形磷化膜)。这种方法得到的磷化膜含有氧化铁和磷酸铁,具有良好的防蚀性能,而且由于单位膜重轻(0 .5g/m2 --- 1 g/m2)大大改善了漆膜的粘结强度。不过,近几十年来,结晶磷化也得到不断的改进,现在已经可以获得极均匀的厚度为l- l .2μm(1. 5g/m2-2g/m2)的磷化膜。
20世纪70年代初期,美国发展了一种钢带连续涂漆技术。钢带先磷化后涂漆,所得复合膜可经受非常苛刻的冷变形加工而不脱落。用含有磷酸锌、磷酸镍和氟活化剂,并以硝酸根亚硝酸根作加速剂的磷化液磷化钢、铝和镀锌钢可以得到令人十分满意的磷化膜,只要磷化7s-10s,膜重便可达到1g/m2一3g/m2。证明结晶磷化工艺现在的适应性可以广泛满足各种不同工艺的要求。这种膜的性能很值得注意,即使涂漆的钢板变形了,这种膜仍然保持着有效的防烛性能。
漆前磷化工艺
漆前磷化工艺可分为两类: (1)结晶磷化,生成重金属磷酸盐结晶的磷化膜,通常为锌,锌/钙或锌、锰磷化。 (2)无定形磷化,以碱金属磷酸盐为主组成磷化液,生成含有氧化铁和磷酸铁的无定形磷化膜。用作油漆底层的磷化膜的膜重通常在0 . 2g/m2 --- 2.5g/m2范围内。一般地说,膜越重抗蚀性能越好,但其他性能,如漆膜的光泽和附着力则在上述膜重范围较轻的膜最好。锌磷化用于在腐蚀性较强的环境使用和在户外使用的制品上,如汽车车身、拖拉机机身板、洗衣机机壳等。无定形磷化用于腐蚀性不太强的环境使用和在户内使用的制品上,如钢制家俱、冷冻机机壳、荧光灯灯架等。
漆前锌系磷化液一般为以亚硝酸钠或氯酸钠加速的含有磷酸锌和硝酸盐的酸性溶液,通常还加有细化剂以期得到结晶细致密和附着力好的磷化膜,最常使用的细化剂是柠檬酸和酒石酸。有时还加有氟化物以改善磷化膜的均匀性,并使磷化液能用于由多种金属组成的部件的磷化。当对磷化膜或磷化液有特殊要求时,还可加人其他重金属,如镍、锰和钙等。磷化液中还可加人某些有机添加剂,使在加热器上形成的垢及沉渣软化便于除去。用这样的磷化液,通常在40℃一60℃喷液磷化,磷化时间为60s-90s,得到浅灰色结晶磷化膜,膜重一般为1.5g/m2一 3.5g/m2。现在采用的电泳涂漆技术要求磷化膜重最好在1.g/m2一2g/m2范围内,以期漆膜获得更好的粘结性能和抗碎石冲击性能。
锌系磷化液用锰盐改性可在较低温(25℃-35’C)下进行磷化,得到膜重约 2g/m2的磷化膜。 用于喷液磷化组成相似的磷化液,也可采用浸液法磷化。通常磷化温度为 30℃一50℃,磷化时间一般为2一5min。 经过改进的浸液法也可在低温(25℃一35℃)下进行磷化,生成膜重约为 2g/m2的磷化膜。 在浸液磷化的锌系磷化液中加入钙,可使零件经碱洗或酸洗后不经细化预处理也能获得细结晶的磷化膜,特别适合于作为涂漆的底层。
无定形磷化是用碱金属一代磷酸盐(一般为 钠或铵盐)处理钢铁零件,生成的磷化膜含有氧化铁和磷酸铁。这种溶液不加特殊的加速剂也可以磷化,不过这种溶液含有亚硝酸盐,钼酸盐,溴酸盐和氯酸盐等加速剂,也可以含有氟化物以适应由多种金属构成的组件磷化。这种溶液通常在30 -60℃磷化,用喷液法磷化约需lmin- 2min,得到的磷化膜膜重为0.4g/m2一 0 .7g /m2,与漆膜有良好的结合性能,有较好的抗蚀性能,但比锌磷化膜差一些。 在无定形磷化液中加入恰当的表面活性剂可使脱脂和磷化两个工序在同一溶液中同时进行。
零件经漆前磷化后还要进行水洗和后处理以提高抗蚀性能。后处理通常采用含有六价铬或含有六价铬和三价铬的溶液处理。随着阴极电泳涂漆技术的发展,已发现用只含三价铬的溶液作后处理很有好处,特别可以提高漆膜的附着力性能。
用作阴极电泳涂漆漆膜底层的磷化膜应具有下述特性
磷化膜必须均匀,只有均匀的磷化膜才有良好的抗蚀性能、良好的漆膜附着力和平滑的阴极涂漆漆膜。
磷化膜的结晶必须细并与基体牢固结合,只有这样的磷化膜才能使漆膜粘结牢固并有良好的抗碎石冲击性能。
P/(P+H)值要高,这也是要获得良好的抗蚀性能和附着力性能所必需的。P/(P十H)值代表锌磷化膜的组成,一般要求P比值大于等于85%。
膜重最好控制在1. 4g/m2 – 2.2g/m’范围内,这样漆膜可获得最佳的附着力性能。
表面没有锈和氧化皮的零件的电泳漆前磷化工艺程序一般如下:
脱脂、除去金属表面的油脂,保证金属表面在以后的步骤中能被处理液完全润湿。
冷流水清洗。
热水清洗。目的有二:除去脏物和预热零件以增加金属表面在磷化液中的初始活性。
表面调整。
磷化处理。
冷流水冲洗。
钝化后处理。
去离子水清洗。
电泳涂漆。
磷化有锈或氧化皮的零件时,需在脱脂水洗工序与磷化工序之间增加下述工序:
用适当的酸溶液或碱溶液(用于铝及其合金)清洗。
冷流水清洗。
细化结晶预处理。例如,用胶体钛盐溶液预处理。
上述工艺程序可用于喷液法和浸液法。汽车车身磷化处理还可以用喷浸结合的方法。
铝制品如果不采用阳极氧化或钝化处理,通常也用锌磷化处理。 磷化电镀镀锌钢或热渗镀锌钢,用含有锌和镍的磷化液处理时,可选用简单的或络合的氟化物作催化剂。
低温磷化工艺
近代大量生产的漆前磷化线趋向于采用低温磷化。现在已经有可在24℃浸或喷液磷化的无定形磷化液,生成膜重为0.44g/m2一0.66g/m2的磷化膜。锌磷化液已经能在38℃生成3.3g/m2一5.5g/m2膜重的磷化膜。用于电泳涂漆前磷化的锌磷化液已经能在25℃一35℃生成1.4g/m2一2.2g/m2膜重的磷化膜。 低温磷化可以大大降低能量消耗,还可节约加热系统的投资。
改用在24℃磷化工艺,除了需要供给泵的能量外不需要热量。两种工艺生成磷化膜的膜重均为0.44g/m2-0.5g/m2 。 虽然浸液磷化比喷液磷化热损失小得多,但是采用低温磷化也还是可以节约能量的。一般磷化温度在60℃以上时,热损失迅速增加。
防锈磷化(工序间或贮存零件防锈)
工序间或贮存零件的防锈磷化,通常要求用厚的磷化膜以求得到良好的防蚀性能。零件经磷化处理后还要浸油、脂或蜡以提高防蚀性能。 英国标准3189把在钢铁表面生成膜重大于7.5g/m2的铁、锰或锌磷化膜称为厚磷化膜。实际上,通常膜重在10g/m2--20g/m2范围内。在某些条件下,膜重常达40g/m2。防锈磷化可采用铁、锰或锌盐磷化。一般工艺程序为
脱脂;
水洗;
磷化(浸液法);
水洗;
后处理;
干燥;
封闭处理,浸于特殊的封闭液中处理。
防锈磷化处理工艺的选择由许多因素决定,如产品的类型、清洗的方法、设备情况及处理时间等。
市场上出售的封闭处理剂品种繁多,如脱水液与油,油在水中的乳化液,矿物油,蜡(使用前溶于石油溶剂)和水基石蜡等。如用脱水液与油处理剂或油在水中乳化液作封闭处理,零件可不经干燥便进行封闭处理。
冷变形加工前磷化的作用
磷化膜对冷变形加工的作用
磷化膜对钢冷变形加工的重要作用是F. Sinzer发现的。直到1945年,冷变形加工前磷化工艺主要用于武器制造方面,后来这种工艺才在各个领域飞速发展,应用厂家遍及金属与工具接触在压力和低温下塑性变形加工各方面。
冷变形加工涉及金属在各种工具(如拔丝模、冲头和冲模)之间的压力塑性变形问题。在这样的加工作业中,金属与模具的表面应力很高,显然接触表面之间的摩擦特性很重要,良好的润滑在变形加工过程中起重要的作用。与金属表面牢固结合的磷化膜加上矿物油或植物油之类的辅助润滑剂可以很好地解决金属表面与模具之间的摩擦问题。磷化膜晶间区的毛细管作用有利于润滑剂浸透磷化膜。后来又发现用皂基润滑剂代替润滑油效果更好。
把磷化处理过的钢毛坯浸于温热的,pH值为8一10的皂液中,当磷化膜为三代磷酸锌时会发生复分解生成锌皂、主代磷酸钠、三代磷酸钾或烷烃胺等。 使用这类润滑剂不仅金属变形加工更容易,而且大大降低了工具的磨损。 浸了润滑剂的磷化膜应视作可以移动于工具和金属表面的膜。因此,每通过一次加工,润滑膜就会损失一部分。许多研究工作者曾用放射性示踪方法研究金属变形加工过程中这种膜的损失情况,发现金属拉伸增长38%、润滑膜大概损失原有膜重的11%。德国研究工作者A. Durer的报告损失大一些,约为20%一50%。
虽然冷变形加工和热变形加工大不相同,但是不能忽视冷变形加工施加于金属的极高的应力能使金属温度上升到200℃左右。在这样的条件下,磷化膜就会脱水。例如,含四个分子水的锌磷化膜会损失两个分子水。M : Gebhardt认为这样的磷化膜便会出现劈裂平面,有助于晶体颗粒在表面滑动过程转移。
工业上用的冷变形加工钢和铝的磷化膜是以磷酸锌为主的,再浸硬脂酸锌,磷化膜的膜重为5g/m2-25g/m2,锌皂量为l00g/m2一150mg/m2。有时因为润滑皂 (如硬脂酸钠)过多而使总膜重增加,这样会使工具堵塞,如高生产率的拔丝加工有时会发生这种情况。如果出现这种情况,建议加完润滑剂后用水冲洗以除去过多的皂,水洗对不溶解的锌皂无影响。
磷化处理在拔管工业的应用
在长的或短的芯棒上拔管或空心拔管都涉及金属内外表面不同程度的变形。 在磷化工艺出现之前,管子毛坯经酸洗清洗后便浸于热的皂液或乳化润滑剂中处理,然后进行冷拔管,使管子横截面减少25%一30%左右。冷拔管子会使金属硬化,因此在进一步冷拔之前需要退火,然后再次进行酸洗、润滑剂等处理。自从采用了磷化处理工艺后便发现毛坯可以连续冷拔两次或三次而不需要退火处理。
磷化处理对冷拔管工业的好处有下列几点:
可以减少摩擦力,减少动力消耗,提高冷拔速度,速度范围为30m/rrin – 100m/min,平均速度为50m/min – 60m/min。冷拔无缝钢管时,每次冷拔可减缩截面尺寸40%左右。
不经退火可进行多次冷拔,这样便可以减少零件在工序间的来回传送次数,减少中间退火、酸洗、浸润滑剂等工序的次数,提高生产效率。
减少工具的磨损。
降低了管子表面的粗糙度,大大减少了由于焊合和擦伤造成的废品。
上述各点大大地提高了拔管工业的生产效率,显著降低了成本,给拔管工业带来了很大的经济效益。
冷拔管磷化处理的典型工艺如下:
毛坯用热硫酸或室温的盐酸酸洗。这道工序很重要,其目的是彻底除去退火处理时生成的氧化物或氧化皮,并使金属表面活化与磷化膜结合得更牢固。
冷流水清洗。
二次冷流水清洗,含有中和盐更好。
锌磷化(浸液法)。
冷流水清洗。
热水清洗,含有中和盐更好。
活性润滑剂处理。
干燥。
毛坯管束最好倾斜地进人槽液,待完全浸人后把管子的倾斜方向反过来,这样可以很快排出管子内面的空气,使管子内表面得到圆满的处理。管子外表面的完全润湿是靠槽底的摇架使管束松开来达到的。
关于上述的工艺程序,还必须作一些补充说明。 酸洗时由管子的表面状态、酸洗槽液的缓蚀程度、酸洗槽液被铁离子污染的程度等因素而定。对焊接管和要求得到“光亮管”的毛坯酸洗时间要短些。第((3)步 和第(6)步有时可在同一个槽内进行。 还必须强调,浸润滑剂前的第(6)步中和处理是很重要的。因为从磷化液出来的管子ph值为2---2.5,不能直接浸人pH值为9的润滑剂槽中,否则,碱性皂和磷化膜的反应就会受到影响,从而降低润滑效果。有时第(5)步清洗可以把毛坯送回第(3)步进行处理,但是在这种情况,第(6) 步的碱中和处理就是必不可少的了。浸润滑剂的时间以刚好能形成锌皂为宜,如,4min – 6min。浸渍时间太长会导致磷化膜被破坏。磷化膜与润滑剂反应,以及可能机械带入的杂质会污染润滑剂槽液,主要污染杂质为氢氧化铁,可由它本身的深棕色及润滑性能的丧失而看出来。把润滑剂槽液连续离心除去杂质可以延长槽液的使用寿命,保持满意的润滑性能,这是美国广泛使用的方法。
干燥过程必须把皂基润滑剂表面层的结合水全部去掉,通常使用热风吹入倾斜的室内使之干燥。
拔管工业使用的磷化液,长期使用氯酸盐作加速剂,最好和硝酸盐一起使用以得到膜重为5g/m2一l0g/m2的磷化膜。但是这类磷化液有时会严重腐蚀金属,因而不可能经常获得光亮的成品。
汽车减震器用的无缝钢管的表面粗糙度要求为5μm – 15μm (0.1μm -0.4μm) 。正是在这方面出现了大大改进了的磷化液。这些磷化液包括以磷酸锌,磷酸钙为基础,用硝酸盐/亚硝酸盐加速,并含有多磷酸盐作为细化剂的磷酸锌溶液。在这一特殊情况,总是希望能得到膜重为4g/m2一8g/m2,与金属牢固结合的磷化膜,而且金属的晶格又不为酸深度腐蚀。
过去普遍使用磷酸锌槽液,单独用硝酸盐加速,在含有铁的情况下磷化,近来明显地倾向于使用硝酸盐/亚硝酸盐加速的磷化液。这种溶液能自动催化再生亚硝酸根离子,因而溶液中不存在亚铁离子。这种系统的磷化液如果小心控制总酸度,可以得到非常好的结果。这种不含亚铁离子的磷化液的最大优点是,材料消耗少、沉渣少,因而与用氯酸盐加速的磷化液相比,可使用较长的时间才需要消除沉渣。
对于无缝钢管来说,所用磷化液生成的磷化膜只有几微米厚已足以冷拔一两次了。化学品消耗从60g/m2一70g/m2降到30g/m2一40g/m2 。焊接管也常用含有细化剂的磷化液处理,这样膜重可减至2g /m2。
磷化处理在拔丝工业的应用
正如拔管工业那样,拔丝工业也很快便认识到磷化对提高拔丝机的效率和改善产品质量有很大的益处。虽然过去冷拔低碳钢用粉状硬脂酸盐干润滑剂是没有什么困难的,但冷拔硬钢和冷镦大直径线材就需要借助于磷化处理了。
典型的工艺程序如下:
用盐酸或硫酸酸洗。
用冷流水清洗,可能的话最好用喷液法清洗。 一次冷流水清洗,用温水更好。
磷酸锌盐磷化处理。
冷流水清洗、用喷液法或洒水器冲洗更好。
用润滑剂槽液或用含有硼砂或石灰的悬浮液作后处理。
干燥。
金属线材可以成捆处理,也可以把线材拉开连续通过各种槽液进行处理,最后重绕成捆,还可以采用Helicof i1方法让线材沿卧式圆筒做螺旋运动连续磷化。采用连续磷化技术,通常只磷化20s-60s。这样短的磷化时间,要得到满意的结果, 必须提高总酸度到80点或120点。处理成捆的线材要求浸液磷化5-10min, 还要注意定期分开各圈以保证均匀处理。
有些处理粗冷镦线材的连续生产线只用研磨或喷砂的方法作表面处理,然后用热水喷淋冲洗和磷化几十秒钟。磷化液总酸度达到60点。 连续磷化完全有可能在20s-40s内得到4g/m2一6g/m2膜重的磷化膜。传统的线材成捆浸液磷化所得磷化膜的膜重通常为5g/m2一l0g /m2。 线材拔丝前磷化也长期使用以氯酸盐或氯酸盐与硝酸盐作加速剂的磷化液。这种磷化液虽然操作简单,但化学药品消耗量大,同时生成大量的沉渣,所以后来只采用以硝酸盐作加速剂的磷化液。但是,这样又因磷化膜中含有磷酸铁,所以拔丝模很快便损坏了。
过去几年有采用自动再生NO2-以N03- ,NO2-离子对作加速剂的磷化液的趋势。调整操作条件可以使磷化膜膜重在5g/m2一15g/m2范围内,而用氯酸盐作加速剂的磷化液所得磷化膜膜重为4g/m2一8g/m2。这种磷化液还有下述优点、 ①化学材料消耗少;②形成沉淀少;③工具磨损较少;④磷化膜质量稳定;⑤由于不含氯离子,防锈性能更好些。
磷化后拔丝,线材截面可在连续拔8次一16次后缩小至原来的10%以下,拔丝速度可达1000m/min,由此可见磷化处理可给拔丝工业带很大的经济效益。 与线材处理有关的冷镦螺栓滚压加工等方面发展得很快,磷化处理在这方面可能会由于使用合金含量更高的合金钢材料而使磷化成膜困难。 用于这方面的磷化膜必须能经受相当大的变形,而且在送到冷镦机之前还会受到最后的校形处理。所以在校形之前磷化膜必须是高强度的,而且膜重应达到 20g/m2- 30g/m2。目前使用的含有促进磷酸锌生长的催化剂的磷化液获得一定的成功。这样的磷化液可以处理含碳0.15% -0.35%(有时达到1%),铬0.5%一 1.5%,锰、钼、镍0.6%一1.2%的钢。
磷化处理在冷挤压加工方面的应用-
冷挤压加工涉及用高达4000t – 6000t的压力使金属塑性变形的问题。磷化使钢冷挤压加工成为可能。如果考虑到这种工艺迅速发展的情况,便可以认识到这不是一件小事。A. A. Dykiel对冷挤压工艺所作的经济分析表明,1950年美国用这种工艺生产的产品是很少的,但到1965年便达到了320000t。联邦德国则从1950年的2000t增加到1965年的180000t。美国市场1970年一1980年间达 1000000t.
在第二次世界大战时,冷挤压技术主要是在德国发展起来的,直到1947年这种技术才出现在法国,尤其是美国花了很大的投资使这种技术大规模地发展起来。 由于冶金工业的普遍进步和工具设计的改进,包括使用高速钢和碳化钨制成的冲头和模具,挤压机的生产效率不断地提高。不过,尽管如此,如果没有磷化工艺的作用,在高达150kgf /rnm2 --- 200 kgf /rnm2 (1500Mpa.- 2000Mpa)压力下,金属流动的问题仍然是难以应付的。现在冷挤压工艺已经能够应用于软钢、超软钢、碳钢、合金钢等材料的挤压加工上。
挤压小零件时,使用从钢棒上切下来的、直径准确的钢坯。钢坯在冷挤压前先用碱性清洗液除去上一道工序带来的磷酸盐和润滑剂,然后退火、酸洗,再磷化,再加润滑剂。.
某些大工厂用这样的方法每天能生产几十万个零件。挤压机每分钟挤压60 次一70次。
一般冷挤压加工前磷化处理的工艺程序如下:
用强碱液脱脂以除去上道工序带来的磷化膜和油脂。
冷流水清洗。用温水更好。
用硫酸酸洗。
热水清洗。
锌磷化处理。一般用N03-,NO2-作加速剂。
冷流水清洗。
用碱性溶液中和。
皂基活性润滑剂处理。
干燥(用热空气)。
铝及其合金使用适当的润滑剂,即使不经化学处理,也能很好地变形加工。但在某些加工较困难的情况下,还是需要有一层磷酸锌和磷酸铝的磷化膜。铝磷化的前处理比较复杂,但要获得良好的结果就必须严格按照工艺程序进行处理。因为铜、硅一类合金成分在碱性浸蚀时会析出,在进一步处理前必须把这些合金成分除去。下列程序是不可缺少的:
在含有有机络合物的强碱性溶液中腐蚀。有机络合物可以控制碱对铝的腐蚀,并可防止生成不溶物。
热水清洗。
用20%一30%硝酸溶液去污物。
冷水清洗。
用含有胶体钦盐的溶液做晶粒细化处理。
用含有氟化物的锌磷化液磷化。氟化物是用来溶解铝,并在铝超过溶解度极限时使之沉淀成为废渣。
冷水清洗。
中和处理。
浸于皂基润滑剂中处理。
干燥。
这种工艺得到的磷化膜膜重为2g/m2一7g/m2相当于1 – 5 μm,主要成分为三代磷酸锌。
目前趋向于用硝酸盐作加速剂,尤其是用硝酸锌作加速剂的磷化液代替用氯酸盐作加速剂的磷化液。这种磷化液的硝酸盐磷酸盐平衡自动再生亚硝酸根,所以溶液中不含亚铁离子。当然,这样就必须使用不同浓度的浓磷化液来配制槽液和补充槽液。此外,还必须十分小心控制温度(70℃一75℃)和槽液的组成(用酸度滴定法)。不过下面所述优点可以补偿这些不便之处。
从技术上看,用硝酸盐作催化剂的磷化液有下述优点:
磷化膜不含氯化物,因此在变形加工前和加工后都有较好的抗蚀性能; 磷化液不含亚铁,可以保证磷化膜的组成稳定; 即使生产量很大,也可以延长槽液的使用寿命; 磷化膜与金属结合极好,有良好的冷变形加工特性。
从经济上看,这种磷化液有下述优点:
处理每平方米金属表面消耗的化学材料较少;工具磨损较少; 沉渣较少,因而降低设备清理的频率,降低运转费用。
冷变形加工前表面处理除了在磷化液方面改进以外,对所用润滑剂也有许多改进。例如,除了使用皂类润滑剂外,还采用乳化矿物 ,极压添加剂、蜡等润滑剂。近来在某些特殊场合还有用磷化和润滑二合一槽液在金属表面生成活性复合润滑膜的。
必须知道,这些磷化液只适用于含有少量铬、镍、钥等合金元素的钢。处理不锈钢有一种工艺是先用草酸盐处理,然后再磷化。不过,应该指出,如果生产不锈钢丝,只用草酸盐处理,再加适当的润滑剂便可满足生产要求了。
磷化处理在变薄拉延加工方面的应用
深拉延熨平又称变薄拉延,这种技术是用冲头把金属板毛坯挤压通过一个模子,冲头与模子之间的间隙小于毛坯的厚度,这祥金属板毛坯便变薄拉延成杯状零件,这些零件的长度主要受压力机行程和毛坯直径的限制。许多产品是用这样的方法制造的,如扬声器壳体、灭火器筒体、制冷压缩机壳体、汽车发动机薄壁缸套等。
有许多变薄拉延加工,使用极压性能好的压延润滑剂就可以了。但当使用较厚的钢板毛坯或零件比较长时,就要考虑在拉延过程中有可能产生擦伤或熔合的危险,这会损坏工具和产生废品。在某些情况,需要采用先把毛坯压成杯,然后退火,再分次深拉延成型的工艺。为了防止在拉延过程中产生擦伤和熔合的故障,以及减少退火和拉延的次数,往往采用磷化膜作为润滑剂的底层构成复合润滑膜,这样处理可以获得非常好的效果。
冷变形加工前磷化工艺的新近发展
磷化与润滑同时进行的新工艺
20世纪70年代发展了一种磷化与润滑在一种溶液中同时进行的新工艺,如美国专利提出了一种磷化与润滑同时进行的组合物。这种组合物含有如下成分:
1)30%一70%(质量计)由C14一C24不饱和脂肪酸和一种胺H (NHCH2CH)n NH2(其中n =2-6)衍生的酰胺磷酸盐。
2)15%-55%烃基化合物,不干性甘油脂或由C14一C18脂肪酸和少于10个碳的链烷醇生成的酯。
3)3%一10%水。
4)2%一7%游离磷酸。
5)8%一15%己烯乙二醇或甲基甲酰胺,二甲基甲酰胺的磷酸盐
6)达5%的表面活性剂。
配制组合物时,先配好(1)然后与(2)、(5)和(6)混合。毛坯经一次磷化润滑处理便可连续进行几次冷变形加工。
美国专利提出一种含有乳化有机润滑剂的磷化液,使磷化和润滑处理同时进行。这种溶液可用于浸或喷的方法。该专利提出的溶液含有0.2%一15%磷酸根(质量计,下同);0.3%一16%乳化有机润滑剂,有机润滑剂选自C8~ C40羧酸与醇类组成的化合物,包括酯类、单胺盐和多胺盐、单烷基和多烷基(Cl – C18)胺盐及它们的混合物,1%-10%乳化剂,乳化剂选自具有1-5 丙烯胺基用的N-牛油多丙烯胺、噁唑啉,蜡及它们的混合物,0.1%-5%腐蚀抑制剂,抑制剂由C7-C8有机竣酸盐和最高达C12的脂族胺和水组成。用噁唑啉化合物作乳化剂可改善工作液的稳定性。操作温度可在26℃一93℃,最好为49-71℃。金属处理完后应在比较高的温度下干燥、
浓溶液具体配方如下:磷酸二氢锌2.6%;磷酸(75%): 5.6%;N-牛油聚丙烯四胺乳化剂2.0%;硬脂酸2.9%;部分氧化了的高分子量酸,酯和醇2:5%;1,3丙 二胺二油酸酯2.0%;三乙醇胺辛酸盐0.2%,余量为水。如果用噁唑啉代替N-牛油1,3丙二胺二油酸醋,可提高溶液的稳定性。
1份浓溶液加3份水稀释配成工作液。工作液加热至77℃便可使用。毛坯经脱脂、除锈、水洗干净后便可浸于工作液中,磷化润滑处理10mino烘干后便可进行冷变形加工
锰盐磷化
英国专利提出冷变形加工前用锰磷化代替通常采用的锌磷化,可解决锌磷化膜在高温(如焊接、退火)分解而产生的零件外表脏污问题。该专利提出的工艺包括下述四个步骤:
用无机酸酸洗。
用含有0.1g/L-8gg/L二代或三代磷酸锰悬浮液处理。
用磷酸锰或磷酸锰铁磷化液处理,使金属表面生成磷化膜。
用润滑剂处理,使金属表面形成润滑膜。
磷化膜增厚处理方法
英国专利提出一种含有氯酸盐加速剂和硫酸根离子的酸性磷酸锌溶液。硫酸根的存在可使磷化膜厚度增加50%左右,同时磷化膜与金属表面的粘结性能也有提高,特别适用于作为冷变形加工润滑剂的底层。
该专利提出的磷化液含有:Zn(浓度大于6g/L),P2O5(浓度大于5g/L),加速剂(以C103-计)(浓度大于lg/L,总酸大于20点,游离P2O5与总P2O5的质量比为0.2-0.6:1。特别是P205, Zn2 + ,CLO3-的质量比最好为1:0.5-4:0.1-1. 硫酸根用量为1g/L-50g/L,最好为5g/L-20g/L。磷化液可以单独使用氯酸盐作加速剂,在这种情况下,氯酸根含量不应少于1g/L。磷化液也可用氯酸盐和硝酸盐作加速剂,在这种情况,氯酸根和硝酸根离子之和必须不少于1g/L,硝酸根含量是以氯酸根氧化当量来计算的。有硝酸根存在总是有利的,P205, N03-质量比应为1:0.2—1:60氯酸根离子一般不超过5g/L,而以0.2g/L---2g/L为最好。磷化液最好含有铜离子,镍离子或钴离子,或者上述都有。镍离子量最好为5~ 1000mg/L, Cu2+最好为lmg/L一50mg/L。
配制磷化液时,可分别溶解各组分于水中,也可用稀释浓磷化的方法来配制,硫酸根则单独加入。磷化液的补充液最好使用浓缩液。补充液中五氧化二磷/锌离子/硝酸根/氯酸根应为1:(0.36一0.8) :(0.1一0.6) :(0.15一0.6),游离P2 05与总P2O5的比值为0.2:1-0.7:1
磷化最好在35℃一98℃进行,采用浸液法。磷化前可用热水洗或用胶体磷酸钛溶液活化金属表面。后处理一般用水洗,也可用钝化液处理。最后用润滑剂处理。
冷变形加工用的皂液润滑剂
冷变形加工磷化后使用的皂液可含有一种或多种可溶性碱金属皂或胺皂,也可以把难溶金属皂分散其中。例如,碱金属皂液可由C10 –C20饱和或不饱和脂肪酸的钠、钾或三乙醇胺盐组成。皂液浓度最好为5g/L一50g/L。适用作难溶金属皂的有前面讲到的脂肪酸的锌、锰、铅、钙、钡和镁盐。用量也可在5g/L--- 50g/L 范围内。皂液温度必须达到至少有部分碱金属皂以溶解状态存在的程度。一般而言,50℃一60℃是适宜的,与金属接触时间0.5min-5min。
当润滑剂以干粉的形式使用时,最合适的是硬脂酸钠和硬脂酸钙。
几种配方:
(1) 三乙醇胺油酸30g/L;硬脂酸锌10g/L ;使用温度 50℃ 处理时间 3min
(2) 硬脂酸钠50g/L ,硬脂酸钙 l0g/L ;使用温度 70℃; 处理时间 5min
(3) 硬脂酸钠 50g/L; 硬脂酸锌 5g/L ;硬脂酸钙 5g/L; 使用温度 75℃ 处理时间 5min
(4) )四亚乙基五胺 3.2(%,下同) 氢氧化钠 3 .5 油酸 22 .8 水 70 .5
(5) )三乙醇胺 5 . 氢氧化钠 1 .8 妥尔油 23.2 水 70.0
(6) 单乙醇胺 2 .8 氢氧化钠 2 .6 椰子脂酸 24 .7 水 70.
(7) 牛脂钠皂 16 .0 碳酸钾 20 .0 硼酸 20 .0 硼砂 38.0 聚乙烯醇(相对分子质量(6000) 6 .0
(8) )牛脂钠皂 15.0 硼砂 、85.0
(9) )单异丙醇胺 3 .0 氢氧化钾 1 . 大豆脂肪酸 23 .5 聚氧乙烯三油酸脂 8 水 64 .5
(10) )硬脂酸钠 45.0 亚硫酸钠 4.0 硼砂 38 .0 水 13 .0
(11) )氯化石蜡(50%氯) 20 ;SAE40润滑油 80
抗磨损磷化膜
磷化膜在防止钢铁零件摩擦面擦伤和减少磨损方面所起的作用
两个滑动摩擦接触的表面必须有一润滑膜隔开,如果在施加压力或切线应力时,这种膜被破坏,摩擦面便会严重地损坏,导致或迟或早地两个表面熔合卡住。 第二次世界大战前不久,除了对传统的润滑剂,如油、脂的改进,和引人如以二硫化钼为基础的各种新品种润滑剂以外,还认识到磷化膜作为润清剂底层的重要性。 1938年一1940年在美国出现的磷化工艺,在战争期间英国便采用了,而法国则在战争结束时,1945年才开始使用。这之前是利用传统的锌盐磷化或锰盐磷化,后来经验证明最好的抗磨损磷化膜是从含有磷酸和一代磷酸锰的磷化液中得到的。在1940年已经认识到镍在这类磷化液的重要性。
钢滑动面抗磨损磷化只用锰盐磷化,但磷化膜中含有磷酸镍更为有利。由于这类磷化所用的磷化液的氧化加速剂氧化性能较弱,磷化液中含有亚铁,所以得到的磷化膜含有硫酸锰和磷酸铁,还含有或不含有磷酸镍。磷化膜的主要成分为硫酸锰铁(Mn, Fe)5, H3 (P04 )4 .4H20,底层为氧化亚铁和磷酸亚铁。磷花膜中锰离子和铁离子比岁磷化液的组成而变。磷化液中铁的含量一般为1g/L-5g/L。在这方面已经证明,溶液中的亚铁含量不但影响磷化初期磷化液对金属的浸蚀速度, 而且影响结晶的成核和生长速度。
用四球机进行摩擦和熔合试验证明锰磷化膜的优越性能。这种试验是用一种有一定性能要求的钢制成的直径为12.7mm的钢球进行的。钢球的接触条件与轮齿接触相似。 三个球的磨损伤痕直径都按旋转方向(平行于伤痕线)和垂直方向测量,六个测量结果的算术平均值便是伤痕的平均直径,以毫米计。某些理由可以解释磷酸锰铁膜在这方面的优越性能。概括地说,这些理由有以下几点: (1)由于结晶膜具有良好的吸附性能,所以在金属表面能较好地保留润滑剂。 (2)由于磷化膜的非金属特性可以防止或延迟滑动面之间的局部熔化或扩散。(3)由于磷化膜的断面是波浪形的,所以滑动面以微表面接触,特别是在走合阶段更是如此。(4)磷化膜有足够的厚度(l0g/m2一15g/m2),又是非金属结晶层,能在某种程度上吸收应力。 (5)硫酸锰结晶石在酸性溶液中形成的,具有特殊结构,牢固地结合在基体金属上。
虽然最初的抗磨损磷化液的组成很简单,是磷酸和一代磷酸锰的溶液,但不久便进行某些改进。从1950年开始,对这种磷化液的使用条件已有足够的了解,可以加人硝酸盐一类的加速剂而不会把二价锰氧化成七价锰,即使是浓的磷化液也是这样。近来已经证明,这类磷化液可用硝酸根/亚硝酸跟离子对加速而不会影响稳定性,因而可以在没有铁离子的磷化液中磷化获得组成稳定的磷化膜。
抗磨损锰系磷化工艺
抗磨损磷化所用的磷化液一般比较浓,通常总酸度为40点一60点。酸度比(TA/FA)应在5-7的范围内,以保证磷化的金属表面有良好的活性。 同时,磷化过程是在比较高的温度下操作,常常接近于沸点(95℃一98’C ),如果操作条件不太合适,有时会破坏平衡。如果磷化液长时间保持在操作温度又不使用,便会发生水解反应,结果生成大量沉淀,溶液的游离酸度变得过高。锰磷化与锌磷化不同,磷酸锰结晶在85 -90℃难以成核和生长,所以必须在高温操作。 使用锰磷化液必然采用浸液磷化工艺,因为要求在高温下采用喷淋磷化实际上是不可能的。 要进行抗磨损磷化处理的零件,通常都是在铸造或热处理之后,又经过机械加工或其他方式加工处理的。经过这样处理的表面只要脱脂后便可以进行磷化处理了。1967年以前,要获得厚度适于装配间隙小的要求(径向4[μm.—8μm] ),结晶细而均匀的磷化膜只能用三氯乙烯、过氯乙烯或乳化清洗剂等一类有机溶剂脱脂,因为用碱脱脂或用酸去除钝化膜都会生成结晶粗大、不均匀、厚的磷化膜,以致影响装配。最广泛使用的磷化工艺程序如下:
使用适当的溶剂(三氯乙烯、汽油等)脱脂,或用有机溶剂与水构成的乳化液脱脂更好。使用乳化液时,脱脂温度可在20 -40℃范围内。
冷流水清洗。
热水清洗。
在95 -98℃的锰磷化液中磷化5min- 15min。
热水清洗,也可用铬酸溶液钝化或用弱碱性溶液中和。
干燥
浸润滑剂处理。
但用有机溶剂或乳化剂脱脂存在下述问题: ‘
脱脂以后用水清洗时,零件表面不被水润湿,因此难以正确判断表面清气洁度。
溶剂废液不易处理,脱脂液的浓度难以测定。
1967年出现一种新的前处理方法,可以用碱脱脂或酸洗都不会生成粗大和不均匀的磷酸盐结晶,这种方法就是用磷酸锰细结晶悬浮液预处理的方法。这种方法使锰磷化工艺具有更大的灵活性和适应性。 如果金属表面擦有研磨膏,只有用喷射碱液或乳化清洗剂的方法才能彻底清洗干净。如果零件热处理之后表面不再加工,表面的氧化物和氧化了的油未除去,零件脱脂后还必须用喷射磨料一类的方法处理,以除去氧化物和氧化油。可用气动喷枪把很细的二氧化硅磨料(40μm-10μm)、水和防锈剂的混合物,以很高的速度直接喷射到零件表面上除去脏物。也可用适当的酸洗方法把氧化物除去,还可以用专用脱脂剂处理这类油污。
抗磨损锰磷化工艺对提高摩擦零件的耐磨性能,防止擦伤、熔合,延长零件使用寿命等方而起重要的作用,已在许多工业领域广泛使用。例如,汽车工业可用这种工艺处理下述零件:后桥齿轮,变速箱的主动齿轮和行星齿轮,凸轮轴和推杆,摇臂轴和油泵,气阀,轴承座圈,轴销,活塞环,紧固件螺栓等。设备制造业也采用这种工艺处理零件,如钻井设备的管接头和套管(这种装置的紧固扭矩很大,因此要防止咬合和腐蚀)。工业和家庭冷冻压缩机所用的配对件间隙很小(以微米计),都经过精密加工,以保证安静地运转,可用这种锰磷化工艺处理的零件有活塞、连杆、滑板、曲轴。抗磨损磷化还可用于机床齿轮、武器装备,自动武器的滑动机构和粘结聚四氟乙烯的带体等的磷化。
抗磨损锰磷化工艺适用于普通钢和低合金钢,不适用于不锈钢、耐热钢,对于这些高合金钢应用草酸盐处理工艺。机械加工造成的表面状态往往使磷化产生困难,因为在表面形成了无定型拜尔比层(Beiby)金属表面经摩擦发热,遭到晶格的破坏或变形,扰乱了次表层,生成了钝化层。轧钢和铸钢对这种现象的敏感性,取决于它们自身的化学成分和结构状态。最麻烦的是铬、钼两元素的共同影响,经验证明,抗磨损锰磷化只能在镍,铬、钼和钒等元素的百分含量总和小于5%的钢上生成均匀的、粘结性能强的磷化膜;对于铸铁来说,也是如此。
磨削加工时,磨轮的沾污不利于磷化膜的形成,这可能是因为生成的表面金属夹杂物不易除去的缘故。如果发生这样的情况,就必须经常修整磨轮。当铬和钼等合金元素含量接近于上限时,必须严格控制磷化液的酸度,以免过度地浸蚀金属。严重过度浸蚀会影响金属的显微结构,同时会生成粘结力很弱的磷化膜,还会受到析出的碳化物的影响。
还有剩余内容未读
@ 元本咨询

声明:说化有益·表面处理联盟网资料文库文档均为用户分享上传,版权归上传者所有。文档内容是行业专业性知识,知识的严谨度及实用性极强,因此部分价值极高的文章需要付费查看,用户可根据实际需求进行已付费文档下载;付费记录可在“用户中心”-“我的订单”-“我的文库”内查看。由于知识产权的特殊性,付费成功后不支持退换,用户应根据自身需求判断是否需要继续操作。
我们欢迎各方(自)媒体、机构转载、引用我们原创内容,但需严格注明来源。同时,我们也倡导尊重与保护知识产权,如发现文章内容涉及侵权,请通过在线咨询进行投诉,我们会在第一时间核实处理。